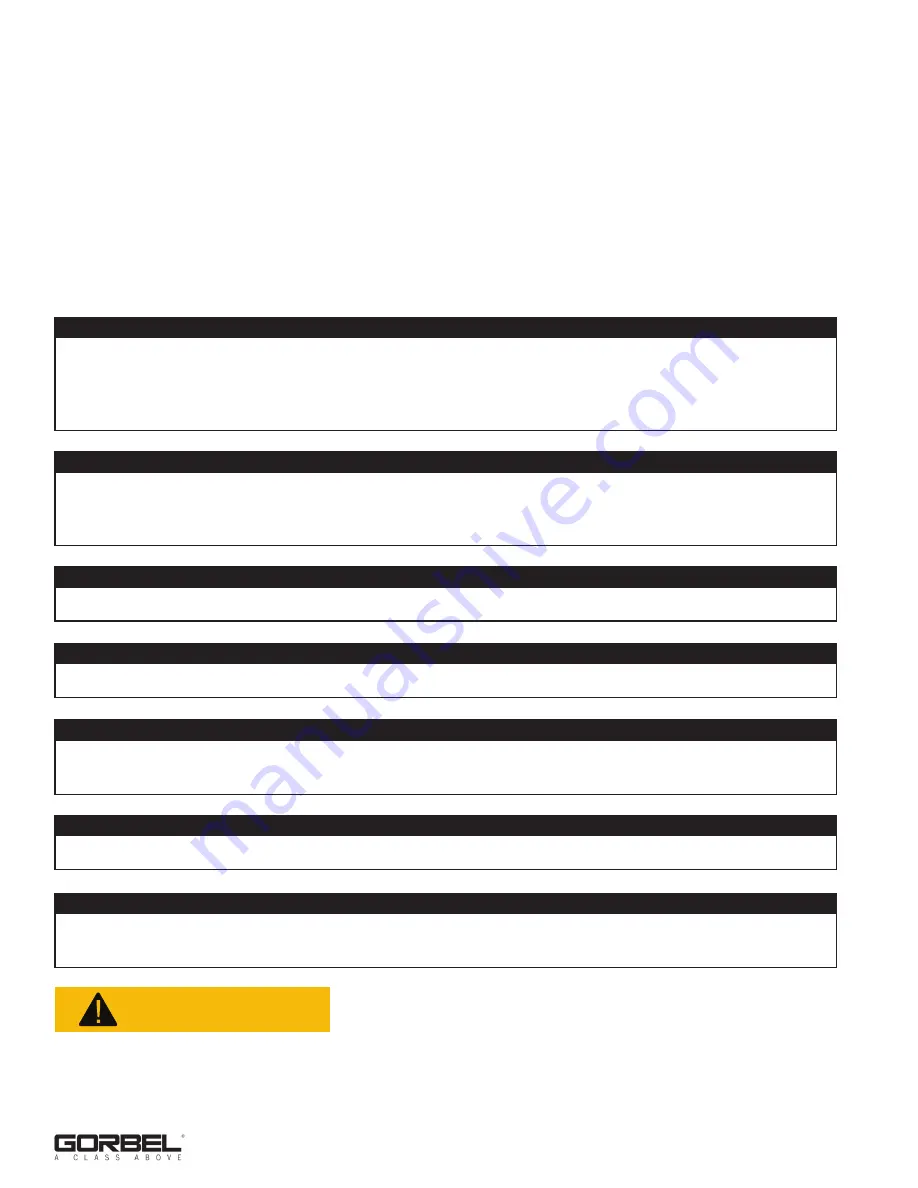
INTRODUCTION
Thank you for choosing a Gorbel® G-Force® Intelligent Lifting Device (ILD)** to solve your material han-
dling needs. The G-Force® is a servomotor driven, high speed, ergonomic materials handling device. The
innovative design and heavy-duty construction of the G-Force® will provide a superior quality product that
will offer years of long term value. A Gorbel® G-Force® will provide many years of dependable service by
following the installation and maintenance procedures described herein.
** U.S. Patent No’s: 5,865,426, 6,622,990, 6,386,513, & 6,886,812, Other Patents Pending
Dimensions contained in this installation manual are for reference only and may differ for your
particular application.
WARNING
Only competent erection personnel familiar with standard fabrication practices should be employed to
install the G-Force® because of the necessity of properly interpreting these instructions. Gorbel is not
responsible for the quality of workmanship employed in the installation of this hoist according to these
instructions. Contact Gorbel, Inc., at 600 Fishers Run, P.O. Box 593, Fishers, New York 14453, 1-585-
924-6262, for additional information if necessary.
WARNING
Equipment described herein is not designed for, and should not be used for, lifting, supporting, or trans-
porting humans. Failure to comply with any one of the limitations noted herein can result in serious bodily
injury and/or property damage. Check Federal, State and Local regulations for any additional require-
ments.
WARNING
Prior to installation, consult a qualified structural engineer to determine if your support structure is ade-
quate to support the loadings created during normal operation of the G-Force®.
WARNING
Reference American Institute of Steel Construction (AISC) Manual of Steel Construction (9th edition), Part
5, Specification for Structural Joints using ASTM A325 or A490 Bolts (section 8.d.2) for proper procedure
to follow when using any torque tightening methods.
WARNING
Do not field modify the G-Force® actuator or handles in any way. Any modification, without the written
consent of Gorbel, Inc., will void warranty.
WARNING
The jog switch buttons are for system maintenance and load testing only, and should not be manipulated
during normal operation of the G-Force®. Operation of the jog switch buttons during normal operation
increases the risk of personal injury to the operator.
4
9/18 - Rev. U
WARNING
Gorbel Inc. authorizes use of wire rope only as supplied by Gorbel for any G-Force® equipment. Use of
other than Gorbel supplied wire rope shall void Gorbel’s warranty of the product.
WARNING
This product can expose you to chemicals, including acrylonitrile,
which are known to the State of California to cause cancer. For
more information go to:
www.P65Warnings.ca.gov