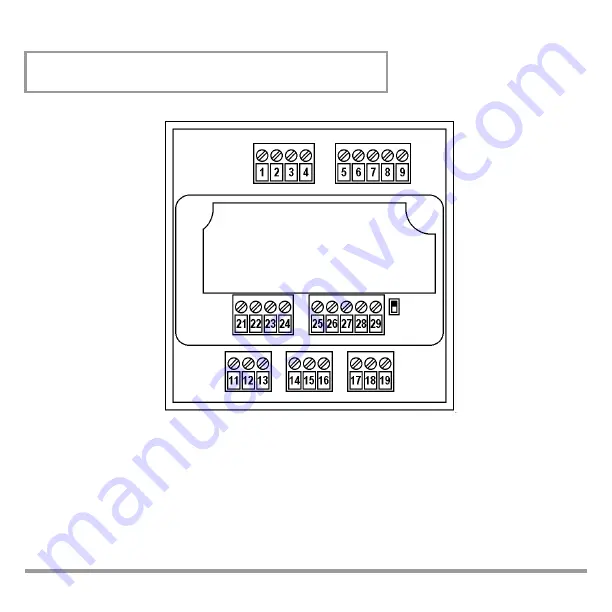
GOSSEN METRAWATT GMBH
9
EN 55022 requires the following warning as regards electromagnetic compatibility:
Figure 3, Connector Terminal Positions
Warning
This is a class A device. It may cause radio interference in residential surroundings. If this is the
case, the operator may be required to implement appropriate corrective measures.
Connectors:
Screw terminals for wire with a cross section of 1.5 square mm or
two-core wire-end ferrules with a cross-section of 2 x 0.75 square mm
Tighten screws with a manual screwdriver only! Tightening torque for all screw termi-
nals: max. 0.6 Nm