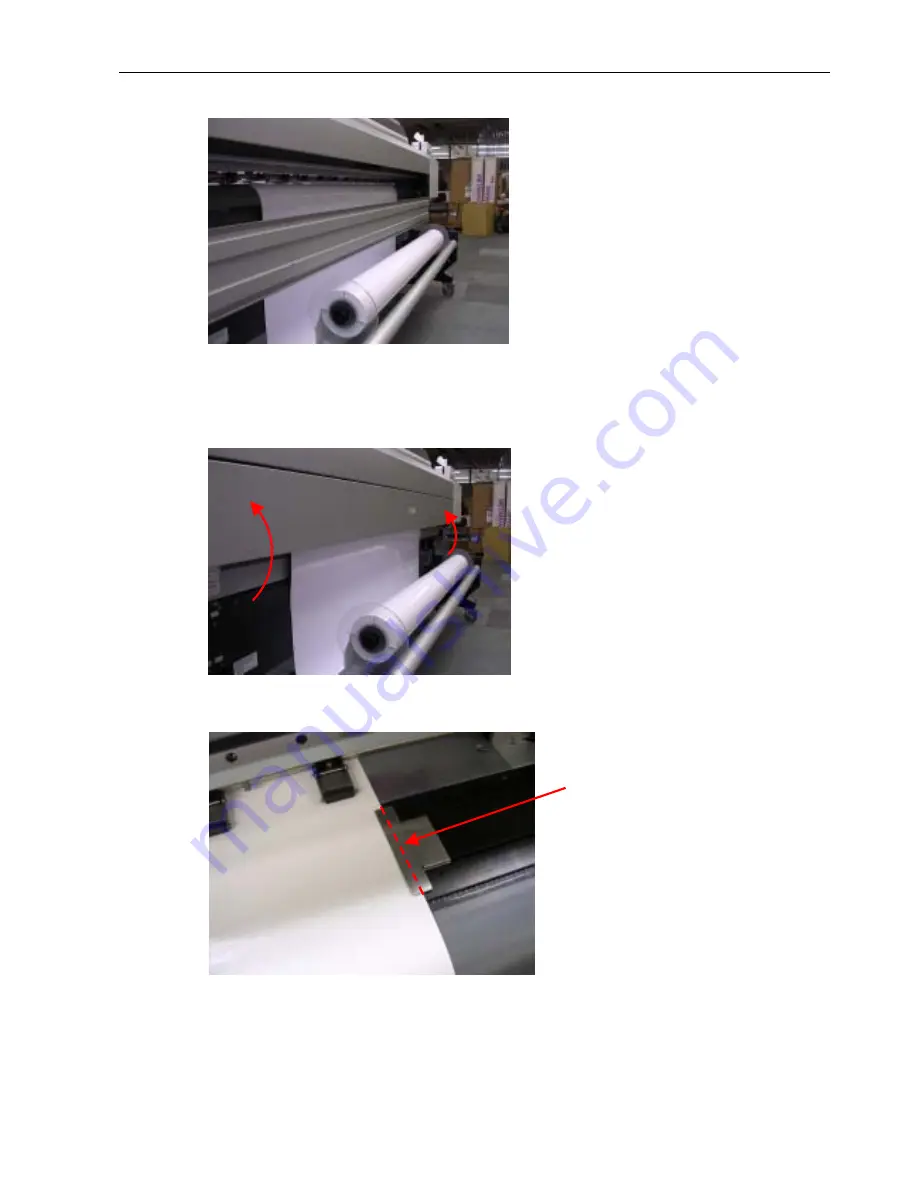
SignJet JS310 Series Set Up Guide
(3) Insert the leading edge of the media from the rear of the printer towards the front.
(4) Align the left edge of the media with the rear guide and front guide scales at the left of the printer,
making sure that the media is not loaded at an angle.
(5) Lower the press roller control pole to hold the media in place.
(6) Close the flap and Replace the screws to the flap at the rear of the printer.
(7) Align the media edge guards with the left and right edges of the media.
Slide each media edge guard
to approximately the position
indicated by the dotted line.
- 47 -