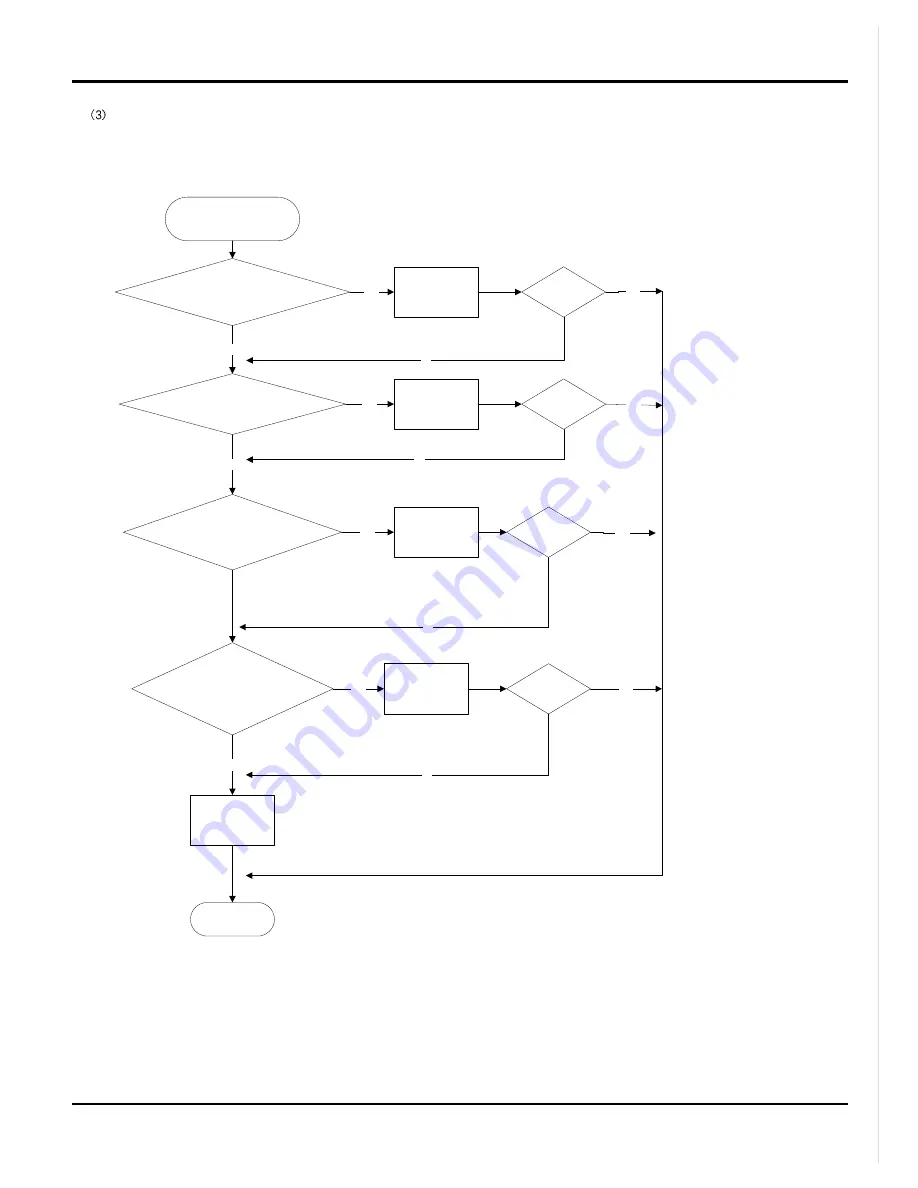
43
Troubleshooting
Start
Poor air return in the indoor unit
Solve the
corresponding
system problem
Eliminate the
malfunction
The fan speed is abnormal
Solve the
corresponding
speed problem
Eliminate the
malfunction
Evaporator is dirty
Clean the
evaporator
Solve the
problem
End
no
yes
yes
no
System is normal, but the indoor tube
temperature sensor
Is abnormal
Replace the
temperature
sensor
Solve the
problem
no
no
Replace the
controller
yes
yes
yes
yes
yes
yes
no
no
no
Troubleshooting for antifreezing protection (E2)
Malfunction diagnosis flowchart:
Summary of Contents for GWC36LB-D1NNA2A/I
Page 1: ...5 75 33 1 6 1 2 8 6HUYLFH 0DQXDO 02 11 11 5HIULJHUDQW 5...
Page 12: ...9 840 1018 412 3 2 Outdoor Unit Constrction views 572 950 378...
Page 35: ...32 8 Exploded Views and Parts List 8 1 Indoor Unit Exploded Views and Parts list...
Page 38: ...35 Exploded Views and Parts list GWC36LB D1NNA2A O 8 2 Outdoor Unit...
Page 40: ...37 Exploded Views and Parts list GWH36LB D1NNA2A O...