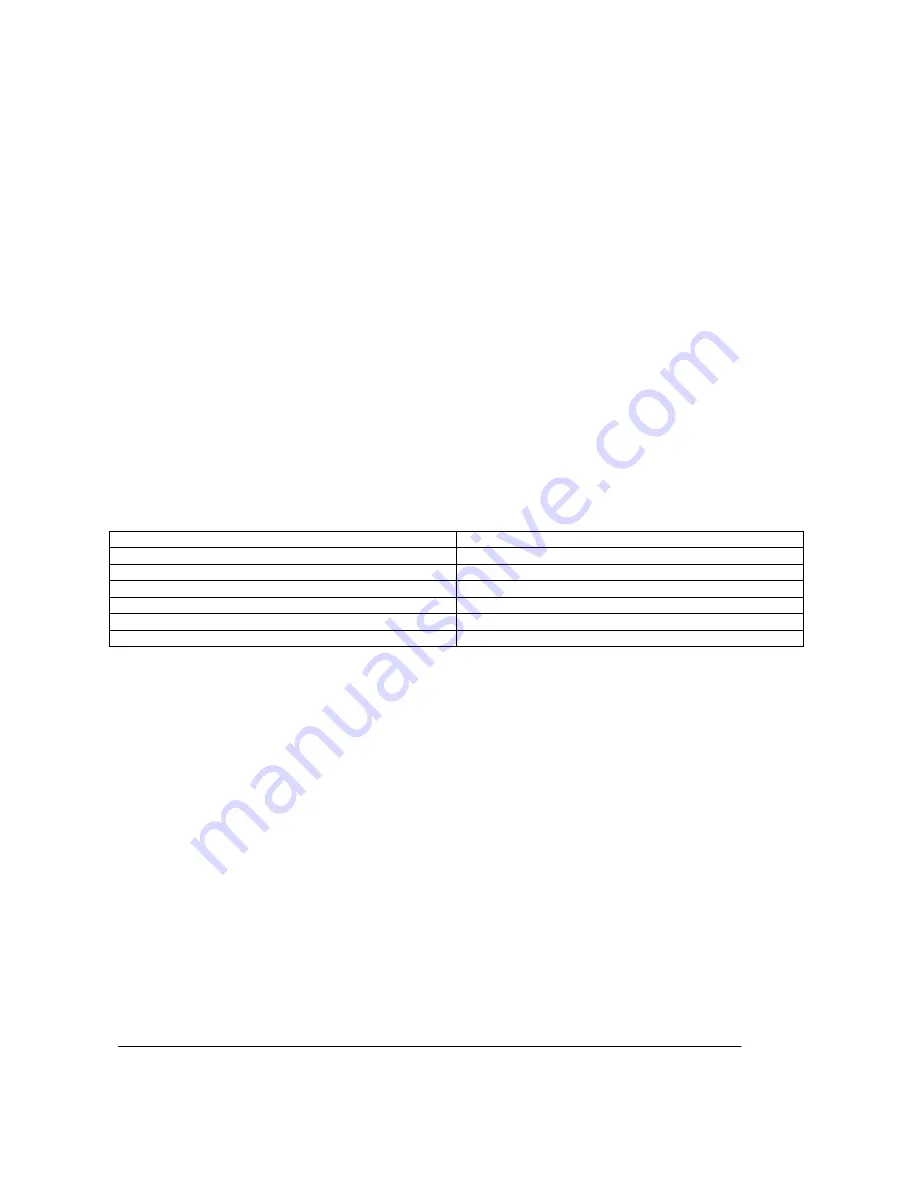
GRAUPNER GmbH & Co. KG D-73230 KIRCHHEIM/TECK GERMANY
Keine Haftung für Druckfehler. Technische Änderungen vorbehalten! Liability for printing errors excluded. We reserve the right to introduce modifications. Sous réserve de modifications!
Nous ne sommes pas responsables d’éventuelles erreurs d’impression!
#0058986
08/2008
19
ABS parts smooth and flat. We recommend 120-grit and 240-grit paper. 600-grit wet-and-dry paper is excel-
lent for obtaining a final smooth finish, and should also be used on surfaces which are to be painted.
•
Although the laser-cut ABS parts are extremely precise, minor gaps are inevitable at glued joints, and these
have to be made good. We recommend a non-cellulose modelling filler paste such as our Schnellspachtel
(Order No. 938) and SK 30 two-pack fast filler (Order No. 924). For younger model-makers we recommend
our Schnellspachtel (Order No. 938) because it is odourless, contains no solvents and is environmentally
friendly. Read the application notes printed on the packaging.
•
If you wish to fit out the model with auxiliary working systems other than the fire monitor, it is important to
plan their installation at an early stage - preferably before you start construction. You will find additional
notes and tips on additional functions at the end of these building instructions.
•
The electric motor must be suppressed before you install it. This is accomplished by soldering a 470 nF
capacitor (Order No. 3588) across the motor terminals as a bridge.
•
Deploy all electrical cables neatly, without crossing them over. Take great care to avoid any bare positive
wire touching any negative wire. Fix all cables in such a way that they cannot possibly come into contact
with the rotating parts of the power train; cable-ties are good for this.
•
Be sure to use cable which is capable of carrying the currents which flow when the boat is operating. If you
install the recommended system components, the appropriate size is 2.5 mm² conductor cross-section (e.g.
Order No. 3689).
•
Deploy the receiver aerial as far away as possible from any high-current cables (at least 3 cm).
•
The shaft system must be lubricated; be sure to use a type of grease or oil which does not soil or contami-
nate water (e.g. grease: Order No. 570; oil: Order No. 206).
•
Before gluing parts together, it is important to clean the joint surfaces carefully. This is best accomplished
by sanding lightly, followed by wiping with a non-greasy liquid detergent or methylated spirit (“meths”). The
same applies to all surfaces which are to be painted, as this improves the paint’s adhesion considerably.
•
Recommended adhesives for joining particular materials:
Material - material
Suitable adhesives
Plastic motor mount - wood
Cyano-acrylate (“cyano”)
ABS - wood
Cyano-acrylate, UHU acrylit
ABS - ABS
Cyano-acrylate, UHU acrylit, UHU plast spezial
ABS - metal
Cyano-acrylate, UHU acrylit
Wood - wood
Cyano-acrylate, UHU hart, white glue
Wood - metal
Cyano-acrylate
Read the instructions supplied with the adhesives. Be sure to observe any special notes in the instructions regarding particular
adhesives. If you are using acetone, methylated spirits or any other solvent as a cleaning agent, special safety measures must be
taken: read the instructions supplied with these materials.
Assembly instructions
1.
The first step is to assemble the boatstand (parts 1, 2 and 3).
TIP
: it is a good idea to stick felt or foam
rubber to the contact surfaces, as this will avoid scratching the hull. The surfaces are particularly vulner-
able when they have been painted.
2.
Assemble the rudder system reinforcement (parts 4, 5 and 6), then glue the rudder bush (part 7) in it.
IM-
PORTANT
: the bush should project by about 12 mm at the top, as shown on the plan. Glue the completed
assembly in the hull (part 8).
NOTE
: the small projecting area between the keel and the hull can be re-
moved if you wish. If you decide to do this, first fill the small channel on the inside of the hull with glue and
allow it to set hard before cutting off the excess material with a modelling knife; alternatively you can sand
it back flush with the hull. Take care not to sand right through the skin!
3.
Glue the motor mount (part 9) in the mounting plate (part 10).
TIP
: lay both parts on a sheet of plastic and
glue them together, to ensure that the motor mount lies exactly flush with the mounting plate (cyano will
not stick to the plastic film).
4.
Fit the two M2 screws (parts 11) and the M2 nuts (parts 12) in the motor mount; at a later stage they hold
the stern tube (part 13) in position.
5.
Solder the suppressor capacitor (part 15), the high-flex copper cable (part 16) and the G2 connectors
(parts 17) to the terminals of the motor (part 14).
6.
Fit the four grubscrews (parts 19) in the shaft coupling (part 18), then insert the motor shaft in the coupling
and tighten the retaining screws.
7.
Place the motor on the motor mount and secure it using the motor retaining screws (parts 20).
8.
Place this assembly in the hull, screw the propeller (part 21) on the end of the shaft, position the parts