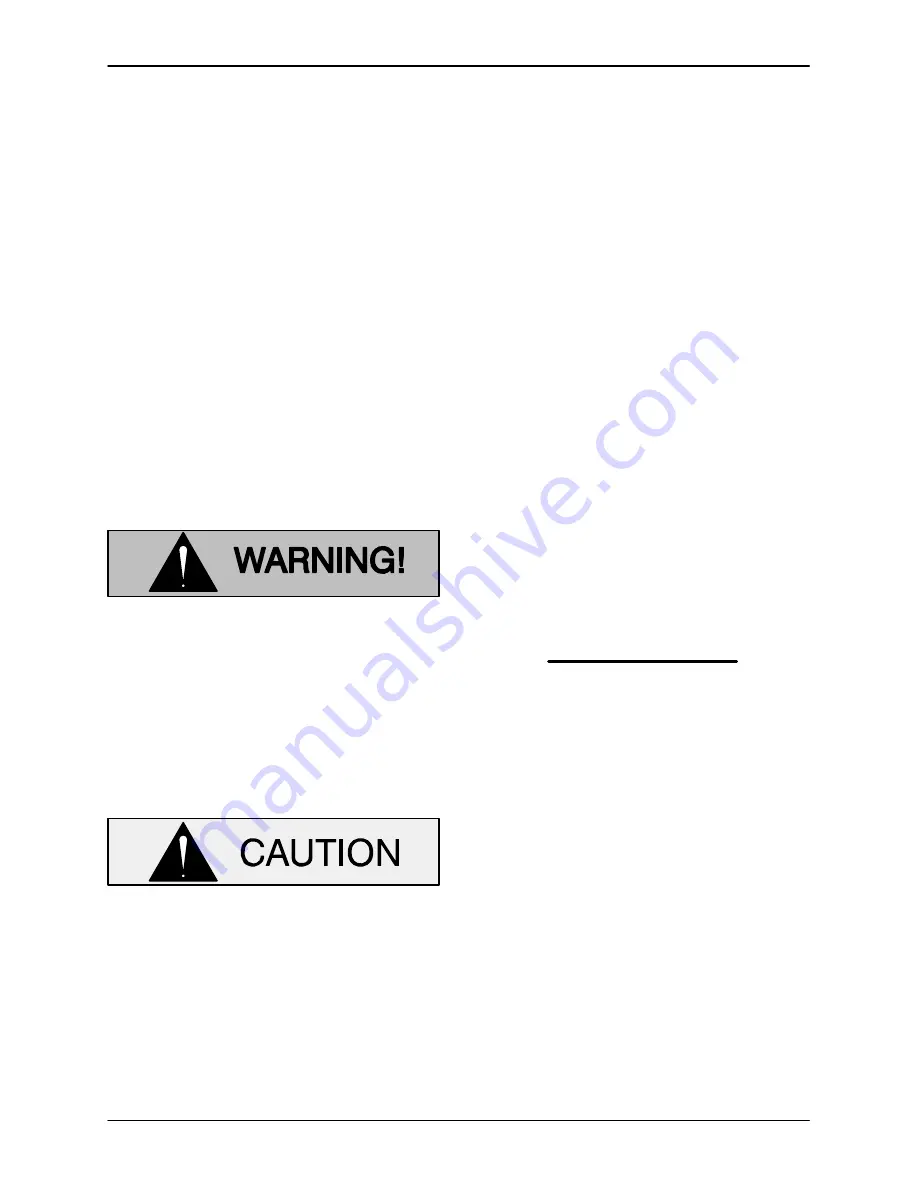
OM-05450
GHS SERIES
PAGE F - 19
SEAL APPENDIX
Seal Removal
(Figures E‐1 and F‐7)
See
PUMP DISASSEMBLY
and remove the
Rotor
Adjusting Sleeve (07)
.
Remove the hardware (B, D and K) securing the
cartridge seal assembly (05) to the backhead
(06A). Loosen the allen head setscrews securing
the rotating portion of the seal to the shaft.
Reach through the opening in the backhead and
pull the cartridge seal off the shaft.
Seal Installation
(Figures E‐1 and F‐7)
See
Pump Reassembly, Section E
, and as
semble the housing assembly (04), backhead kit
(06) and rotor/shaft assembly (03).
Clean the seal cavity and shaft with a cloth soaked
in fresh cleaning solvent.
Most cleaning solvents are toxic and
flammable. Use them only in a well ven
tilated area free from flame, sparks, and
excessive heat. Read and follow all pre
cautions printed on solvent containers.
In many cases it may not be necessary to replace
the entire cartrdige seal assembly when the seal
fails. Seal re‐build kits are available from the seal
manufacturers; consult the factory.
Seal components
must
be kept clean.
Handle seal parts with extreme caution to
prevent damage. Use care not to contami
nate the precision‐finished faces; even fin
gerprints on the faces can shorten seal life.
If necessary to clean the faces, use a clean
cloth and wipe in a circular pattern.
Inspect the seal components for wear, scoring,
grooves, and other damage that might cause leak
age.
If a replacement seal is being used, unwrap the
mechanical seal components.
Lightly lubricate the seal area of the shaft using a
soft hand soap and water solution, glycerine or sili
cone grease.
Do not use petroleum based lubri
cants.
Slide the cartridge seal assembly onto the shaft un
til the seal gland plate is fully seated against the
backhead. A pusher tube may be used to evenly
force the seal into position. Rotate the seal until the
seal ports are in a suitable position for equipment
piping.
Assemble the rotor adjusting sleeve (07) and ad
just the end clearance as described in
Pump Re
assembly, Section E
. The end clearance must be
set before completing the seal installation.
Install the hardware (B, D and K) and lightly snug
the gland to the face of the seal chamber. Tighten
the gland nuts evenly in a cross pattern, two flats at
a time, to the torque values shown in Table E‐1 for
the size of the gland hardware.
NOTE
The gland hardware must be tightened equally to
prevent seal misalignment
before tightening the
seal setscrews
.
Due to variations in seal design from the manufac
turers, some seals may be equipped with center
ing/alignment clips and others may not. If the seal
has centering/alignment clips, turn the clips 90
to
the shaft and check to ensure absolute centering
on the drive collar (consult the literature provided
with the seal for additional instructions).
Turn each of the seal setscrews until the tip of each
setscrew just touches the shaft. After the set
screws all touch the shaft, tighten the setscrews
until the points of the setscrews are embedded in
the shaft. This should keep the seal centered on
the shaft. Follow setscrew torque values as de
scribed in the literature provided with the seal.
If so equipped, ensure that the centering/align
ment clips are positioned 90
to the shaft. Rotate
the shaft by hand to ensure that the drive collar is
not rubbing or binding against any of the clips.
If adjustment is required, loosen the gland nuts
and move the gland slightly to achieve centering,