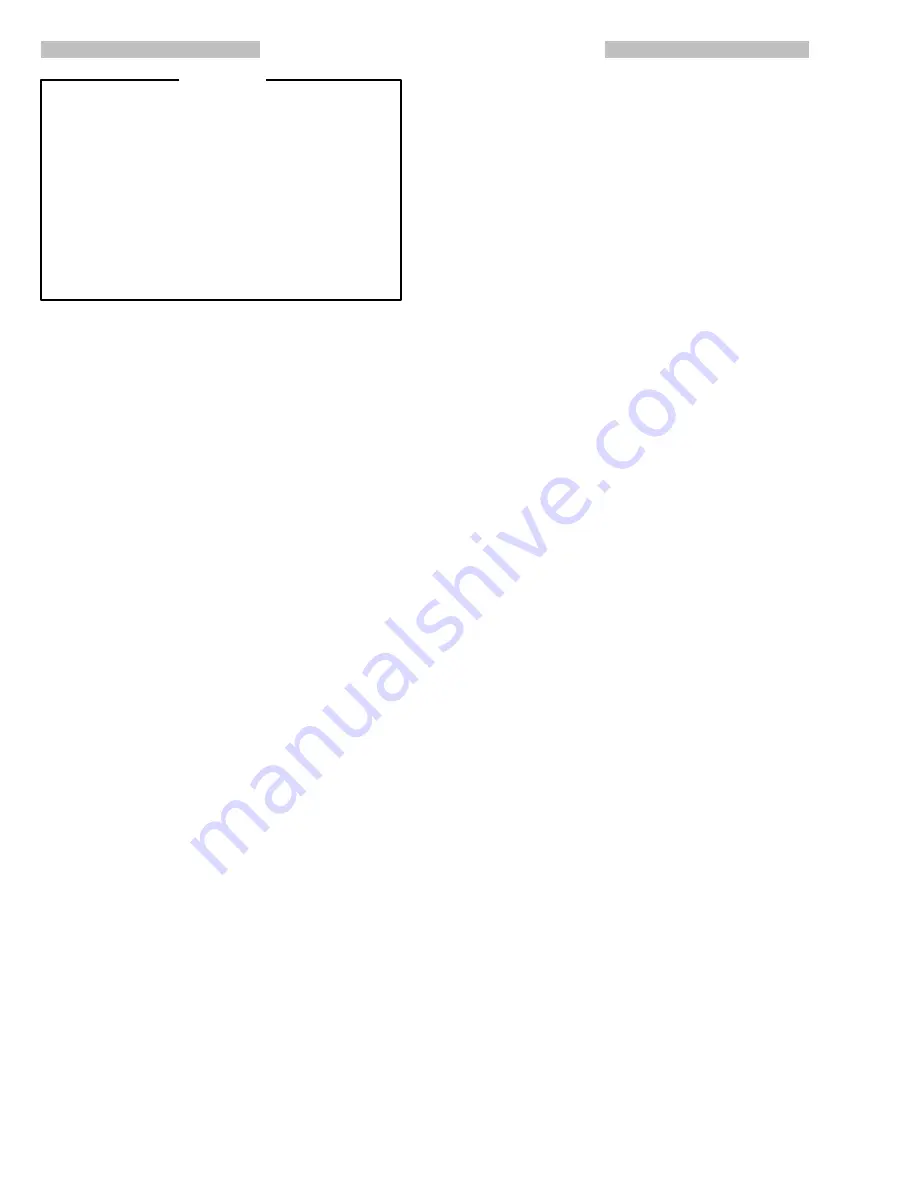
8
306–646
DISPLACEMENT PUMP SERVICE
Moving parts can pinch or amputate your fingers or
other body parts. When the pump is operating, the
priming piston (located at the pump intake) and the
air motor piston (located behind the air motor
shield) move. Therefore, NEVER operate the pump
with the air motor shield removed, and keep your
fingers and hands away from the priming piston.
Before attempting to clear an obstruction from the
priming piston or service the pump, follow the
Pres-
sure Relief Procedure Warning
on page 7 to pre-
vent the pump from starting accidentally.
WARNING
Before You Start (All Models)
1. Repair Kit 220–861 is available. See pages 13 and
15. For the best results, use all the new parts in the
kit, even if the old ones look good. Repair kit parts are
indicated in the text and the parts list with an asterisk,
for example (27*).
2. To reduce down time, keep spare parts on hand.
Recommended spare parts are indicated in the parts
list with a double asterisk, for example (41**).
3. The gland/packing stacks (64*, 65*) are preas-
sembled.
Do not disassemble the stacks when in-
stalling them in the pump.
4. For air motor service and parts information, refer to
manual 307–049 for motor Model 208–356, manual
306–968 for motor Model 206–647, manual 307–304
for motor Model 215–255, or manual 307–741 for
motor Model 220–106.
5. If possible, flush the pump before service with a com-
patible solvent. Follow the
Pressure Relief Proce-
dure Warning
on page 7. Stop the pump at the bot-
tom of its stroke.
6. Disconnect all the hoses. Remove the pump from its
mounting and clamp it in a vise.
Model 204–641 Displacement Pump (Used on
Models 204–287, 215–873 and 222–248)
Disassembly
NOTE:
Refer to Fig 2 and the parts drawing.
1. Remove the cotter pin (41). Unscrew the coupling
nut (50) and the three tie rod locknuts (44). Pull the
displacement pump (2) off the air motor (1).
2. Remove the cotter pin (42). Loosen the locknut (45).
Unscrew the connecting rod (53) from the upper cap
(33).
3. Insert a 1/4 in. (6 mm) diameter rod in the holes of the
packing nut/wet–cup (21), and loosen it. Push the
displacement rod (18) down until the priming piston
(37) clears the intake valve housing (28). Remove
the nut (6), priming piston (37), valve plate (36) and
plate guide (31).
4. Unscrew the four tie bolts (8) and pull the intake valve
housing (28) off the pump. Pull the priming rod (32)
and displacement rod (18) out of the bottom of the
cylinder (39). Remove the pin (7) and unscrew the
priming rod (32) from the connecting rod (20).
5. Pull the cylinder (39) down out of the outlet housing
(26). Inspect the inner surface of the cylinder and the
outer surface of the displacement rod (18) for
scratches or scoring, which can cause premature
packing wear and leaking. To check, run a finger over
the surface or hold the part up to the light at an angle.
6. Disassemble the intake valve (3). Clean and inspect
all parts, replacing as necessary . Check the intake
valve seat (30) for nicks or damage.
7. Unscrew the upper cap (33) from the connecting rod
(20). Pull the displacement rod (18) off the lower cap
(19), and remove the piston assembly from the con-
necting rod. Disassemble the piston.
8. Unscrew the packing nut/wet–cup (21). Remove the
wiper seal (66). Remove the throat packings from the
outlet housing (26).
9. Clean and inspect all parts, replacing as necessary.
Reassembly
NOTE:
Refer to Fig 2 and the parts drawing during the
following procedure.
1. See Detail A of Fig 2. The gland/packing stack (64*)
for the throat is preassembled.
Do not disassemble
the stack.
Lubricate the gland/packing stack and in-
stall it into the outlet housing (26).
Be sure the lips of
the v–packings are facing down. Install the wiper
seal (66) in the groove of the wet–cup (21)
with the
lips facing down. Loosely install the packing nut/wet–
cup (21).
2. See Detail B of Fig 2. Install the two bearings (35*)
and the u–cup packing (56*) on the piston (38).
Be
sure the lips of the packing are facing up. Install the
small o–ring (15) in the lower cap (19) and the larger
o–ring (17) on the outside of the lower cap.
3. Install the piston (38), valve plate (34), and lower cap
(19) on the connecting rod (20).
4. Insert the connecting rod (20) into the displacement
rod (18) so the lower cap (19) fits into the bottom of
the displacement rod. Screw the top cap (33) onto
the connecting rod (20) until it is tight against the top
of the displacement rod (18).
5. Install one copper gasket (27*) in the outlet housing
(26). Screw the priming rod (32) into the connecting
rod (20) and secure with the pin (7). Push the dis-
placement rod (18) and priming rod (32) up into the
outlet housing (26) so the top of the displacement rod
just protrudes from the packing nut/wet–cup (21).
Lubricate the priming rod (32).
6. Install the cylinder (39) in the outlet housing (26), be-
ing careful not to scratch the polished inner surface
of the cylinder.
7. See Detail C of Fig 2. Slide the intake valve gland/
packing stack (65*) into the intake valve seal housing
(3).
Do not disassemble the stack.
Be sure the lips
of the v–packings are facing up. Tighten the packing
nut (11). Install the valve seat (30) in the intake valve
housing (28). Place the intake valve seal housing (3)
on the seat (30).
8. Install two copper gaskets (27*) on the intake valve
stop (29). Install the stop in the intake valve housing
(28).