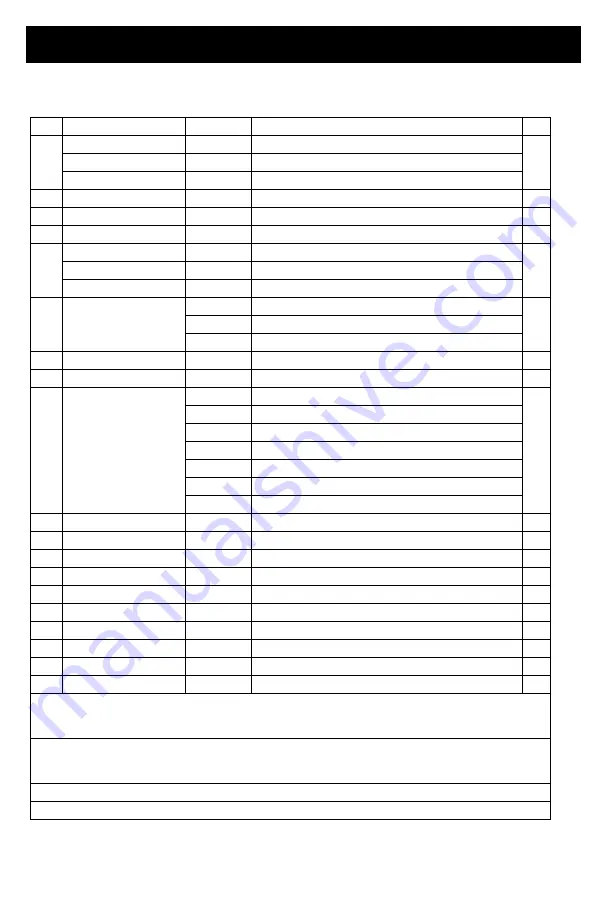
Parts - SaniSpray HP 65 (Quick Repair)
3A7653D
31
Parts List - SaniSpray HP 65 (Quick Repair)
Ref. Sprayer Model
Part
Description
Qty.
1
25R972, 25R962 25R921
KIT, motor, drive, HP65, 120V,
includes 56
1
25R946
25T291
KIT, motor, drive, 230V, CEE,
includes 56
25R948, 25R954 25T292
KIT, motor, drive, 230V, multi,
includes 56
7
All
25R920
KIT, pump
1
8
All
25R922
KIT, enclosure
1
26
All
25R923
KIT, hopper
1
31†
25R792
25R874
GUN, SaniSpray, HP, NA
1
25R946, 25R948 25T289
GUN, SaniSpray, HP, EU
25R954, 25R962 25T290
GUN, SaniSpray, HP, AP
32
All
LP617
TIP, LP617
1
LP619 †
TIP, LP619
LP621
TIP, LP621
36
All
112133
SCREEN, hopper
1
56
All
25T410
KIT, warning labels, cord
1
60
All
CARD, medical alert (not shown)
1
222385
English, Spanish, French
17F690
Dutch, German, Italian
17A134
English, Chinese, Korean
17R476
English, Spanish, Portuguese (Brazil)
26A997
English, Indonesian, Hindi
26A998
English, Chinese, Japanese
98
All
25T282
EXTENSION, 15 in. (not shown)
1
99*
All
25R872
TIPSEAL, 5-pack (not shown)
1
101
All
25C828
HOSE, 1/8 in. x 4-1/2 ft.
1
118
25R948, 25R954 195551
PLUG, retaining
1
144
25R962
244285
CORDSET, Japan (not shown)
1
146
25R954
17N232
CORDSET, India (not shown)
1
147
25R948, 25R954 242001
CORDSET, EU Schuko
1
149
25R954
242005
CORDSET, ANZ
1
157
25R948
287121
CORDSET, Italy, Denmark, Switzerland
1
158
25R948
17J242
CORDSET, UK (not shown)
1
Motor/Drive Kit 25R921 does not include cordset adapter for Japan. Cordset adapter
must be ordered separate (see Ref. 144). Control Kit 25T292 does not include cordset
adapter. Cordset adapter must be ordered separate (see Ref. 146-158).
*
Two extra TipSeals (polymer spray tip seals) are included with the sprayer. For
disinfectant applications, use TipSeal (polymer spray tip seal) instead of the OneSeal
(metal seal) that is included with the replacement spray tips.
†
SaniSpray HP Gun includes LP619 Spray Tip.
Replacement safety labels, tags, and cards are available at no cost.