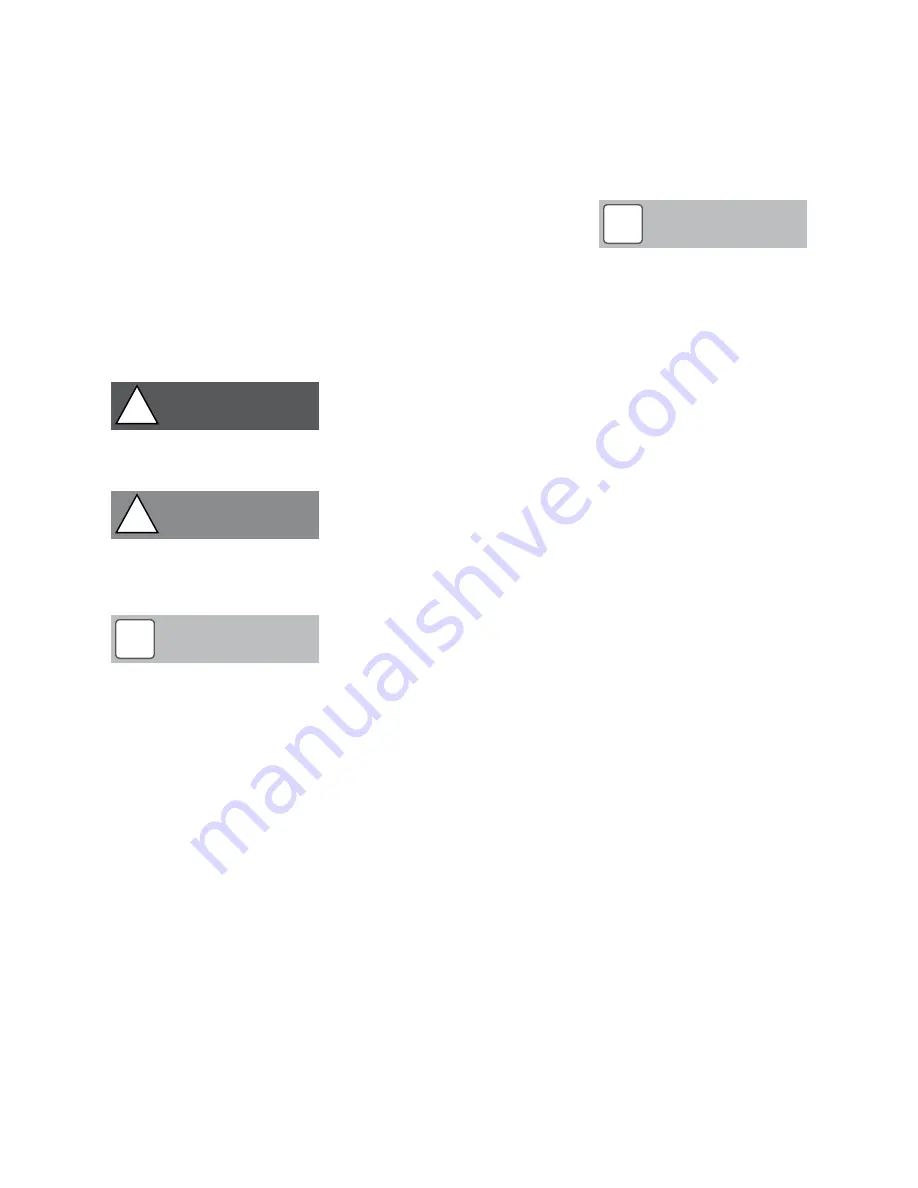
1
Introduction
4
Warning of possible human injury as
a consequence of not following the
instructions in the warning.
The Grant VORTEX Pro Combi e
condensing boilers contain an extra
heat exchanger which is designed to
recover the latent heat normally lost
by a conventional boiler. It does this
by cooling the flue gases to below 90°
C, thus extracting more sensible heat
and some of the latent heat. This is
achieved by cooling the flue gases to
their dew point (approximately 55° C).
To ensure maximum efficiency, the
boiler return temperature should be 55°
C or less, this will enable the latent heat
to be condensed out of the flue gases.
The boiler will achieve net thermal
efficiencies of 100%.
To achieve maximum performance
from the Grant VORTEX Pro Combi
e boilers, it is recommended that
the heating system is designed so
that a temperature differential of
20°C between the flow and return is
maintained.
The Grant Vortex Pro Combi e boilers
will however still operate at extremely
high efficiencies even when it is not
in condensing mode and therefore
is suitable for fitting to an existing
heating system without alteration to the
radiator sizes. The boiler is capable of a
maximum flow temperature of 78° C.
1.2 Boiler description
The Vortex Pro Combi e boilers are
automatic pressure jet oil boilers
designed for use with a sealed central
heating system and will provide
domestic hot water at mains pressure.
All boilers are supplied with the control
panel and the burner factory fitted, and
a factory fitted low level discharge fuel
system.
Caution concerning likely damage
to equipment or tools as a
consequence of not following the
instructions in the caution.
Note text. Used for emphasis or
information not directly concerned
with the surrounding text but of
importance to the reader.
1.1 How a Condensing
Boiler Works
During the combustion process,
hydrogen and oxygen combine to
produce heat and water vapour. The
water vapour produced is in the form
of superheated steam in the heat
exchanger. This superheated steam
contains sensible heat (available heat)
and latent heat (heat locked up in the
flue gas). A conventional boiler cannot
recover any of the latent heat and
this energy is lost to the atmosphere
through the flue.
!
WarninG
!
CaUtiOn
!
nOtE
For conventional flue applications,
where required, Grant recommends
the use of the Grant ‘Green’ flue
system, to provide an insulated twin
- wall flue system. Refer to Section 9
for further details.
Only Kerosene must be used with a
low level discharge flue appliance.
The Vortex Pro Combi e boilers are
only suitable for use with Kerosene.
All burners are ready to connect to a
single pipe system with a loose flexible
fuel line (900mm) and
3
/
8
” to
1
/
4
” BSP
male adaptor supplied with the boiler.
If required, an additional flexible fuel
line (900mm) and
3
/
8
” to
1
/
4
” BSP male
adaptor are available to purchase from
Grant Engineering (UK) Limited, for
two-pipe oil supply system, Part No.
RBS36.
The temperature of the water leaving
the boiler to heat the radiators is User
adjustable.
The setting of the boiler thermostat on
the Vortex Pro Combi e boilers has no
effect on the hot water performance.
Figure 1-1 shows the components in
the Vortex Pro Combi e boilers and the
position of the control panel. Figure 1-2
shows the details of the control panel.
!
nOtE
This manual is intended to guide
engineers in the installation and
maintenance of Grant VORTEX Pro
External Combi e boilers. A separate
manual is available to guide users in
the operation of these boilers, and
is printed inverted at the end of this
manual.
The following special text formats
are used in this manual for the
purposes listed below: