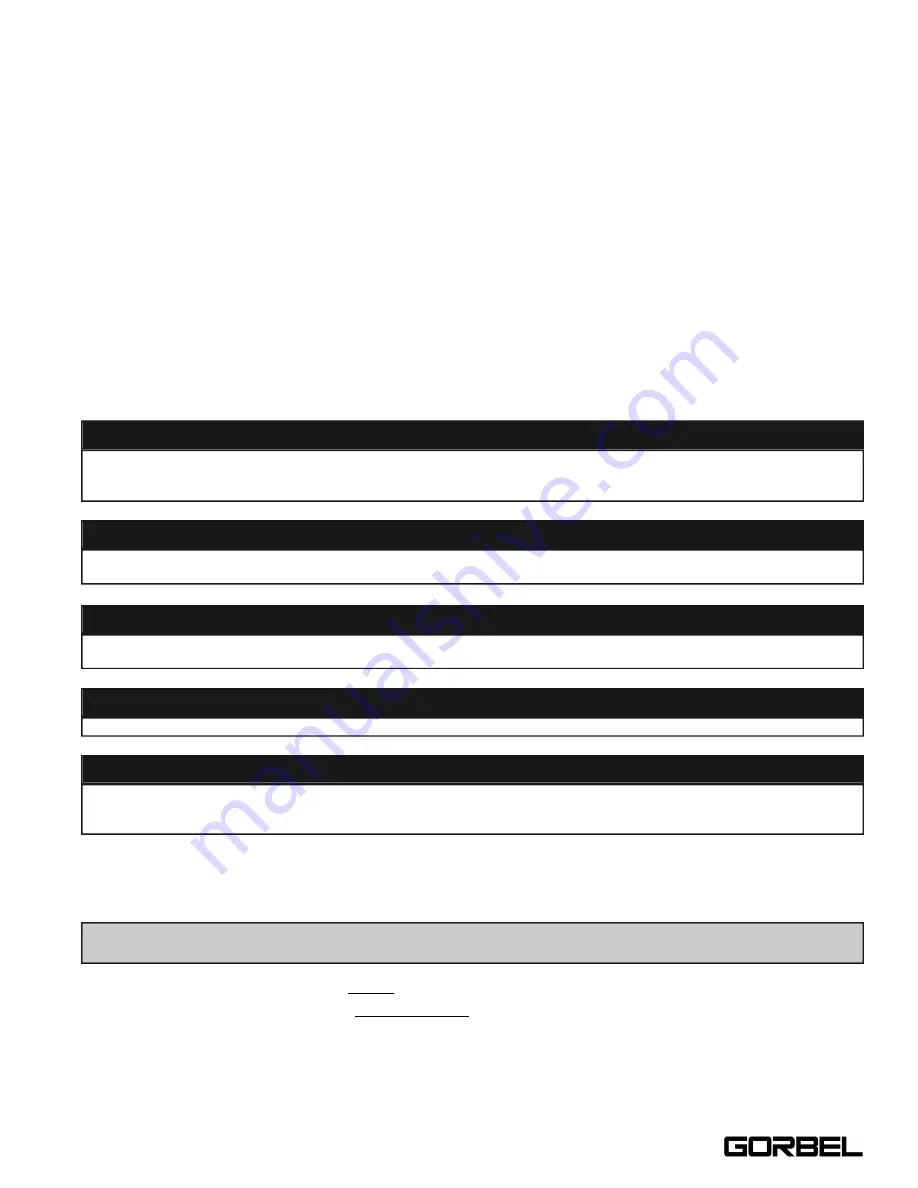
INTRODUCTION
Thank you for choosing Gorbel Ceiling Mounted Work Station Cranes to solve your material handling needs. The
innovative design and heavy-duty construction of the Gorbel Work Station Cranes will provide a superior quality
product that will offer years of long term value. All Gorbel cranes are pre-engineered for powered hoist operation.
The hoist weight allowance is 15% of the crane’s capacity (for example, a crane rated for 1000 pounds, allows for a
1000-pound live load plus 150 pounds for the weight of the hoist). There is also an allowance of 25% of the crane
capacity for impact caused by hoist use. Gorbel Work Station Cranes will provide many years of dependable
service by following the installation and maintenance procedures described herein.
Dimensions contained in this installation manual are for reference only and may differ for your particular
application. Please refer to the enclosed General Arrangement Drawing for actual dimensions.
Normal safety precautions:
These include, but are not limited to:
•
Checking for obstructions in crane travel
•
Checking that all bolts and threaded rods are tight and have lockwashers
•
Making sure that end stops are in place
•
Making sure that festooning cannot be snagged or pinched, whether it is electric or pneumatic
For additional safety precautions, see page 24.
INSTALLATION
STEP 1 - PRE-ASSEMBLY
1.1
Read entire installation manual
before
you begin installing your crane.
1.2
Check packing list to make sure
correct quantity
of parts is included.
1.3
Tools and materials typically needed to assemble crane are as follows:
• Hand tools
• Powered metal-cutting saw
• Leveling tools
• Steel shims (for flush mounted hangers)
• Ladders/man lifts
• Torque wrench (able to torque up to 200-ft. lb.)
WARNING
Equipment described herein is not designed for, and should not be used for, lifting, supporting or transporting humans. Failure to
comply with any one of the limitations noted herein can result in serious bodily injury and/or property damage. Check State and
Local regulations for any additional requirements.
WARNING
Crane cannot be utilized as a ground: A separate ground wire is required. For example, systems with 3-phase power require
three conductors plus one ground wire.
WARNING
Before installing any crane system, it is critical you determine that your building will safely support the loads. Gorbel, Inc.
assumes no responsibility for adequacy or integrity of the mounting surface.
WARNING
Sway bracing is required (except when using flush mounted hangers). For more information see page 23.
WARNING
Reference the American Institute of Steel Construction (AISC) Manual of Steel Construction (9th edition), Part 5, Specification for
Structural Joints using ASTM A325 or A490 Bolts (section 8.d.2) for the proper procedures to follow when using any torque-
tightening method.
TIP:
Packing list can be found in plastic pocket attached to the hardware box: General Arrangement Drawing
and additional inserts can be found enclosed in this installation manual.
Æ
1
9/05
Summary of Contents for AL 1000
Page 1: ......