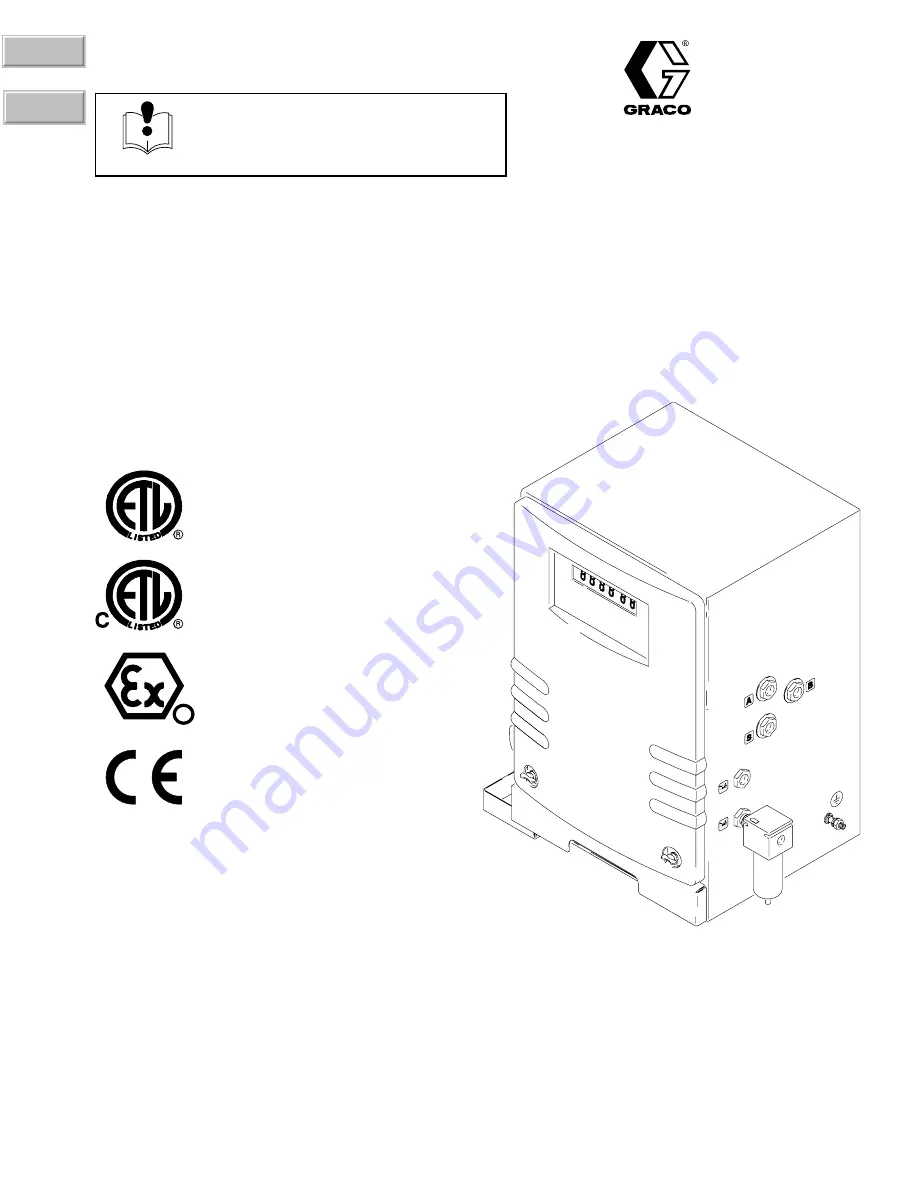
308783
Rev. C
Supersedes B
First choice when
quality counts.
Certified to CAN/CSA
22.2 No. E79–11–95
Conforms to ANSI/UL
standard 2279
Recognized Component
EExia II A T4
98D.123384
Intrinsically Safe for Hazardous Locations
Class
I
; Division 1; Group D*
*
If an external power supply is connected to the control, the control
is no longer intrinsically safe and the control, as well as the power
supply, must not be operated in hazardous locations.
If a printer is connected to the control, Printer Barrier Kit 240652
must be installed to maintain intrinsic safety. If the printer is
installed without the Printer Barrier Kit, the control is no longer
intrinsically safe and the control and printer must not be installed
or operated in hazardous locations.
D
7486A
INSTRUCTIONS-PARTS LIST
INSTRUCTIONS
This manual contains important
warnings and information.
READ AND KEEP FOR REFERENCE.
ProMix
Control Assembly
For proportional mixing of plural component coatings
3000 psi (21 MPa, 207 bar) Maximum Working Fluid Pressure
4000 psi (28 MPa, 276 bar) Maximum Fluid Working Pressure
with Part No. 239954 High Pressure Spring Kit
3000 psi (21 MPa, 207 bar) Maximum Solvent Supply Pressure
100 psi (0.7 MPa, 7 bar) Maximum Working Air Pressure
Part No. 239735
GRACO INC.
P.O. BOX 1441
MINNEAPOLIS, MN
55440–1441
COPYRIGHT 1997, GRACO INC.
Graco Inc. is registered to I.S. EN ISO 9001