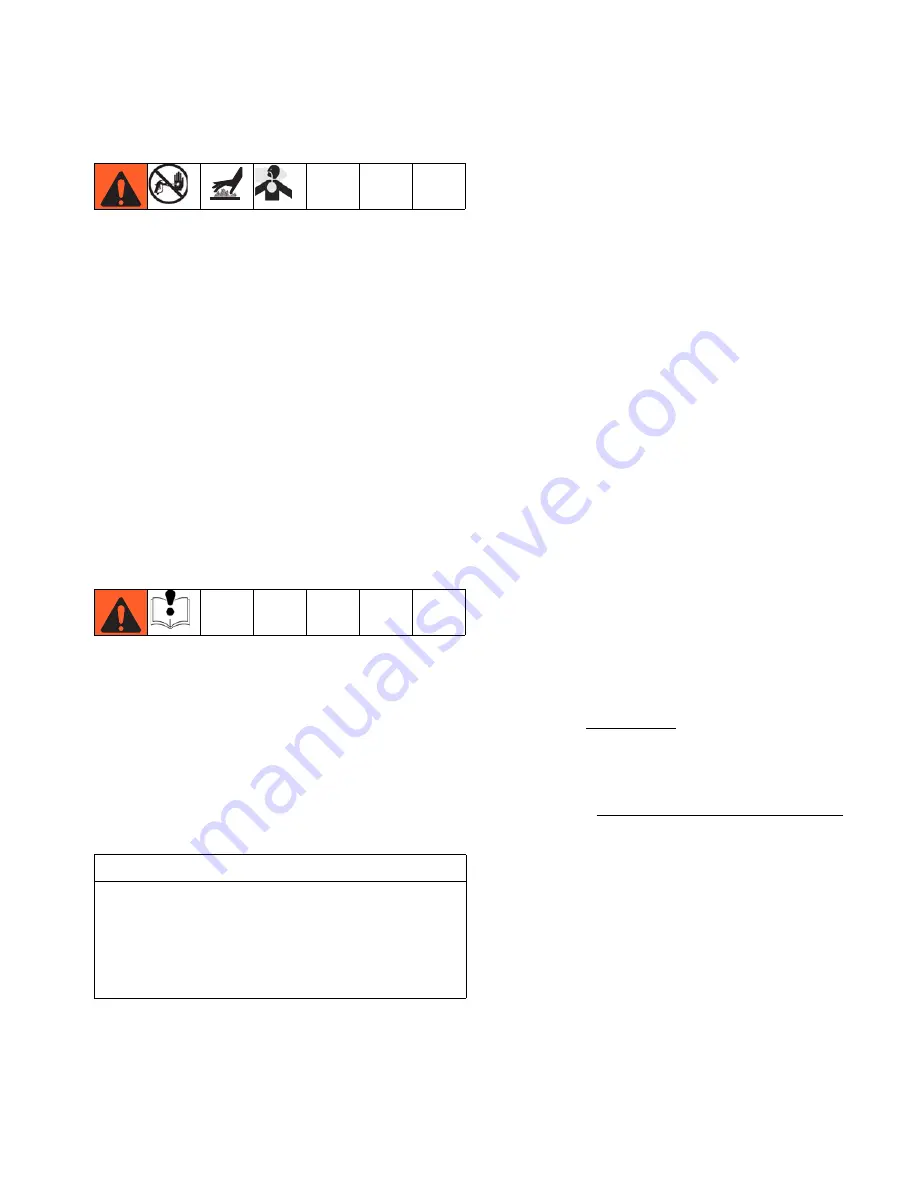
Operation
309834W
7
Operation
Pressure Relief Procedure
1. Turn off the fluid supply to the meter.
2. Shut off all electrical power to the fluid system.
3. Follow the Pressure Relief Procedure for your fluid
system dispensing device.
Flow Meter Function
This is a positive displacement, gear flow meter. The
gear flow meter is highly accurate, even with low flow
rates. The fluid flowing through the meter rotates the
gears. The gear position is monitored by a sensor
device. An electrical impulse is produced by the sensor
each time a gear tooth moves past it.
Recommended Usage
•
See the
Technical Data
for fluid and ambient tem-
perature limits.
•
Only use the flow meter with fluids that are compati-
ble with the “Wetted Parts” listed in the
Technical
Data
.
Flow Volume Range
See
Technical Data
on page 18 for flow volume range.
Flow Meter Verification
The factory calibration factor (k factor) for the flow meter
is stated in the
Technical Data
section of the manual.
This calibration factor is the number of flow meter pulses
per liter, as determined by a measurement with oil.
Most sealant and adhesive materials are compressible
and, since the flow meter is measuring the material
under high pressure, the actual volume of material may
vary slightly from the measured volume due to this com-
pressibility.
To adjust the flow meter k factor to reflect the uncom-
pressed volume dispensed more accurately, perform
the following steps:
1. Obtain a beaker, 500 cc or larger, and measure the
mass of the empty beaker.
2. Manually dispense material into the beaker.
3. Record both the volume displayed and the current
flow meter k factor (pulses per liter).
4. Measure the mass of the full beaker.
5. Subtract the weight of the empty beaker to deter-
mine the fluid mass.
6. Calculate the actual volume dispensed:
fluid mass (g) = volume (cc)
density (g/cc)
7. Calculate the new flow meter k factor:
k factor = displayed volume (cc) X k factor (old)
measured volume (cc)
8. Repeat steps 1-7 to validate the k factor.
CAUTION
The flow meter gears and bearings can be damaged if
they rotate at too high a speed. To avoid high speed
rotation, open the fluid valve gradually. Do not
over-speed the gear with air or solvent. To prolong
meter life, do not use the meter above its maximum
flow rate.