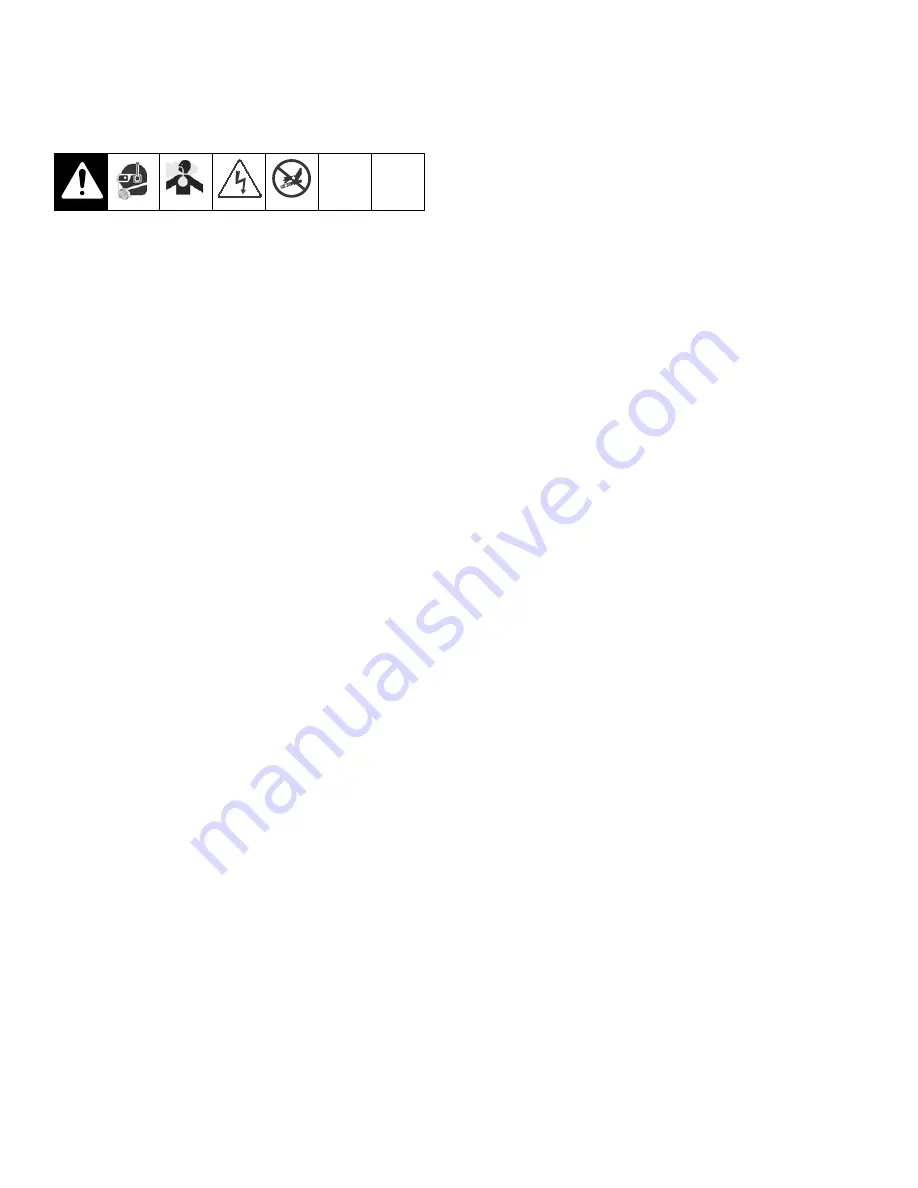
Pouring Operation
42
313813A
Pouring Operation
Low and High Pressure
Circulation
When the metering pump motors are first turned on, the
machine will enter low pressure circulation. After that
the machine will stay in or return to low pressure circula-
tion if the following conditions are met.
•
A pour has not occurred since the metering pump
motors were started
•
If the preset High Pressure Hold Time has elapsed
since the last pour occurred and calibrate mode has
not been selected.
When any of the following conditions are met, the
machine will be in high pressure circulation.
•
The pour start button has been pressed but Pres-
sure-Build Time has not yet elapsed
•
A pour has finished but High Pressure Hold Time
has not yet elapsed
Pouring Requirements
The following requirements must be met in order for a
pour to occur.
•
Main Power on
•
Control Power on
•
Night Mode off
•
Manual or Automatic Mode selected
•
Iso and Poly Metering Pump Motors on
•
Iso and Poly Fail To Build Pour Pressure Alarm inac-
tive
•
Iso and Poly Low Pour Pressure Alarm inactive
•
Iso and Poly Tank Low Level Alarms inactive
If all of the above requirements are satisfied, then the
“MixHead Pour Ready” indicator on the Status Screen
will be green, see page 19.
Beginning the Pour
After both streams reach the required pour pressure and
the preset pressure build time elapses, the MixHead is
commanded to open and the pour occurs.