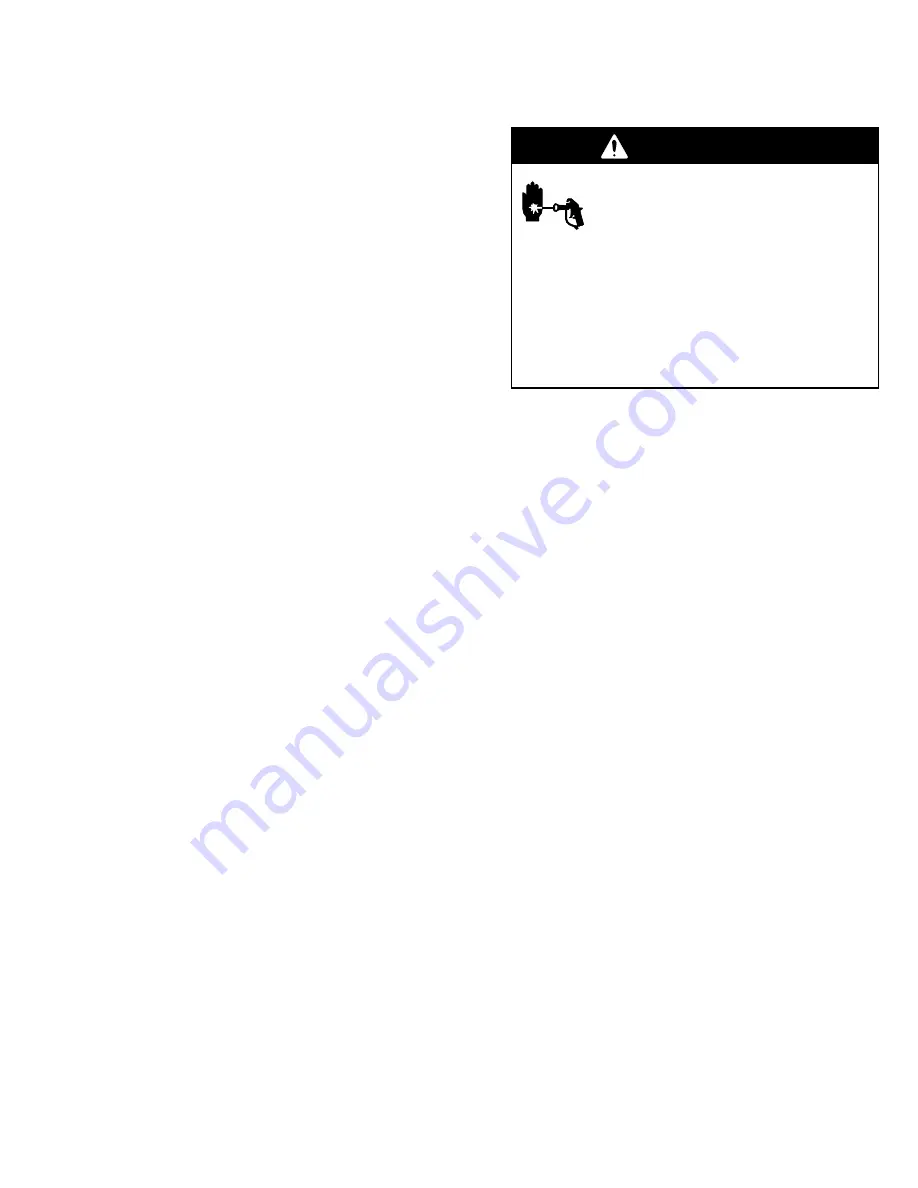
5
306–667
Operation
Grounding
To reduce the risk of static sparking, ground the pump,
object being sprayed, and all other spray equipment
used or located in the spray area. Check your local
electrical code for detailed grounding instructions for
your area and type of equipment. Be sure to ground all
of this spray equipment.
Pump or sprayer: as instructed in your separate
pump or sprayer manual.
Air compressor or hydraulic power supply: accord-
ing to local code.
Fluid hoses: use only grounded hoses with a maxi-
mum of 500 feet (150 m) combined hose length to
ensure grounding continuity.
Spray gun: obtain grounding through connection to
a properly grounded fluid hose and sprayer or
pump.
Fluid supply container: according to local code.
Object being sprayed: according to local code.
All solvent pails used when flushing, according to
local code. Use only metal pails, which are conduc-
tive. Do not place the pail on a non-conductive
surface, such as paper or cardboard, which inter-
rupts the grounding continuity.
To maintain grounding continuity when flushing or
relieving pressure, always hold a metal part of the
gun firmly to the side of a metal pail, then trigger
the gun.
Pressure Relief Procedure
WARNING
INJECTION HAZARD
Fluid under high pressure can be in-
jected through the skin and cause
serious injury. To reduce the risk of an
injury from injection, splashing fluid, or moving
parts, follow the Pressure Relief Procedure
whenever you:
are instructed to relieve the pressure,
stop spraying,
check or service any of the system equipment,
or install or clean the spray tips.
1.
Engage the spray gun safety latch.
2.
Shut off the power supply to the pump and close
any bleed-type master air valves in the air supply.
3.
Disengage the gun safety latch.
4.
Hold a metal part of the gun firmly to the side of a
grounded metal pail, and trigger the gun into the
pail to relieve pressure.
5.
Engage the spray gun safety latch.
6.
Open the pump fluid drain valve (required in your
system), having a container ready to catch the
drainage.
7.
Leave the drain valve open until you are ready to
spray again.
If you suspect that the spray tip or hose is completely
clogged, or that pressure has not been fully relieved
after following the steps above, very slowly loosen the
tip guard retaining nut or hose end coupling and relieve
pressure gradually, then loosen completely. Now clear
the tip or hose.