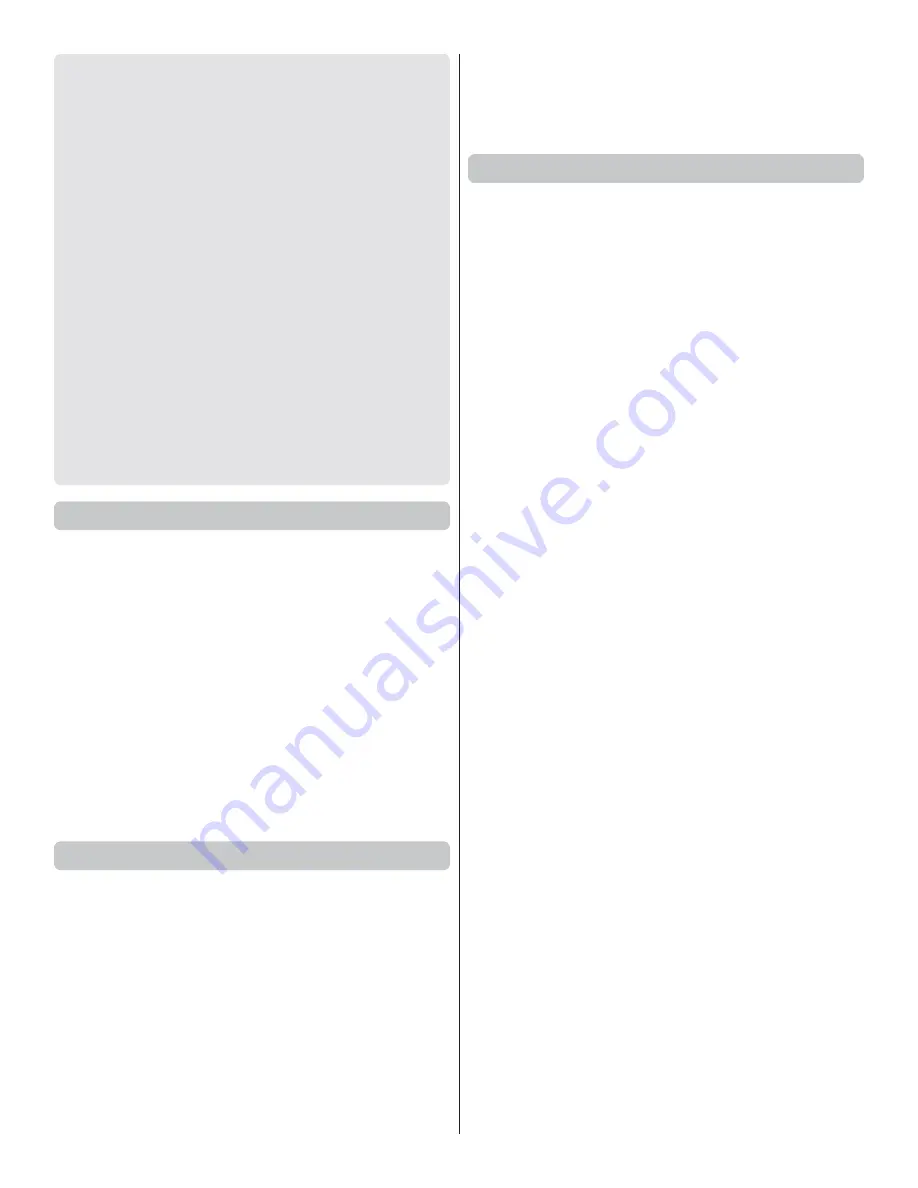
39
CAUTION
(This applies to all R/C airplanes)
If, while fl ying, you notice an alarming or unusual sound such
as a low-pitched “buzz,” this may indicate control surface
fl utter.
Flutter occurs when a control surface (such as an
aileron or elevator) or a fl ying surface (such as a wing or
stab) rapidly vibrates up and down (thus causing the noise).
In extreme cases, if not detected immediately, fl utter can
actually cause the control surface to detach or the fl ying
surface to fail, thus causing loss of control followed by an
impending crash. The best thing to do when fl utter is detected
is to slow the model
immediately
by reducing power, then
land as soon as safely possible. Identify which surface
fl uttered (so the problem may be resolved) by checking all
the servo grommets for deterioration or signs of vibration.
Make certain all pushrod linkages are secure and free of
play. If it fl uttered once, under similar circumstances it will
probably fl utter again unless the problem is fi xed. Some
things which can cause fl utter are; Excessive hinge gap;
Not mounting control horns solidly; Poor fi t of clevis pin in
horn; Side-play of wire pushrods caused by large bends;
Excessive free play in servo gears; Insecure servo mounting;
and one of the most prevalent causes of fl utter; Flying an
over-powered model at excessive speeds.
Takeoff
Before you get ready to takeoff, see how the model handles
on the ground by doing a few practice runs at
low speeds
on the runway. If you need to calm your nerves before the
maiden fl ight, shut the engine down and bring the model
back into the pits. Top off the fuel, then check all fasteners
and control linkages for peace of mind. If you have dual rates
on your transmitter, set the switches to “high rate” for takeoff,
especially when taking off in a crosswind. Although this model
has good low-speed characteristics, you should always build
up as much speed as your runway will permit before lifting off,
as this will give you a safety margin in case of a “fl ame-out.”
When you fi rst advance the throttle the plane will usually turn
left slightly. Correct by applying suffi cient right rudder to hold it
straight down the runway. When the plane has suffi cient fl ying
speed, lift off by smoothly applying up elevator (don’t “jerk” it
off into a steep climb!), and climb out gradually.
Flight
For reassurance and to keep an eye on other traffi c, it is a
good idea to have an assistant on the fl ight line with you. Tell
him to remind you to throttle back once the plane gets to a
comfortable altitude. While full throttle is usually desirable for
takeoff, most models fl y more smoothly at reduced speeds.
Take it easy with the Dirty Birdy for the fi rst few fl ights, gradually
getting acquainted with it as you gain confi dence. Adjust the
trims to maintain straight and level fl ight. After fl ying around
for a while and while still at a safe altitude with plenty of fuel,
practice slow fl ight and execute practice landing approaches
by reducing the throttle to see how the model handles at
slower speeds. Add power to see how the model climbs as
well. Continue to fl y around, executing various maneuvers
and making mental notes (or having your assistant write
them down) of what trim or C.G. changes may be required
to fi ne tune the model so it fl ies the way you like. Mind your
fuel level, but use this fi rst fl ight to become familiar with your
model before landing.
Landing
To initiate a landing approach, lower the throttle while on the
downwind leg. Allow the nose of the model to pitch downward
to gradually bleed off altitude. Continue to lose altitude, but
maintain airspeed by keeping the nose down as you turn onto
the crosswind leg. Make your fi nal turn toward the runway (into
the wind) keeping the nose down to maintain airspeed and
control. Level the attitude when the model reaches the runway
threshold, modulating the throttle as necessary to maintain
your glide path and airspeed. If you are going to overshoot,
smoothly advance the throttle (always ready on the right rudder
to counteract torque) and climb out to make another attempt.
When you’re ready to make your landing fl are and the model
is a foot or so off the deck, smoothly increase up elevator until
it gently touches down. Once the model is on the runway and
has lost fl ying speed, apply some down elevator to place the
nose on the ground, regaining nose wheel control. Remember
to mind your fuel level. Do not wait until your tank is empty to
begin your landing approach. You will need some fuel left if
you need to abandon your approach and circle back around.
One fi nal note about fl ying your model. Have a goal or fl ight
plan in mind for
every
fl ight. This can be learning a new
maneuver(s), improving a maneuver(s) you already know,
or learning how the model behaves in certain conditions
(such as on high or low rates). This is not necessarily to
improve your skills (
though it is never a bad idea!)
, but more
importantly so you do not surprise yourself by impulsively
attempting a maneuver and suddenly fi nding that you’ve run
out of time, altitude or airspeed. Every maneuver should be
deliberate, not impulsive. For example, if you’re going to do a
loop, check your altitude, mind the wind direction (anticipating
rudder corrections that will be required to maintain heading),
remember to throttle back at the top, and make certain you
are on the desired rates (high/low rates). A fl ight plan greatly
reduces the chances of crashing your model just because of
poor planning and impulsive moves.
If you are new to pattern fl ying, there are many great websites
on the internet that are dedicated to pattern fl ying. Other
resources for pattern fl ying information is web forums and of
course your local R/C fl ying club. Amateur videos of pattern
fl ying demonstrations which can be found on the internet are
also a great resource for learning.
Remember to think.
Have a ball! But always stay in control
and fl y in a safe manner.
GOOD LUCK AND GREAT FLYING!