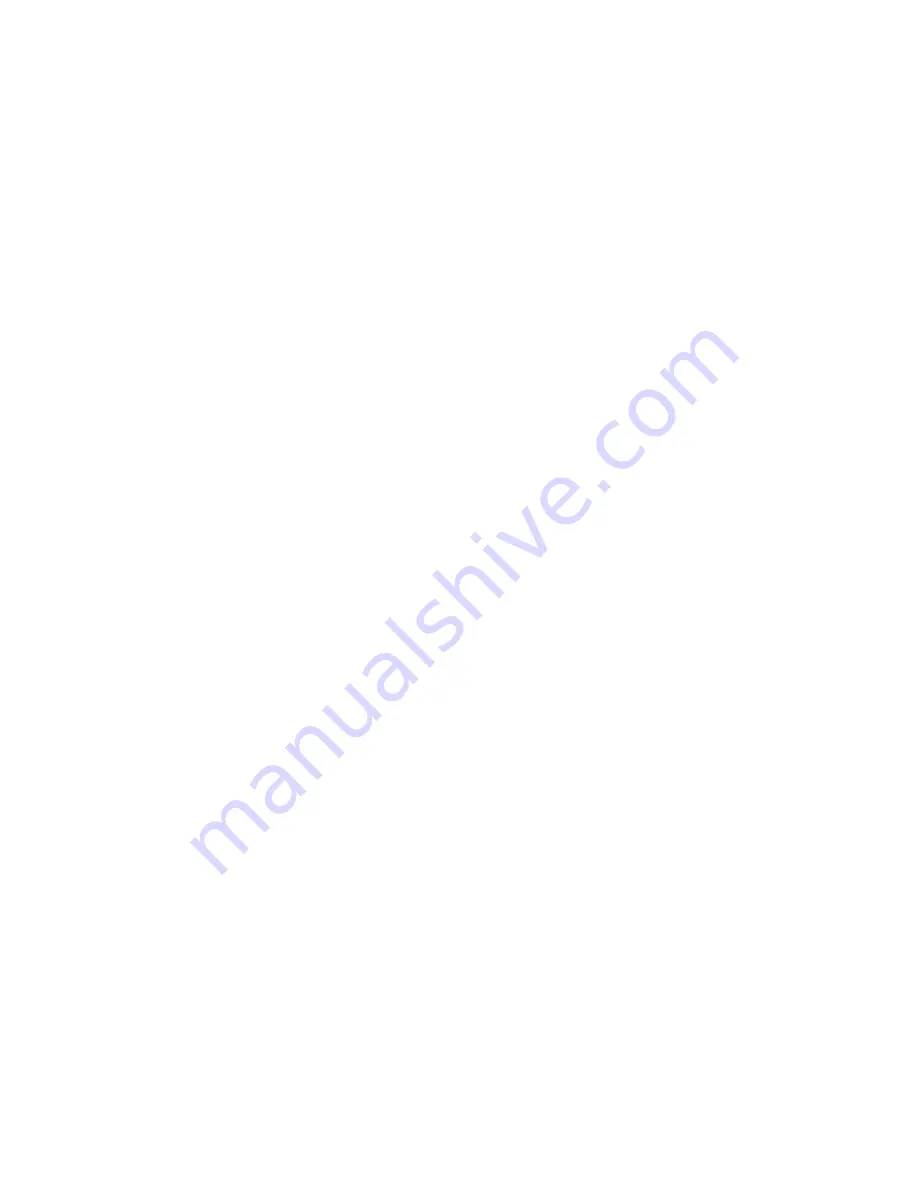
14
308655
Parts List
Model 205626, Series J
Model 222065, Series B
Model 222095, Series B
Wall-Mount Universal Pump
55-Gallon Drum Cover-Mount Pump
55-Gallon Drum Bung-Mount Pump
Includes items 1 to 113
Includes items 1 to 113, 150, and 151
Includes items 1 to 113, 150,152, and 153
Ref
No.
Part No.
Description
Qty.
1
AIR MOTOR
(items 2 to 36)
1
2*
110247
SEAL; polyurethane, nitrile
1
3
101578
SCREW, cap, hex hd
8
5
102656
MUFFLER, air exhaust
1
7
116343
SCREW, ground
1
11
156698
PACKING, o-ring
1
12
158359
ACTUATOR, air valve
1
13
158360
YOKE, trip rod
1
15
158362
PIN, toggle
2
16
158364
PIN, pivot
2
17*
158367
GROMMET, lower valve
2
18
158377
PACKING, ring seal
1
19*
158378
PACKING, o-ring
1
20*
158379
PACKING, o-ring
1
21*
160261
NUT, valve
4
22*
160618
WIRE, lock
2
23
160623
ARM, toggle
2
24
190929
RING, lift
1
25
167585
SPRING, helical compression
2
26*
170709
POPPET, exhaust valve
2
27
207391
PISTON, includes items 27a to
27c, (also includes 207385 repair kit
when ordered as a replacement
part)
1
27a
102975
SCREW, rd hd mach; 6–32 X 1/4” 2
27b
158361
CLIP, spring
2
27c
BARE PISTON
(not sold seperately)
1
28
191544
BASE, air motor
1
29
191545
ROD, displacement
1
Ref
No.
Part No.
Description
Qty.
30
15E954
CYLINDER, air motor
1
31
207150
ROD, trip
1
32*
236079
POPPET, inlet valve
2
33
119344
LABEL, designation
1
35
Y
290259
LABEL, warning
1
36
191546
BEARING, throat
1
103
100279
BALL; sst
1
104
101190
BALL; sst
1
105*
156633
PACKING, o-ring
1
107*
113564
SEAL, block, vee
1
108*
156641
PACKING, o-ring
1
109
191547
PISTON/VALVE SEAT
1
110
191548
CYLINDER, fluid
1
111
183009
VALVE HOUSING
1
112
157182
RETAINER, ball
1
113
191123
RETAINER, seal
1
150
110127
SPACER, foot
1
151
191128
TUBE, extension; 21.75” (553 mm)
1
152
191130
TUBE, extension; 26.0” (661 mm)
1
153
222308
BUNG ADAPTER
1
*
Included in Repair Kit 238751, which may be
purchased separately.
Y
Extra warning labels are available at no cost.