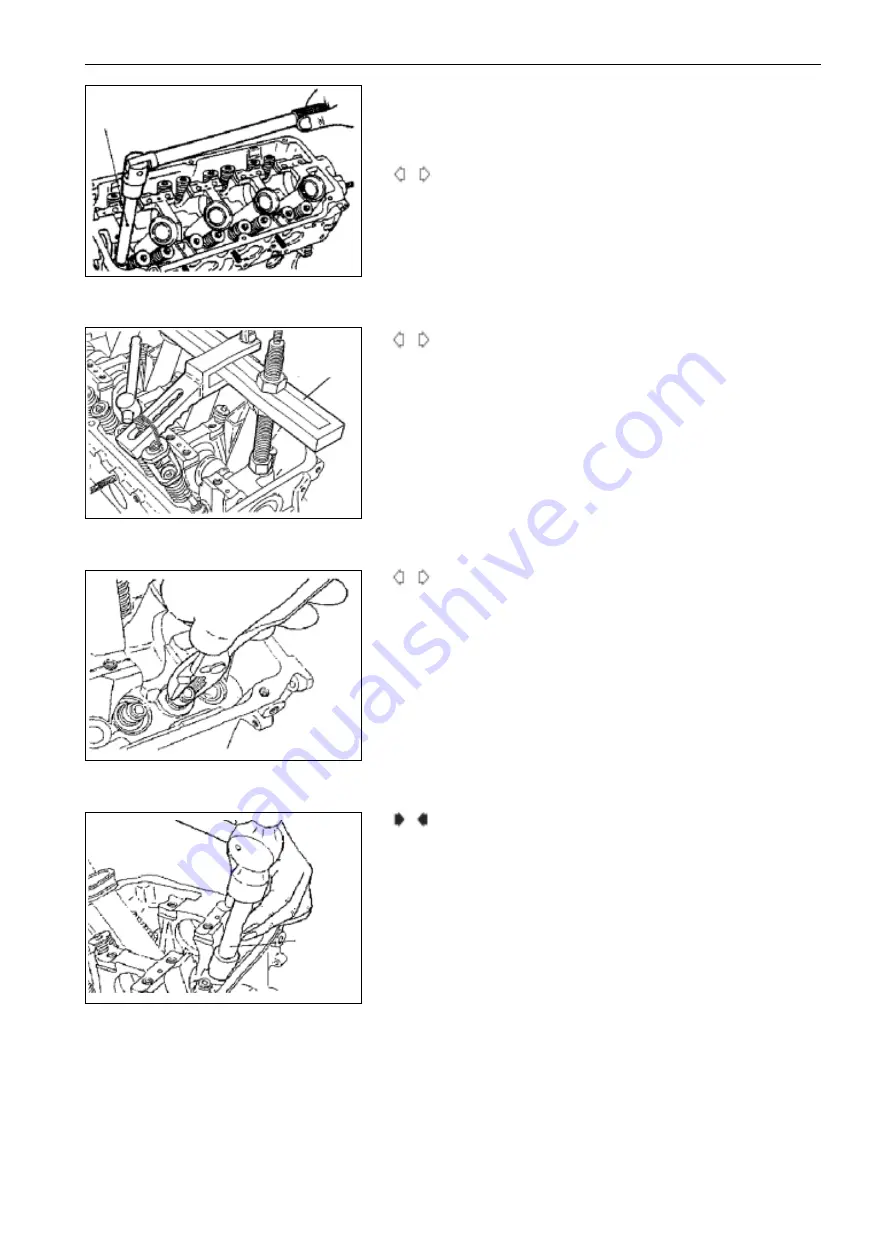
11-31
ENGINE
CYLINDER HEAD AND VALVE
MB991654
MD998772
9EN0062
9EN0063
MD998774
Notices after Disassembly
The disassembled parts should be sorted as per the cylinder number
and the intake/exhaust parts.
Dismantle of Cylinder head Bolts
(1)
Loosen the bolts of each cylinder heads with SST. The looseness
should be even and gradual.
Dism Dismantle of Valve Lock Clamp
(1)
The dismantled parts such as the valve and spring should be
marked with the cylinder number and signboard of mounting
position and kept well so as to prepare the later reuse in assembly.
Dismantle of Valve Oil Seal
(1)
The valve oil seal must not be reused.
Mount of Valve Oil Seal
(1)
Mount the lower site of valve spring.
(2)
Mount the valve oil on the valve guide with SST tools. Incorrect
mount will lead to leakage.
Notice:
The valve oil seal must not be reused.
A
A
C
B