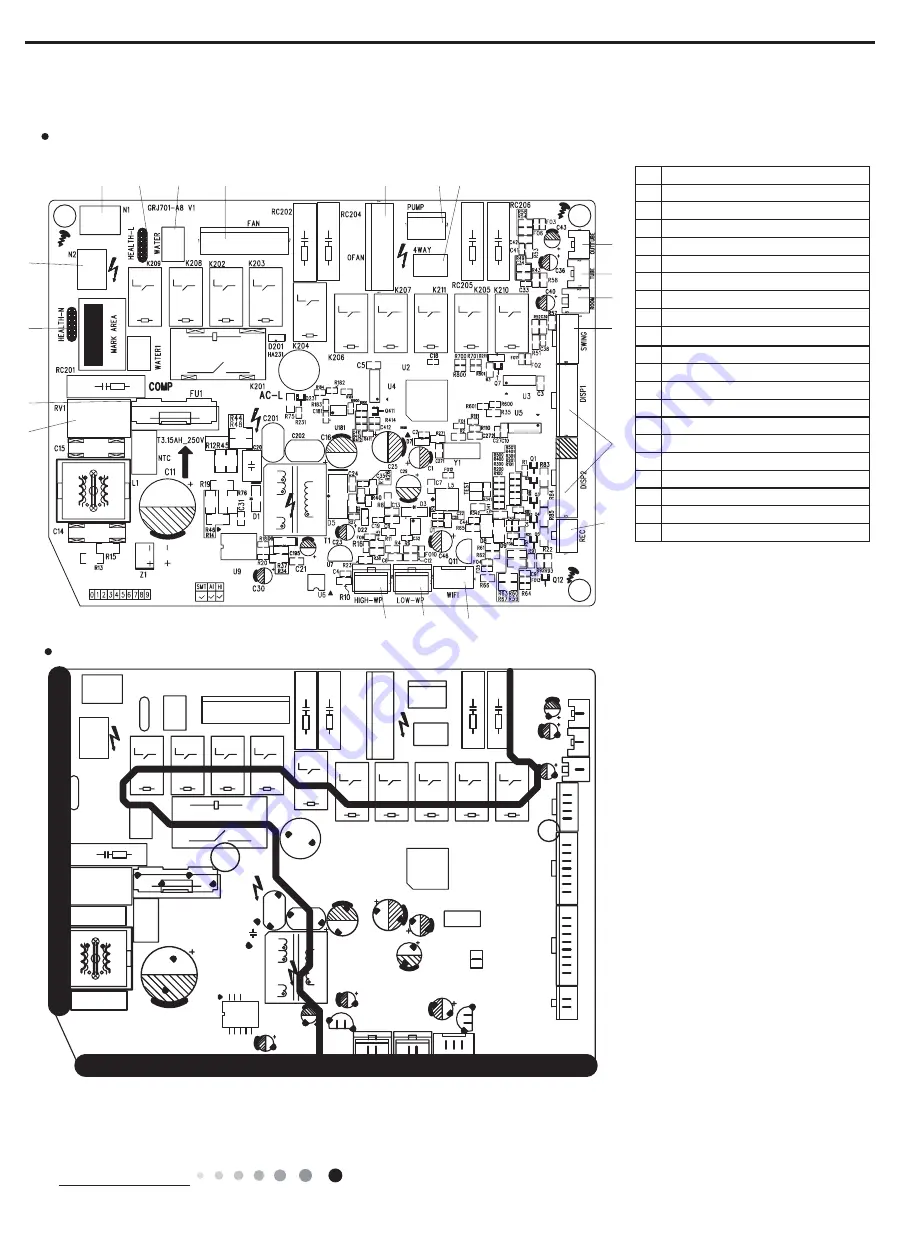
25
Technical Information
Service Manual
5.2 PCB Printed Diagram
TOP VIEW
BOTTOM VIEW
(1)Silk screen on main board
1
2
3
4
5
6
7
8
9
10 11
12
13
14
16
17
18
19
20
15
No.
Name
1 Piezoresistor
2 Fuse
3 Copper fin Health of neutral wire
4 Copper fin N2 of neutral wire
5 Copper fin N1 of neutral wire
6 Copper fin Health of live wire
7 Copper fin water of motor
8 Indoor fan
9 Outdoor fan
10 Water Pump terminal
11 4-WAY valve terminal
12 Outtube temperature sensor
13 Tube temperature sensor
14 Ambient temperature sensor
15 Swing terminal
16 Interface of display board
17 Interface of remoter
18 Interface of wifi board
19 Low water level
20 High water level