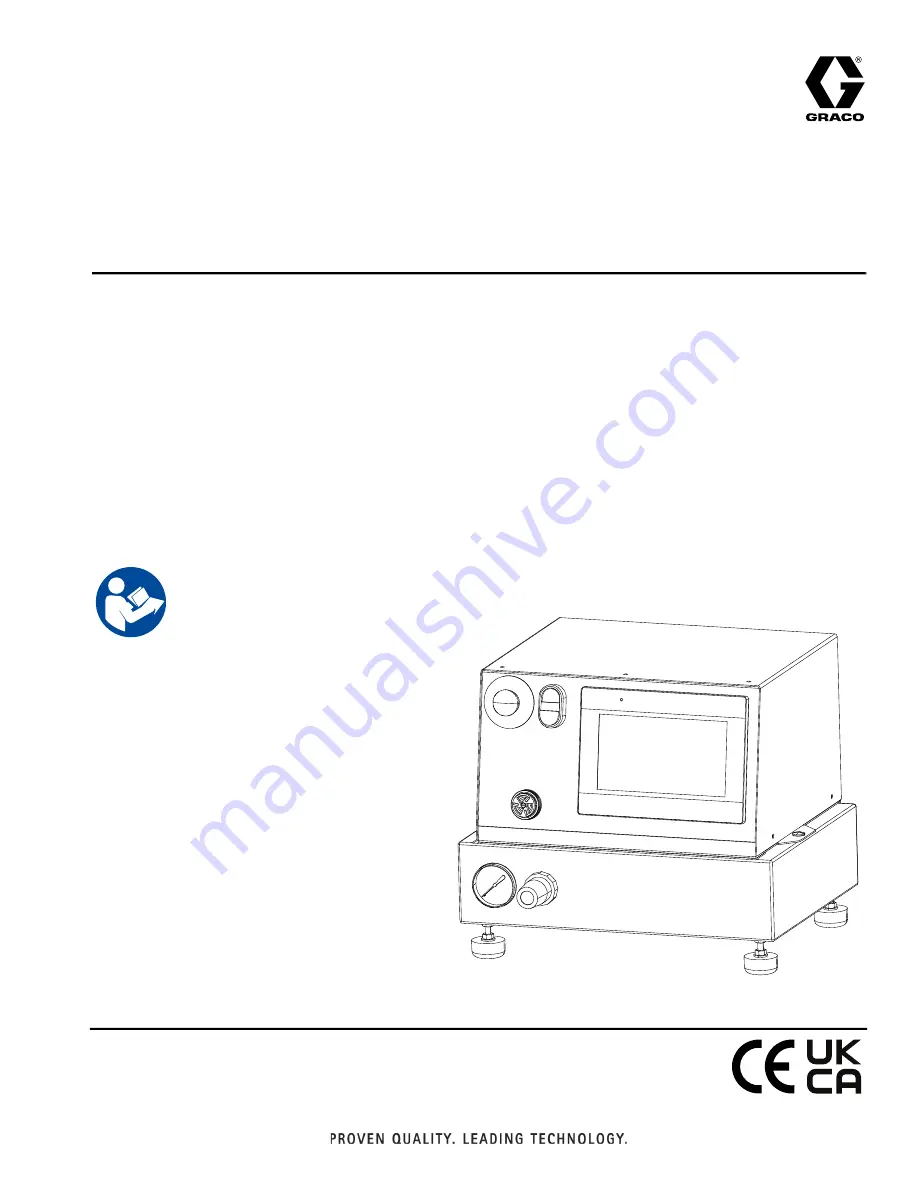
313877J
EN
Setup - Operation - Parts
PD44
Control Box
Meter, mix and dispense system for two-component micro-dispensing of sealants and
adhesives. For professional use only.
Not approved for use in explosive atmospheres or hazardous (classified) locations.
26C940
Micrometer PD44 Control Box
100 psi (0.7 MPa, 7 bar) Maximum Air Working Pressure
See page 2 for model information.
Important Safety Instructions
Read all warnings and instructions in this
manual before using the equipment.
Save these instructions.