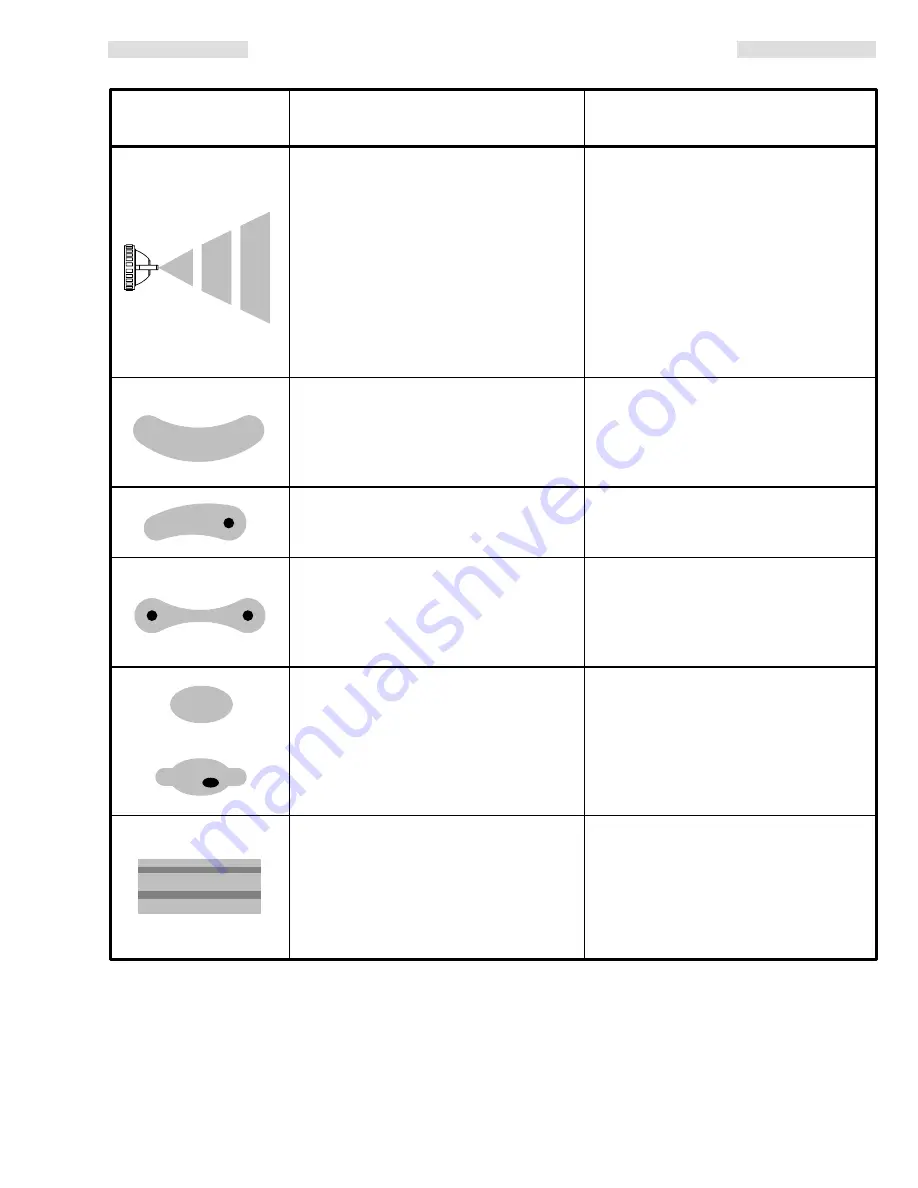
308-188 7
SPRAY PATTERN TROUBLESHOOTING CHART
PROBLEM:
CAUSE
SOLUTION
IMPROPER SPRAY
PATTERN
Insufficient fluid supply.
Adjust fluid regulator or fill fluid tank.
Loose fluid nozzle or damaged fluid
Tighten or replace fluid nozzle (2) and
nozzle taper seat.
needle (1).
Dirt between fluid nozzle, taper seat
Clean.
and body.
Loose or cracked fluid inlet fitting (4a).
Tighten or replace fitting.
Loose fluid tube in pressure tank.
Tighten fluid tube.
Dry or worn fluid needle packings (10, 16)
Lubricate or replace packings;
or loose packing nuts (9) permit air to get
tighten packing nuts.
into fluid passage.
Fluid build-up on air cap; partially
Clean with soft implement or
clogged horn holes. Full air pressure
submerge in suitable solvent and
from clean horn hole forces fan pattern
wipe clean.
toward clogged end.
Damaged fluid nozzle or air cap holes.
Replace damaged part.
Fluid build-up on the perimeter of fluid
Remove obstruction. Never use wire
nozzle orifice, or partially clogged fluid
or hard instruments.
nozzle orifice.
Too high atomization air pressure.
Reduce air pressure or adjust air
adjusting valve (5).
Fluid too thin.
Regulate fluid viscosity.
Not enough fluid pressure.
Increase fluid pressure.
Low atomization air pressure.
Increase air pressure or adjust air
adjusting valve (5).
Fluid too thick.
Regulate fluid viscosity.
Too much fluid.
Reduce fluid pressure.
Adjust fluid adjusting valve (6) until
proper pattern is obtained.
Last coat of fluid applied too wet.
Apply drier finish with multiple
strokes.
Too much air pressure.
Use least air pressure necessary.
Insufficient air pressure.
Increase air pressure.
Non-uniform spray pattern.
Clean or replace air cap.
Fluttering or spitting
spray
Streaks
NOTE: Some improper patterns are caused by the improper balance between air and fluid.