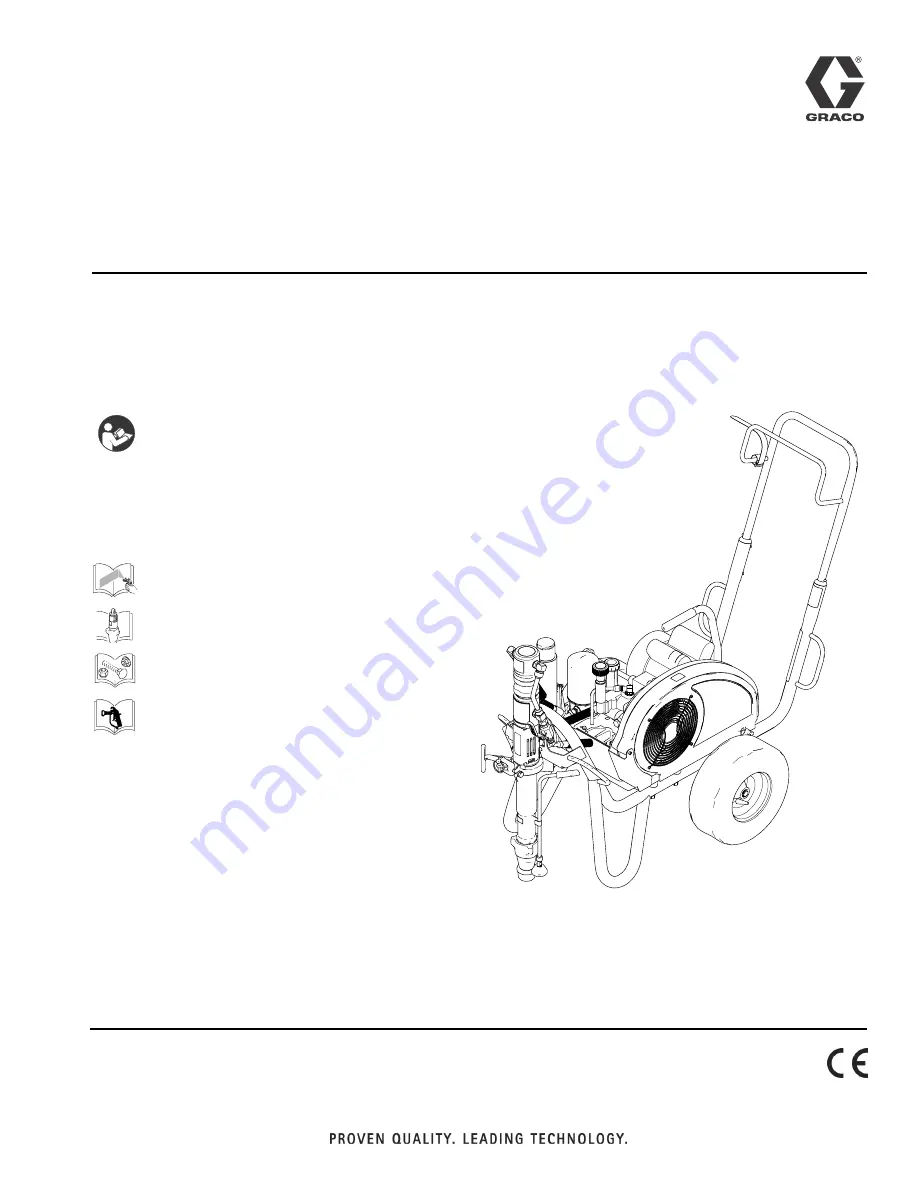
Repair
DutyMax
™
Hydraulic Sprayers
3A2247A
EN
-
For professional use only -
- Not approved for use in European explosive atmosphere locations -
Models: 24M054 (EH200DI), 24M055 (GH200DI), 24M056 (EH300DI), 24M057 (GH300DI)
3300 psi (22.8 MPa, 228 bar) Maximum Working Pressure
See page 3 for model information.
Important Safety Instructions
Read all warnings and instructions in this
manual. Save these instructions.
3A2246
311845
3A2248
308491 - Blue Texture Gun
309495 - Inline Texture Gun
ti18188a