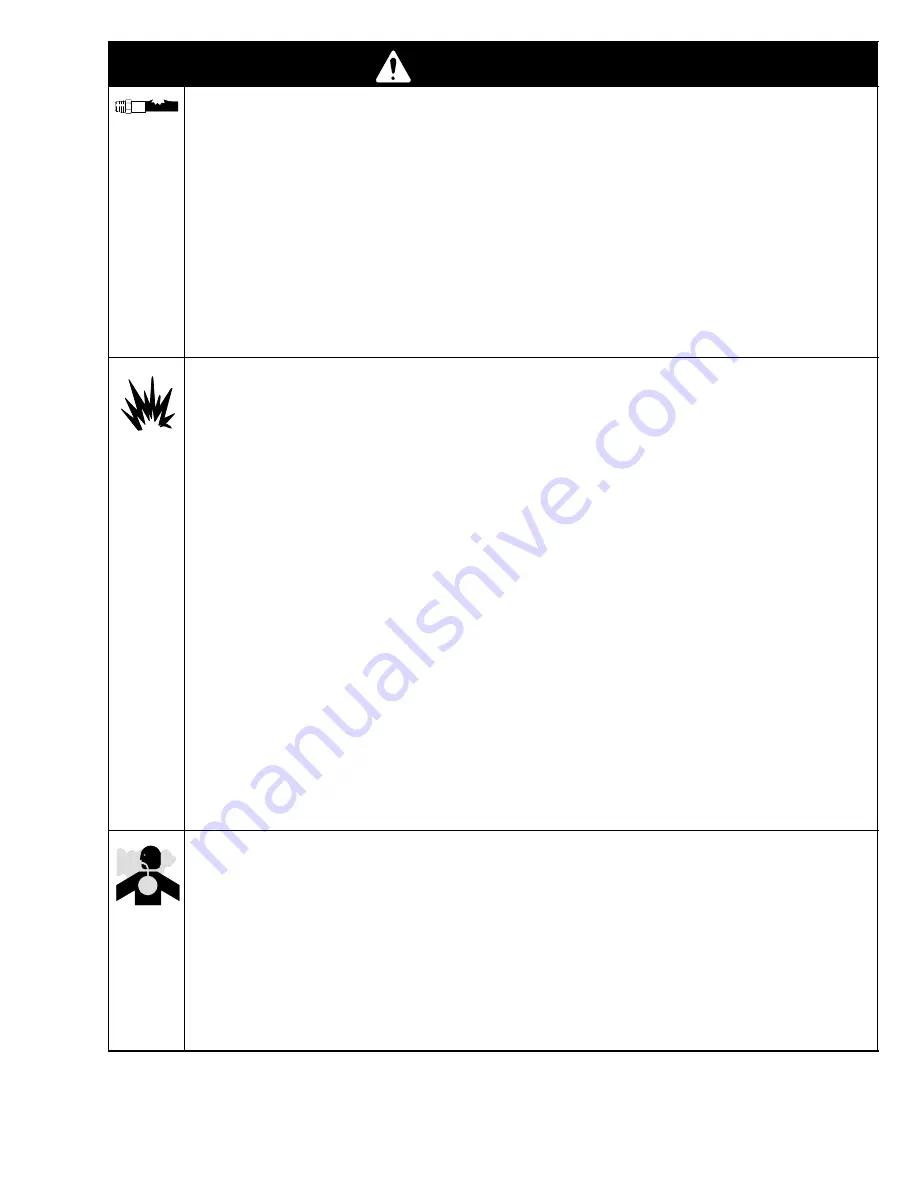
307133
3
WARNING
PRESSURIZED EQUIPMENT HAZARD
Spray from the gun, hose leaks, or ruptured components can splash fluid in the eyes or on the skin
and cause serious injury.
D
Do not stop or deflect fluid leaks with your hand, body, glove, or rag.
D
Follow the Pressure Relief Procedure on page 6 whenever you: are instructed to relieve the
pressure; stop spraying; clean, check, or service the equipment; and install or clean the fluid
nozzle.
D
Tighten all the fluid connections before operating the equipment.
D
Check the hoses, tubes, and couplings daily. Replace worn, damaged, or loose parts immediately.
Permanently coupled hoses cannot be repaired; replace the entire hose.
FIRE AND EXPLOSION HAZARD
Improper grounding, poor ventilation, open flames or sparks can cause a hazardous condition and
result in a fire or explosion and serious injury.
D
Ground all equipment in the work area. Refer to Grounding on page 4.
D
If there is any static sparking or you feel an electric shock while using this equipment, stop spray-
ing immediately. Do not use the equipment until you identify and correct the problem.
D
Provide fresh air ventilation to avoid the buildup of flammable fumes from solvents or the fluid
being sprayed.
D
Keep the spray area free of debris, including solvent, rags, and gasoline.
D
Electrically disconnect all equipment in the spray area.
D
Extinguish all open flames or pilot lights in the spray area.
D
Do not smoke in the spray area.
D
Do not turn on or off any light switch in the spray area while operating or if fumes are present.
D
Do not operate a gasoline engine in the spray area.
D
Keep a fire extinguisher in the work area.
TOXIC FLUID HAZARD
Hazardous fluid or toxic fumes can cause serious injury or death if splashed in the eyes or on the skin,
inhaled, or swallowed.
D
Know the specific hazards of the fluid you are using.
D
Store hazardous fluid in an approved container. Dispose of hazardous fluid according to all local,
state and national guidelines.
D
Always wear protective eyewear, gloves, clothing and respirator as recommended by the fluid and
solvent manufacturer.