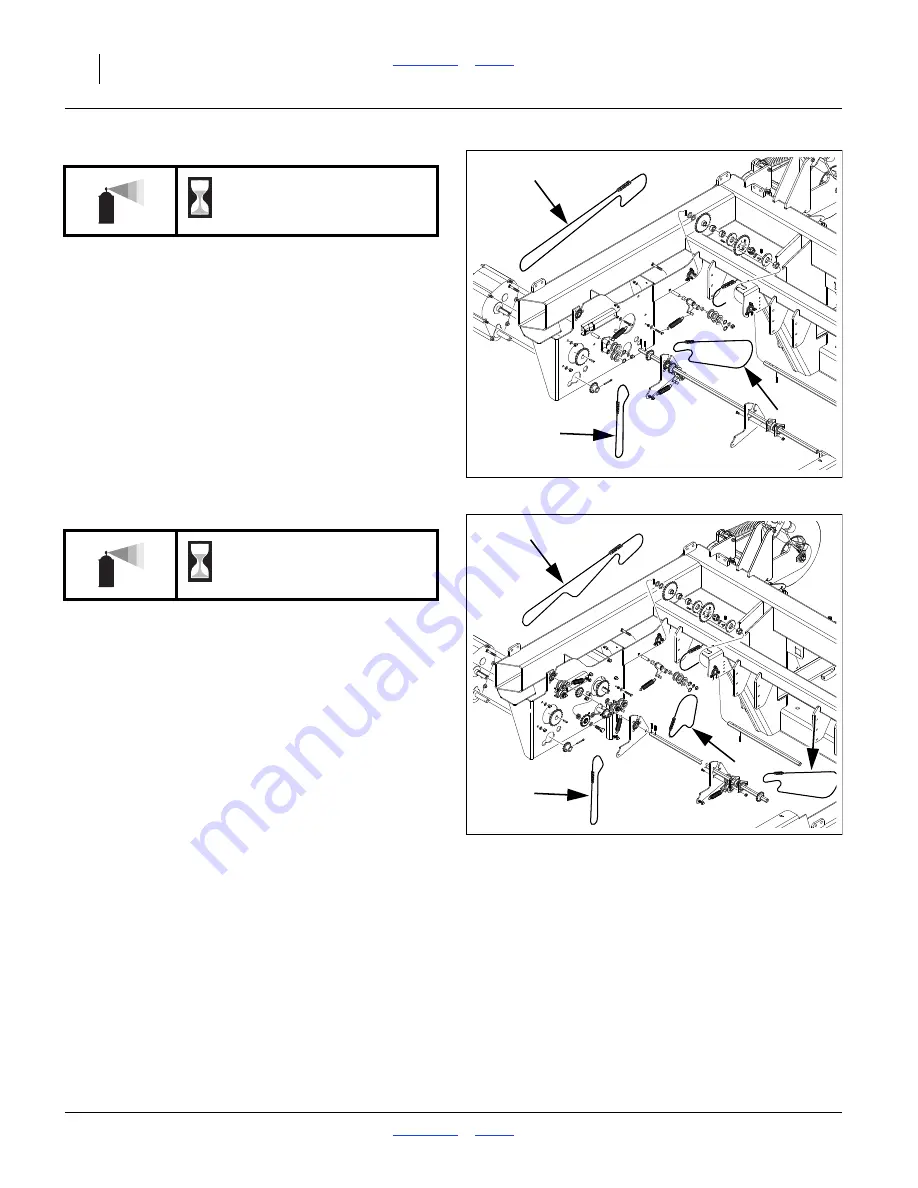
138
Great Plains Manufacturing, Inc.
NTA607/2007HD
166-283M
04/09/2019
Drive Chains (Single-Hopper)
1 gearbox input chain,
1 gearbox output chain,
1 meter input chain;
3 chains total (see also Contact Drive Chains)
Lubricant: multi-purpose spray lube
Quantity: coat thoroughly
Null4:
Drive Chains (Dual Hopper)
1 gearbox input chain,
1 gearbox-to-meter chain,
1 gearbox output chain,
1 meter input chain;
4 chains total (see also Contact Drive Chains)
Lubricant: multi-purpose spray lube
Quantity: coat thoroughly
Null4:
As Required
Null4:
31179
As Required
Null4:
31185