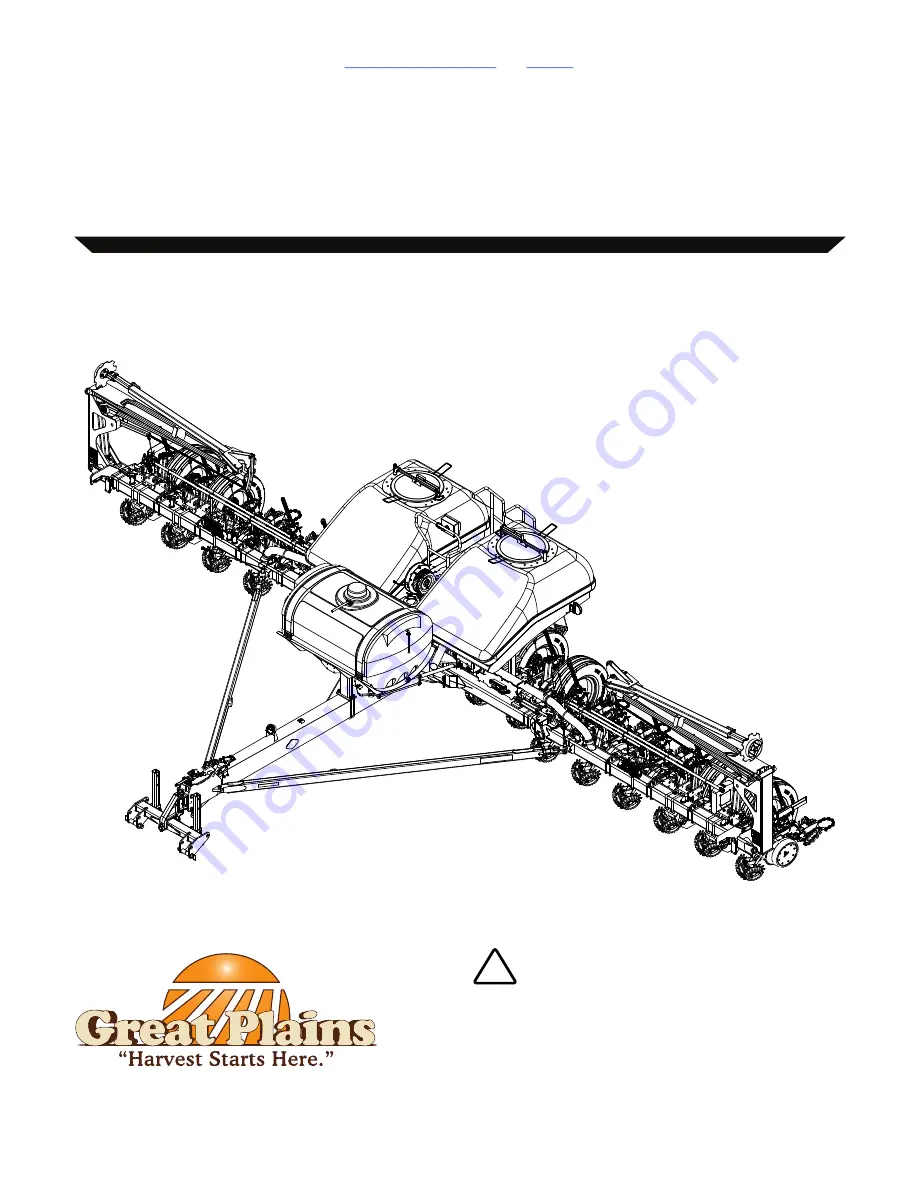
Read the operator manual entirely. When you see
this symbol, the subsequent instructions and
warnings are serious
-
follow without exception.
Your life and the lives of others depend on it!
Illustrations may show optional equipment not
supplied with standard unit.
!
Original Instructions
411-681M
Great Plains
OPERATOR MANUAL
MODEL PL5700 3-Section Planter
PLANTER
Summary of Contents for PL5700
Page 122: ...Great Plains 411 681M 04 08 2021 115 PL5700 Planter Table of Contents Index Specifications ...
Page 146: ...Great Plains 411 681M 04 08 2021 139 PL5700 Planter Table of Contents Index Warranty ...
Page 149: ......
Page 150: ...Great Plains Mfg 1525 E North St P O Box 5060 Salina KS 67402 ...