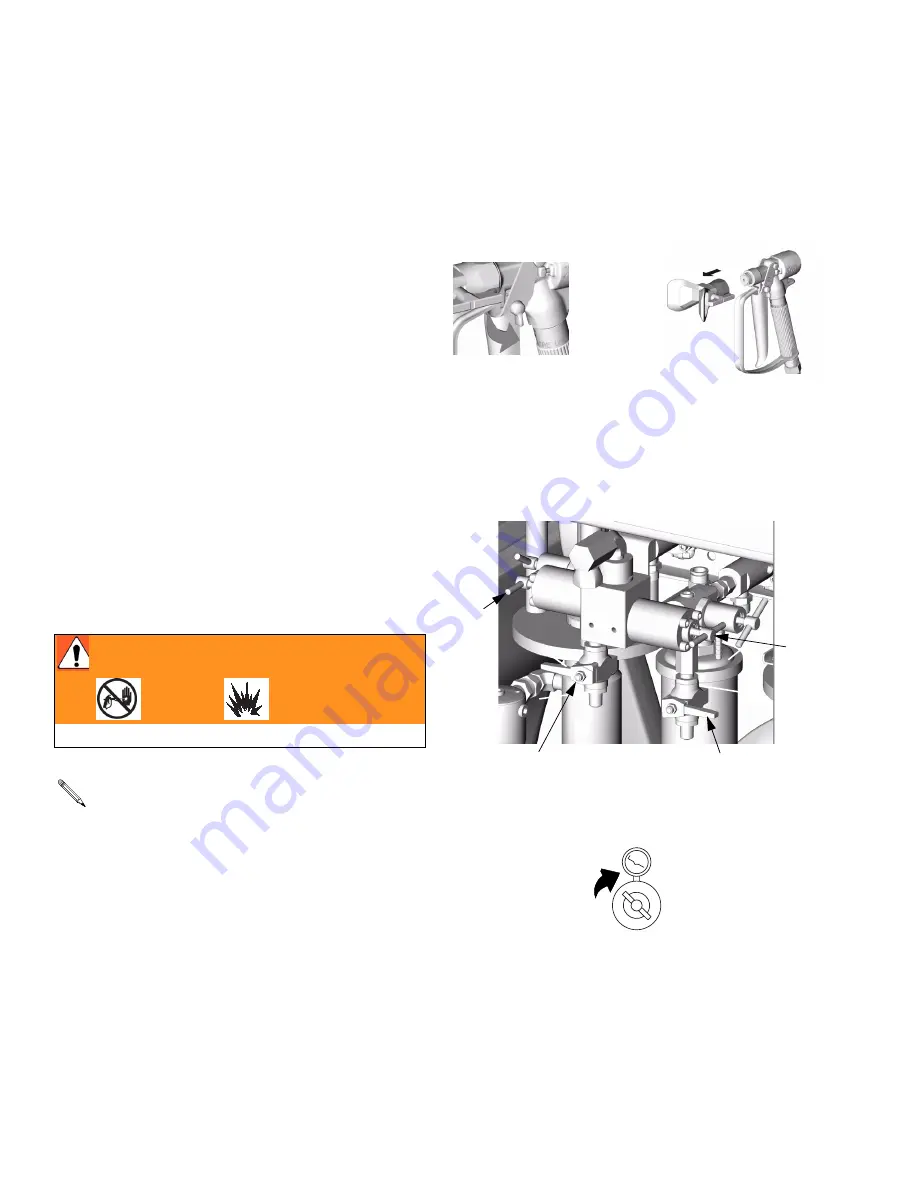
Flushing
16
310665E
Flushing
There are times when you only want to flush the fluid
manifold, such as:
•
breaks in spraying
•
overnight shutdown
•
end of potlife
In this manual, that procedure is referred to as
. You can flush the fluid manifold by
connecting a solvent pump to the fluid manifold.
Other times, you need to flush the entire system:
•
first time material is loaded into equipment*
•
color change
•
servicing
•
shutting down equipment for more than 3-1/2 hours
(depends on material)
•
putting equipment into storage
*
initial flushing, as no material has been loaded into the sys-
tem yet.
To flush the entire system, you first follow the
procedure, at right, then the
Fluid Manifold Flushing
Using Solvent Pump
WARNING
Read warnings, page 5.
•
Use the lowest possible pressure when flush-
ing to avoid splashing.
•
Before color change or shutdown for storage,
flush at a higher flow rate and for a longer
time.
•
A circulation setting is available. Consult your
distributor. Refer to page 30.
1.
, page 14.
Engage trigger lock. Remove spray tip.
2.
Ensure that shutoff valves G
A
and G
B
are open.
Connect solvent pump line to solvent purge valve J
A
and J
B
. Turn on solvent pump and open solvent
purge valve J
A
.
3.
Adjust solvent pump regulator to desired pressure;
use lowest pressure possible.
TI5183a
TI5049a
TI4957b
J
B
G
B
J
A
G
A
Summary of Contents for 234614
Page 18: ...Flushing 18 310665E...