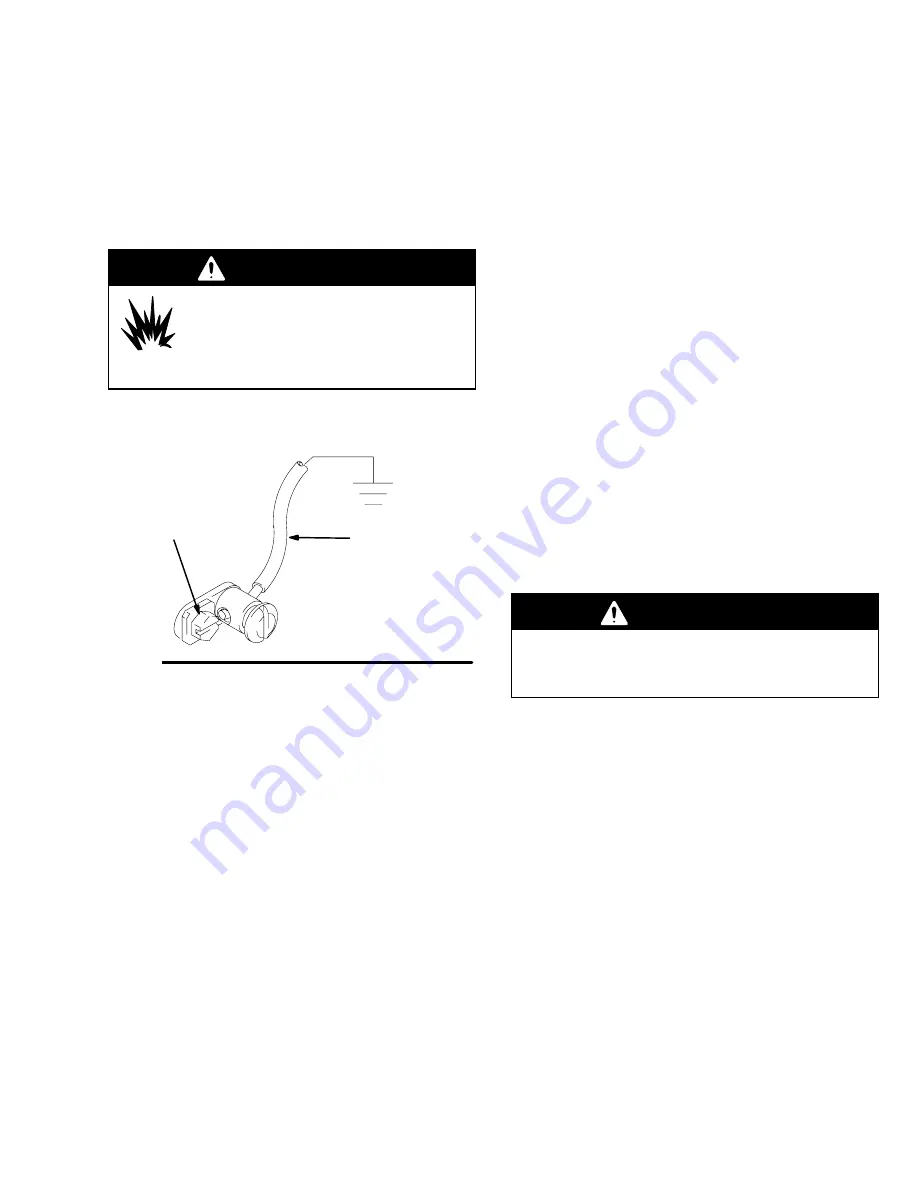
5
309407
Installation
NOTE:
Reference numbers and letters in parentheses
in the text refer to the callouts in the figures and the
parts drawing.
NOTE:
Always use Genuine Graco Parts and
Accessories, available from your Graco distributor.
Grounding
WARNING
FIRE AND EXPLOSION HAZARD
Before operating the pump, ground the
system as explained below. Also read
the section
FIRE OR EXPLOSION HAZ-
ARD
on page 3.
D
Pump:
Use a ground wire and clamp as shown
below.
Fig. 1
TI1052
Y
Z
D
Air and fluid hoses:
Use only electrically conductive
hoses.
D
Air compressor:
Follow manufacturer’s
recommendations.
D
Dispensing valve:
Ground through connection to a
properly grounded fluid hose and pump.
D
Object being dispensed to:
Follow your local code.
D
Solvent pails used when flushing:
Follow your local
code. Use only metal pails, which are conductive,
placed on a grounded surface. Do not place the pail
on a nonconductive surface, such as paper or
cardboard, which interrupts the grounding
continuity.
D
To maintain grounding continuity when flushing or
relieving pressure
, hold a metal part of the
dispensing gun firmly to the side of a grounded
metal
pail, then trigger the gun to ground the pump.
To ground the pump,
remove the ground screw (Z)
and insert through the eye of the ring terminal at end of
ground wire (Y). Fasten the ground screw back onto
the pump and tighten securely. Connect the other end
of the ground wire to a true earth ground. See Fig. 1.
To order a ground wire and clamp, order Part No.
222011.
Mounting the Pump
WARNING
Mount the pump securely so that it cannot move
around during operation. Failure to do so could
result in personal injury or equipment damage.
D
Select a convenient location for the equipment to
ensure easy operator access to the pump air
controls, sufficient room to change supply
containers, and a secure mounting platform.
D
If you are mounting the pump directly on the supply
tank, position the pump so its intake valve is no
more than 1 in. (25 mm) from the bottom of the
container. Mount the pump to the cover or other
suitable mounting device.