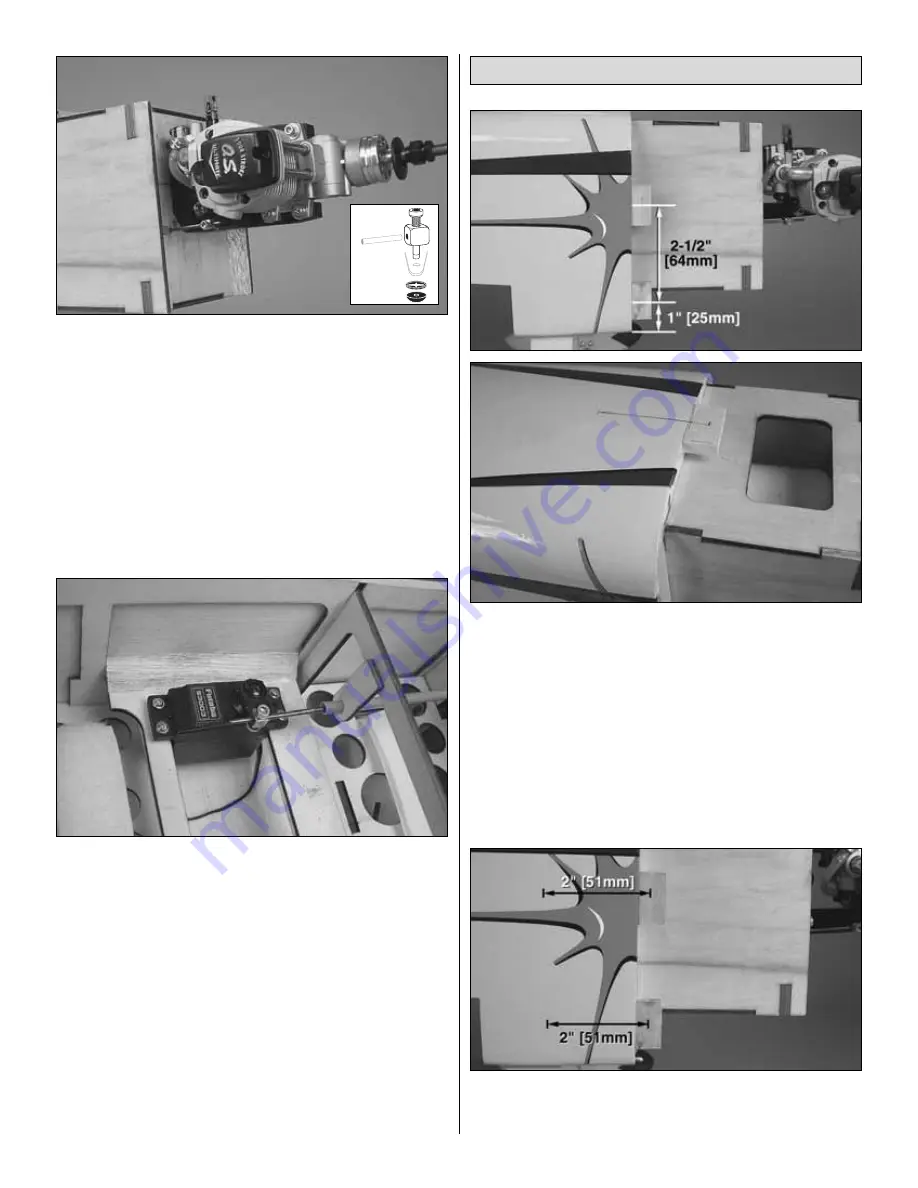
❏
12. Locate a .074 x 17.5” [445mm] pushrod wire. Cut the
threaded end from the wire. Insert the wire into the plastic tube
you installed for the throttle. Install a brass screw lock connector
into the throttle arm, locking it to the arm with a nylon retainer.
Insert this wire into the screw lock connector and the plastic
tube you installed for the throttle. Lock the wire to the connector
with a 6-32 x 1/4” [6mm] socket head cap screw.
Refer to this photograph for the steps 13-15.
❏
13. Locate the plywood pushrod support. Slide the support
over the gray plastic pushrod you have installed in the fuselage.
❏
14. Install the throttle servo into the tray in the fuselage.
Drill a 1/16” [1.6mm] hole through each of the mounting
holes in the servo. Install and then remove a servo mounting
screw into each of the holes you have drilled. Apply a couple
of drops of thin CA into the holes to harden the threads. After
the glue has cured, install your servo.
❏
15. Install a brass-screw lock connector and nylon retainer
to the servo arm. Slide it onto the pushrod wire, center the
servo, and install the servo arm onto the servo. Then, install
the servo screw into the servo and a 6-32 x 1/4” [6mm]
socket head cap screw into the screw-lock connector. Glue
the plywood pushrod support to the former.
❏
1. Measure up from the bottom of the fuselage 1" [25mm]
and make a mark. From that mark measure up 2-1/2" [64mm]
and make another mark. Epoxy a 1/4" x 1/2" x 1" [6x13x25mm]
hardwood block to the fuselage, centering the blocks on the
marks you have made. Do this on both sides of the fuselage.
Install a block at the top center of the fuselage.
❏
2. Install the cowl over the engine. Cut the cowl as needed
to fit the cowl to the fuselage. Final cutting of the cowl can be
done once the cowl is bolted to the fuselage. Once the cowl
will fit without any obstruction from any part of the engine,
remove the cowl from the fuselage.
❏
3. From the center of each of the cowl mounting blocks
measure back 2" [51mm]. Mark a line on the fuselage with a
fine-point felt-tip marker.
Install the Cowl
14