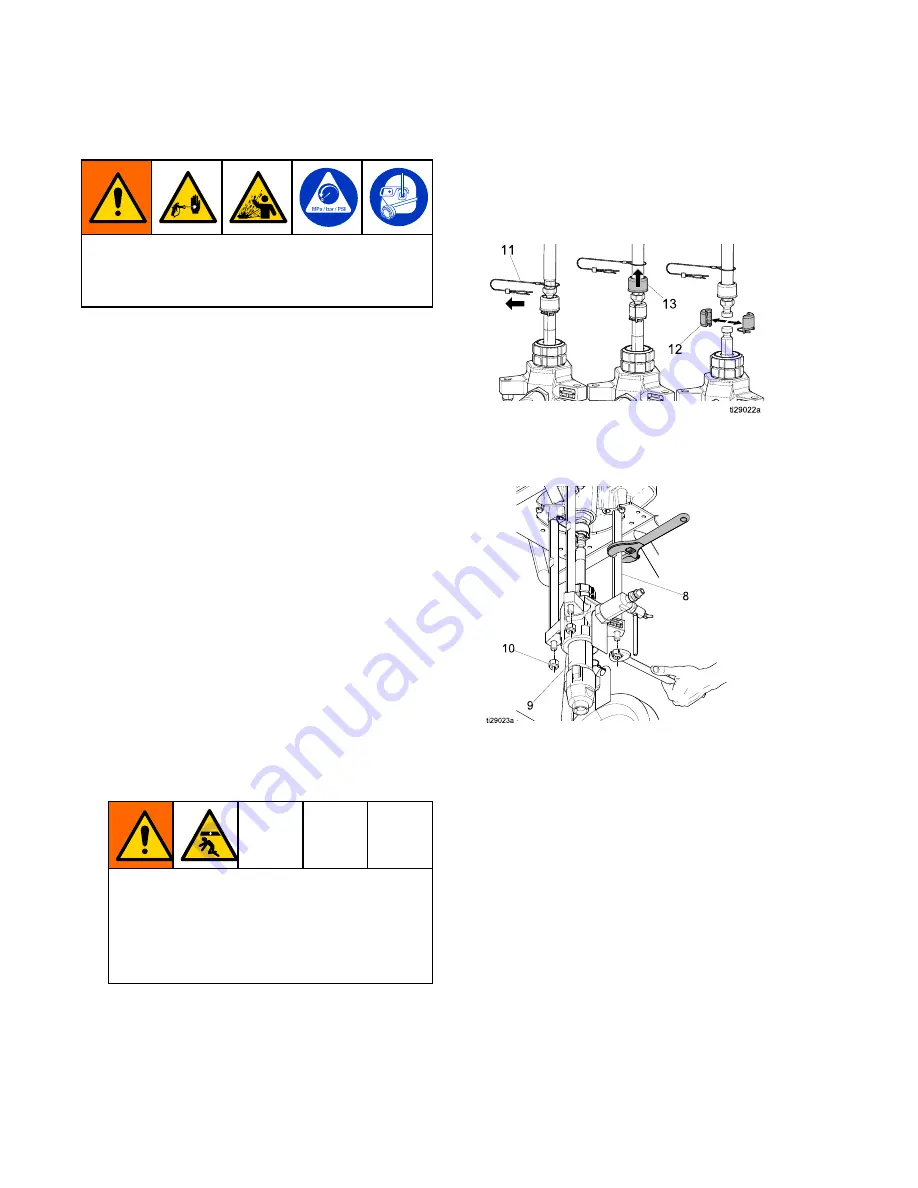
Repair
Repair
Repair
Repair
To reduce the risk of injury due to skin
injection and splashing, perform the
Pressure Relief Procedure, page 12
before
performing any repair procedure.
Xtreme
Xtreme
Xtreme Lower
Lower
Lower Removal
Removal
Removal
Required
Required
Required Tools
Tools
Tools
• Set of adjustable wrenches
• Torque wrenches
• Rubber mallet
• Thread lubricant
• Anti-seize lubricant
• Thread sealant
Disconnect
Disconnect
Disconnect and
and
and Reconnect
Reconnect
Reconnect Lower
Lower
Lower
1.
Flush the pump (see
Prime/Flush, page 13
).
Stop the pump at bottom of its stroke.
2.
Perform
Pressure Relief Procedure, page 12
.
3.
Disconnect the unit from the power source.
4.
Disconnect the fluid hose, then disconnect the
suction hose. Hold the fluid inlet fitting with
a wrench to keep it from loosening while you
disconnect the suction hose.
Do not lift the pump by the lift ring when the
weight exceeds 360 kg (800 lb). The lift ring
could fail and result in injury.
Use caution when disconnecting the lower;
they can weigh up to 25 kg (55 lb). Take
appropriate precautions.
5.
If the driver does not require service, leave it
attached to its mounting.
6.
Remove clip (11) and slide coupling cover (13)
up to remove coupling (12).
7.
Use a wrench to hold the tie rod flats to keep
rods (8) from turning. Unscrew nuts (10) and
remove the lower (9).
8.
Refer to the Xtreme Lower manual (311762) to
service the lower.
9.
Reconnect the lower by following the disconnect
steps in reverse order.
NOTE:
NOTE:
NOTE: Torque the nuts (10) to 50–60 ft-lb (68–81
N•m).
22
3A3164D