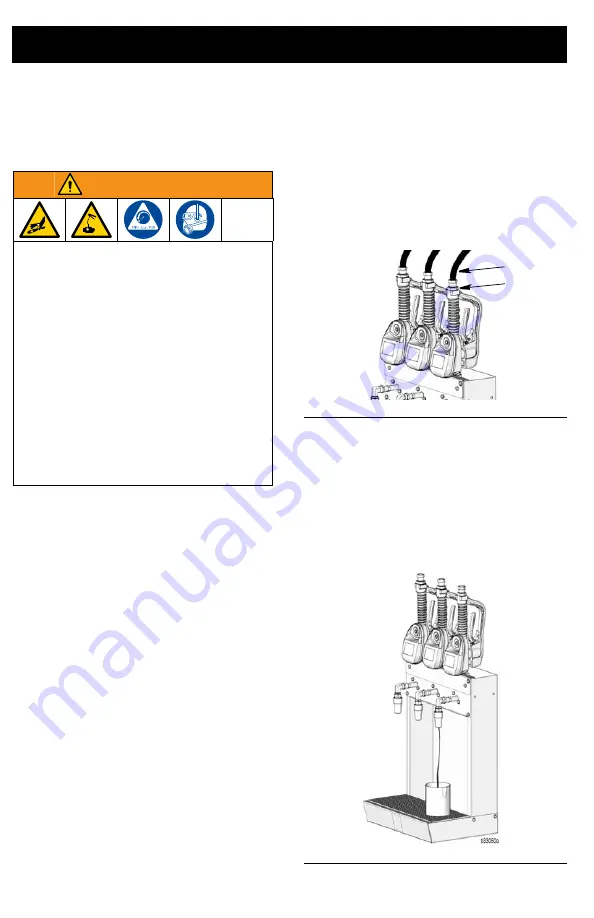
Repair and Maintenance
6
3A5573C
Repair and Maintenance
Pressure Relief Procedure
1.
Turn off power supply to the pump.
2.
Place a container under the drain valve
on the oil bar (F
. 18). Open the nozzle.
3.
Pull trigger to dispense as much of the
fluid as possible to relieve pressure.
4.
Leave the nozzle open until you are
ready to pressurize the system.
Oil Bar Disassembly
1.
Relieve pressure. See the Pressure
Relief Procedure.
2.
Disconnect fluid distribution lines (c)
from fitting (3) (see F
3.
Pull trigger to dispense as much of the
fluid remaining in the line as possible
(F
NOTE:
A collection container should
already be in place and the nozzle
should be open after performing
Pressure Relief Procedure (Step 1).
WARNING
PRESSURIZED FLUID HAZARD
This equipment stays pressurized until
pressure is manually relieved. To help pre-
vent serious injury from pressurized fluid,
such as skin injection, splashing fluid and
moving parts, follow the Pressure Relief
Procedure when you stop dispensing and
before cleaning, checking, or servicing the
equipment.
PERSONAL PROTECTIVE EQUIPMENT
Wear appropriate protective equipment
when in the work area to help prevent
serious injury, including eye injury, hearing
loss, inhalation of toxic fumes, and burns.
F
IG
. 17
F
IG
. 18
3
c
Summary of Contents for Pulse 25D121
Page 11: ...NOTES 3A5573C 11 NOTES...