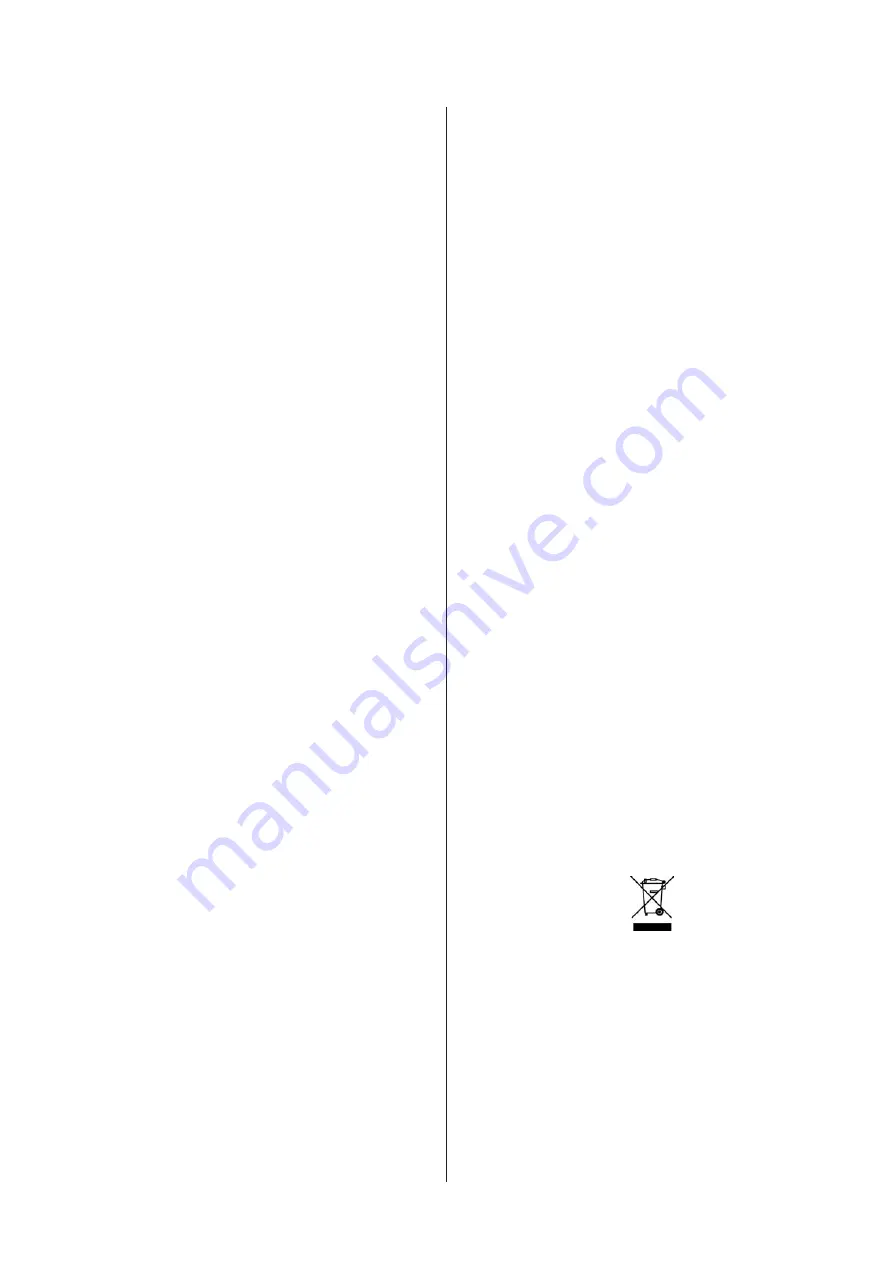
14
8.2.2 SAFETY DEVICES
- Door closed safety microswitch cuts off power to the whole
auxiliary circuit and consequently stops the machine.
- Electronic overcurrent device (overload cutout) within the motor:
disconnects power supply in the event of coil overheating.
- Air-break system in the soap dispenser: prevents wastewater from
polluting the drinkable water system in the event of a depression.
- Normally open drain valve: enables safe door manual opening by
means of the manual puller.
- Tilt switch: avoids mechanical damage in the event of irregular
loads.
- Fuse-fitted heating elements. the electric circuit is disconnected in
case of malfunction.
8.3 PERIODIC MAINTENANCE BY TECHNICAL
PERSONNEL
All periodic maintenance operations must be carried out by the
authorized after-sales service or by qualified personnel.
BEFORE ANY MAINTENANCE OPERATION, CHECK THAT
THE WALL CIRCUIT BREAKER IS OFF AND THE WARM
WATER, COLD WATER AND STEAM TAPS ARE CLOSED
(THE LATTER APPLIES TO STEAM-HEATED MACHINES
ONLY). THE DRUM MUST BE MOTIONLESS AND DRAINED
AND THE INSIDE TEMPERATURE MUST NOT EXCEED
40°C.
Be very careful during maintenance. NEVER override or ignore
safety devices for any reason. Use only original spare parts. If doubts
should arise, contact your sales person immediately, explaining
what the fault is and indicating some information on the machine:
model and serial number (details reported on the rating plate
appearing on the rear of the machine or inside the door, where
applicable).
Monthly checks
Make certain that the filters located on the outer part of the electrical
valves are clean.
Make certain that the steam valve strain is clean (this applies to
steam-heated machines only).
Clean the soap dispenser from any soap remains.
Clean the door gasket and the tub inlet with a cloth. Always keep
forced-cooling slots and openings free from dust (the fan sucks
fresh air from the room), which are on the rear of the machine,
where the speed inverter is housed.
Yearly checks
Make certain that the floor fastening nuts are securely closed (if
applicable).
Check the wear of the belts and replace them if necessary. If more
than one of them is worn out, replace the entire set of belts.
Make sure that the safety devices are working properly (e.g. the lock
microswitch and the tilt microswitch).
Check that the screws for electrical connection are tight on the
contactors and power inlet terminal strip.
Disassemble the drain valve and clean it inside from lint.
Check that the heating elements are in perfect condition and clean
them from scale.
BEFORE TURNING THE MACHINE BACK ON BY THE
CIRCUIT BREAKER, PUT ALL THE PANELS REMOVED
BACK IN PLACE.
8.4 AUTOMATIC MAINTENANCE REQUEST
The machine saves the number of cycles it executes. After 1000
programs the machine will flash a message from cycle 1001
onwards.
More precisely, when starting a new cycle by the START/STOP
button, the machine will enable the buzzer and will flash the writing
" MAINTENANCE REQUIRED" for 10 seconds. Then it will carry
out the selected cycle normally. At every cycle, 50 cycles before
cycle 1000, the display puts out the message "MAINTENANCE IN
50 cycles" to warn the user that maintenance will be required. In this
case the buzzer will not be enabled.
When this message is displayed, request yearly maintenance.
To dismiss this reading and start the 1000 cycle count from scratch,
press the push-button "- " for at least 5 secs with the door closed.
Then the total number of cycles performed will be viewed and, if the
push button "-" is pressed again within 10 seconds, the count will
be set to zero and will be ready to start back again.
Before resetting the G400 control it will be necessary to enter a date
and a text. The control will first read the question "date: 01/01/01".
Move the cursor to the first "0". Increase or decrease the selection
as needed using keys "+" and "-" and confirm using the "
!
:
ENTER" key. Then the cursor will automatically move to the
second figure of the date ("1"). Proceed accordingly until the date
is complete and then press the "
!
: ENTER" key. The G400 control
will prompt the word "technician": enter the name of the person
who performed the maintenance.
Press the "SEL" key: the cursor will become bigger so that you can
select the letters using keys "+" and "-". Confirm by the "
!
:
ENTER" key. The cursor will move to the next position so that you
can select the next letter as above. The control count cannot be reset
unless these two values are entered.
This information will be stored and is available in the SERVICE
menu, MAINTENANCE entry, along with the number of cycles
performed from the last maintenance event and the total number of
cycles carried out.
8.5 IDENTIFYING AND ORDERING SPARE PARTS
To identify the codes of spare parts refer to the exploded drawings
and relevant list. Once you have identified your codes, send a
standard written order to the manufacturer, mentioning clearly
machine model, serial number, feed voltage and frequency and, of
course, including the code and description of the spare part needed.
9. MACHINE DECOMISSIONING,
DISMANTLING AND DISPOSAL
If the equipment is no longer to be used, it is advisable to
decommission it and suitably dispose of the resulting materials,
considering the advice provided in the chapter "Transportation and
installation". Please, for the sake of the environment, sort the
materials in accordance with the waste disposal provisions in force
in your country, so that they can be properly disposed of or recycled.
All the parts composing the machine can be treated as solid urban
waste, except for the metal parts, which yet are not classed among
special waste in most European countries.
9.1 INFORMATION TO USERS
Pursuant to the Italian law 151 that implements Directives 2002/
95/EC, 2002/96/EC and 2003/108/EC concerning the reduction in
the use of hazardous substances in electric and electronic apparatus,
as well as waste disposal
the crossed-out dustbin symbol on the appliance indicates the
product must be disposed of separate from other wastes once it
reaches the end of its life cycle.
The sorting for recycling purposes of this equipment when at the
end of its life cycle is organized and managed by the manufacturer.
Users willing to discard this equipment will have to contact the
manufacturer and comply with the procedures the latter has
established for sorting and recycling the machine at the end of its
life cycle. Adequate pre-sorted waste collection before subsequently
sending the appliance for recycling, treatment and environmentally
compatible disposal helps avoid possible negative effects on the
environment and health and favors the recycling of the materials
making up the appliance. Unlawful disposal of the product by the
user is punishable by the administrative sanctions the laws in force
provide for.
www.groupdynamics-laundry.com