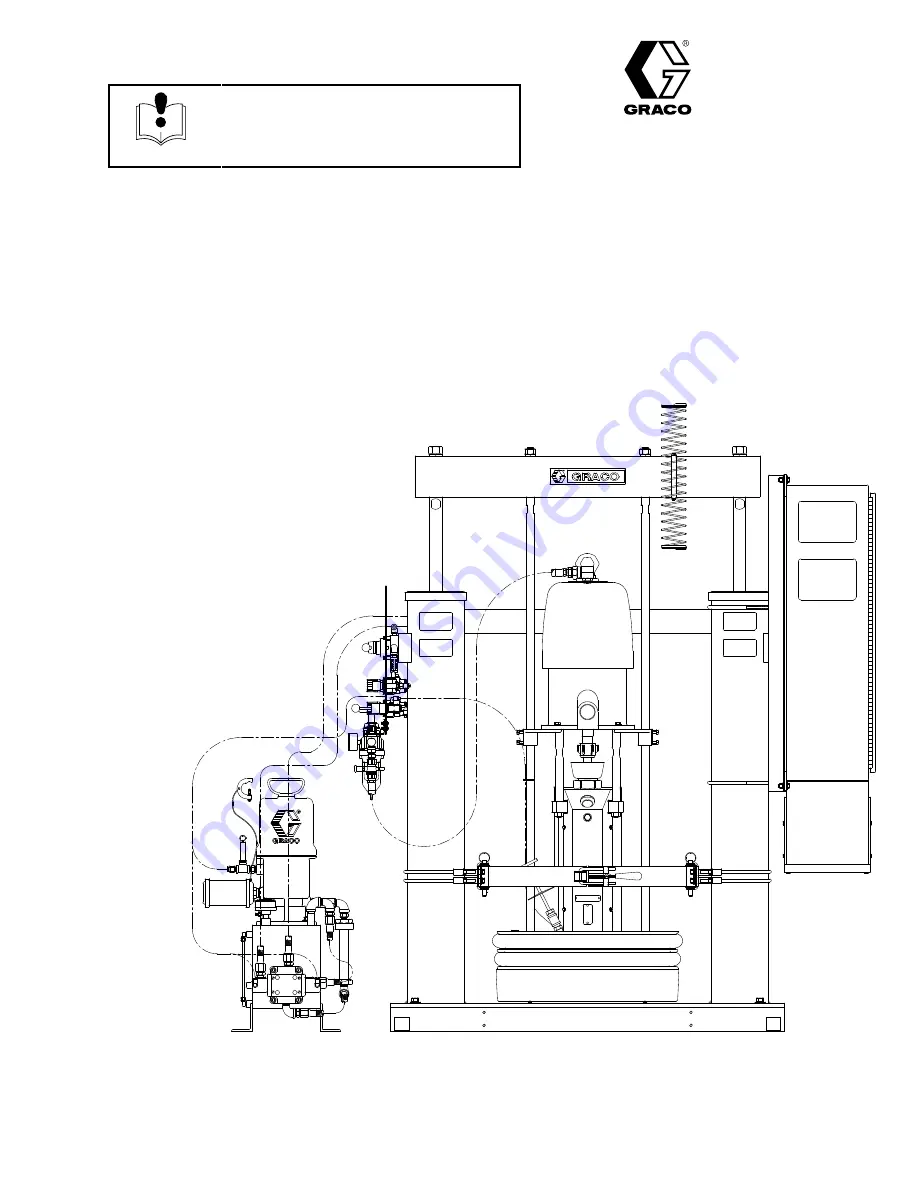
310–534
Rev. B
Supersedes Rev. A
INSTRUCTIONS–PARTS LIST
INSTRUCTIONS
This manual contains important
warnings and information.
READ AND KEEP FOR REFERENCE.
200 Liter (55 Gallon) Drum Size
165 mm (6.5”) Dual Post
Therm-O-Flow
55-H
Heated Supply Unit
with Hydraulic-Powered Ram
918–452
Silicone Follower Wipers,
31:1 Bulldog
, 480 VAC,
Therm-O-Flow Pump Module,
Hydraulic Power Supply
918–453
Silicone Follower Wipers,
65:1 King
, 480 VAC,
Therm-O-Flow Pump Module,
Hydraulic Power Supply
918–480
Silicone Follower Wipers,
31:1 Bulldog, 240 VAC,
Therm-O-Flow Pump Module,
Hydraulic Power Supply
Summary of Contents for Therm-O-Flow 55-H
Page 42: ...42 310 534 Notes ...
Page 60: ... 310 534 Electrical Control Panel and Wiring for C32428 240 VAC Lines 100 121 122 122 ...
Page 64: ...64 310 534 Electrical Control Panel and Wiring for C32428 240 VAC Lines 200 220 ...
Page 65: ...310 534 65 Notes ...
Page 66: ... 310 534 Electrical Control Panel and Wiring for C32429 480 VAC 122 122 Lines 100 121 ...
Page 70: ...70 310 534 Electrical Control Panel and Wiring for C32429 480 VAC Lines 200 220 ...