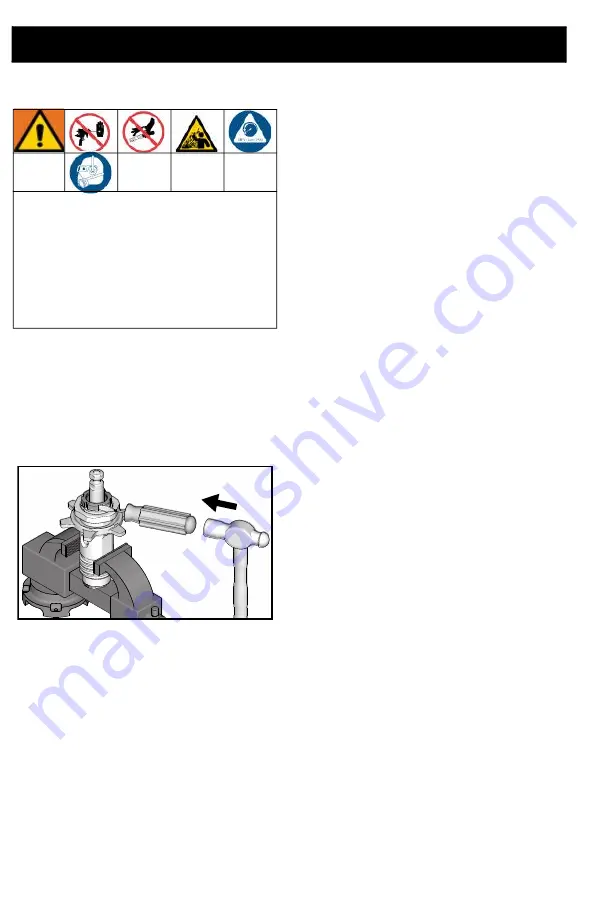
Repair
16
334599L
Throat Packing Adjustment
When pump packings begin to leak after
much use, perform
, page 5 and tighten packing nut
down until leakage stops or lessens. This
allows approximately 100 gallons of
additional operation before a repacking is
required. Packing nut can be tightened
without o-ring removal.
This equipment stays pressurized until
pressure is manually relieved. To help
prevent serious injury from pressurized
fluid, such as skin injection, splashed
fluid and moving parts, follow the
Pressure Relief Procedure
whenever
sprayer is stopped and before sprayer is
cleaned or checked, and before
equipment is serviced.
ti24988a