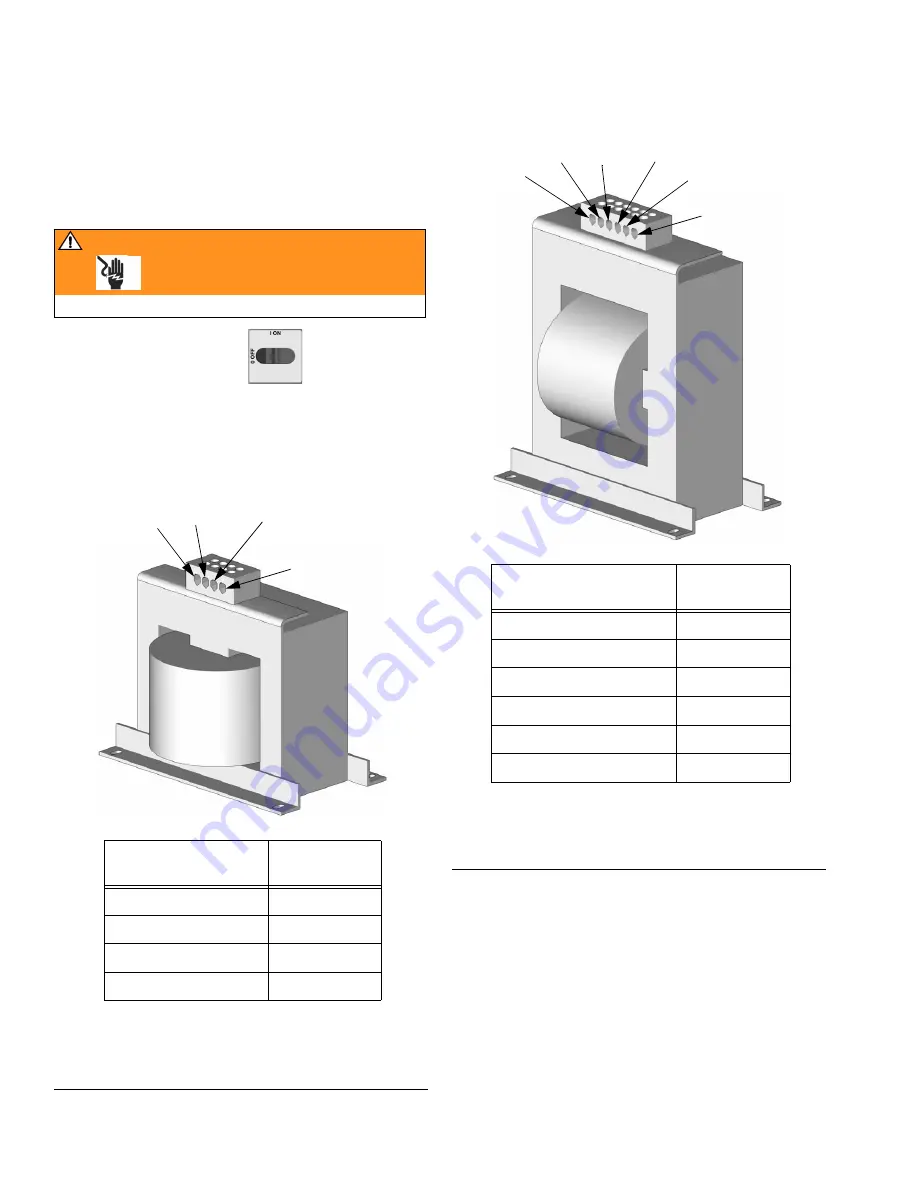
Setup
22
309551C
Turn main power switch OFF
. Transformer tap
wire connections vary depending on length of heated
hose. See F
. 8. Verify that tap wire connec-
tions are correct.
11.
Set transformer wire
taps
WARNING
Read warnings, page 5.
F
IG
. 7: Model E-20 and E-XP1 Transformer Wire Taps
.
* Length includes heated fluid hose and whip hose.
Hose Length* ft (m)
Tap Terminal
Label (ft)
60-85 (18.3-25.9)
50
110-135 (33.5-41.2)
100
160-185 (48.8-56.4)
150
210-235 (64.1-71.7)
200
TI3469a
50 ft
100 ft
150 ft
200 ft
F
IG
. 8: Model E-30 and E-XP2 Transformer Wire Taps
* Length includes heated fluid hose and whip hose.
Hose Length* ft (m)
Tap Terminal
Label (ft)
60-85 (18.3-25.9)
50
110-135 (33.5-41.2)
100
160-185 (48.8-56.4)
150
210-235 (64.1-71.7)
200
260-285 (79.3-86.9)
250
310 (94.6)
300
TI3470a
50 ft
100 ft
150 ft
200 ft
250 ft
300 ft