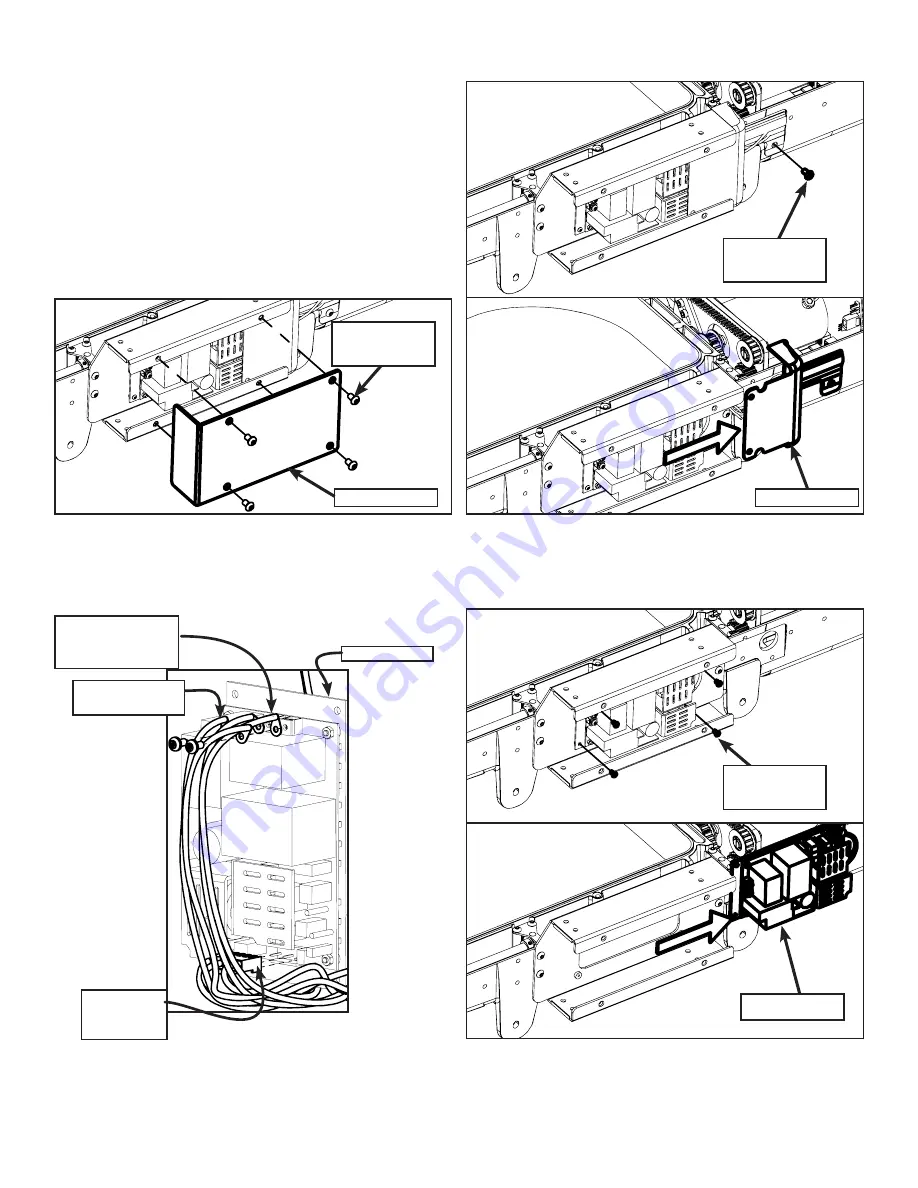
Power Supply
Main Controller
24V Power Cable
Motor Driver
24V Power Cable
(Thinner Cable)
Cable to AC
Power Supply
Cable
Bottom Cover
M6 x 10 mm
SBHCS (4)
M6 x 10 mm
SBHCS (1)
M3 x 6 mm
SBHCS (4)
Power Supply
Plastic Cover
1. Use the 4 mm Allen Wrench to remove the
screws from the Bottom Cover and remove the
Bottom Cover.
3. Detach the Cables from the Power Supply using
the Phillips Head Screw Driver.
2. Remove the Screw from the Plastic Cover and
Remove the Plastic Cover.
4. Remove (4) Screws and slide out the Power
Supply.
Tools Needed:
4 mm Allen Wrench
Phillips Head Screw Driver
|
Power Supply
Q’nique 21: Service Manual
20
Summary of Contents for Q'nique 21
Page 1: ...Service Manual 21 ...