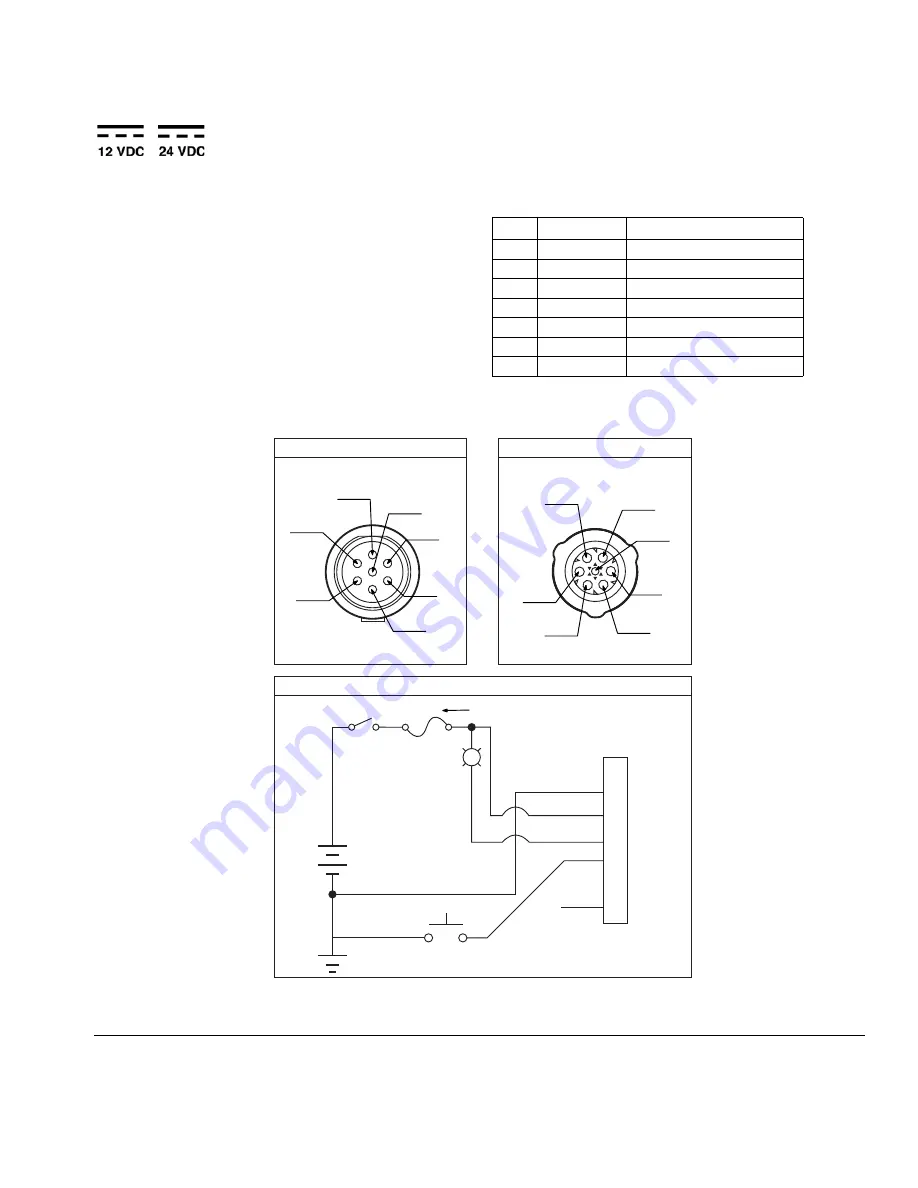
Installation
332305B
17
Power CPC DC - 5 Wire
Part No.: 126218: 15 ft (4.5 m)
Part No.: 126219: 20 ft (6.1 m)
Part No.: 126220: 30 ft (9.1 m)
NOTE:
An Illuminated Remote Run Button Kit: 571030,
571031 for starting a manual run cycle if used in con-
junction with a 5-wire CPC cable, is available from
Graco. Contact your local Graco distributor or Graco
Customer Service for additional information about these
kits.
Pin and Related Wire Color (F
IG
. 6)
Pin
Pin Name
Color
1
Not Used
Not Used
2
-VDC
Black
3
+VDC
Red
4
LIGHT
White
5
MANUAL
ORANGE
6
Not Used
Not Used
7
Not Used
Green
F
IG
. 6
(1)
(2)
(3)
(4)
(5)
(6)
(7)
1
2
3
4
5
6
7
L
Fuse
12V-pump - 7.5A - Graco kit #571039
24V pump - 4A - Graco kit #571040
Example Wiring Diagram
Connector on Housing
Connector on Cable
(1)
(3)
(2)
(7)
(6)
(5)
(4)