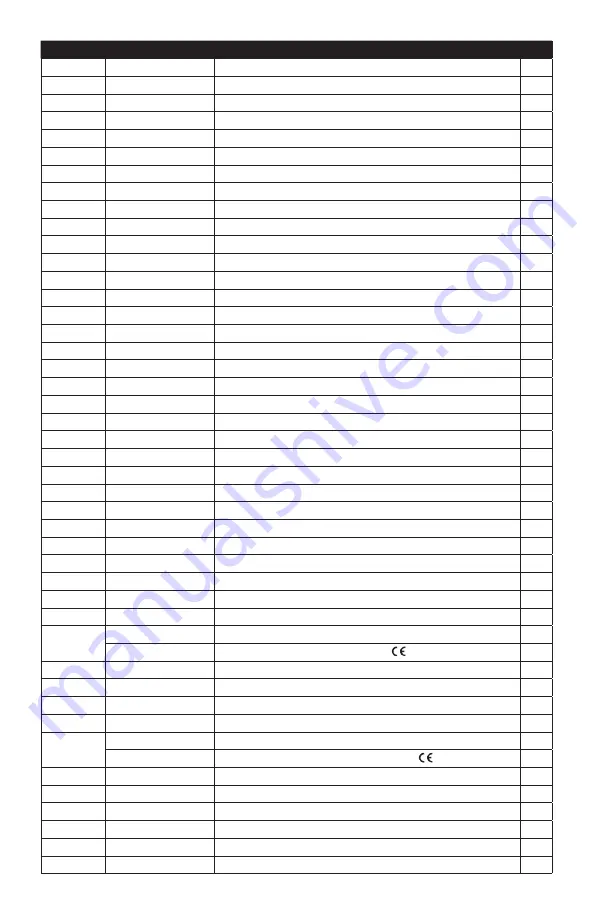
RAM PRO XL 0321
13
ITEM NO.
PART NUMBER
DESCRIPTION
QTY.
14
SQC-03
MANIFOLD, SQC, 823
1
15
SQC-07
LATCH, QC MANIFOLD
2
16
SQC-06
SPACER, SS, QC MANIFOLD
3
17
HWS-1024-163-SC
SCREW, 10-24, 1 5/8” L, SOCKET CAP
3
18
CD-CAP
CHEMICAL DISPENCE CAP
1
19
CD-HOUSING
CHEMICAL DISPENSING HOUSING
1
20
CD-CUP
CHEMICAL DISPENSER CUP
1
21
TUBEGUALD-XL-2
TUBE CLEANING TABLETS
2
22
R7-12
DC MOTOR DRIVE
1
23
X2-05-02
HANDLE, ROLL CAGE, X2
1
24
R7-11
WHEEL, R7
2
25
1718
VENT ELBOW, 1/8 NPT X 1/4 BARB
3
26
9008
FOOT
10
27
HWS-1016H
SCREW, #10-16 X 3/8” SLOTTED HEX HEAD
26
28
HWST-1037-P
SCREW, #10 X 1/2", PANHEAD
6
29
X2-14
GROMMET, BLIND, 3/8”
6
30
HWS-25-1SH
SCREW 1/4-20 X 1”, SOCKET HEAD
10
31
X2-05-03
STAR NUT, TUBE CONNECTOR
2
32
824
SEAL, WATER, 1” OD X 1/2" ID
1
33
825
BEARING, 1/2" X 1 1/8”
2
34
945
SPRING SPACER
1
35
826
SNAP RING
1
36
SQC-10
SPRING, TORSION, QC MANIFOLD
1
37
R7-13
MOTOR COUPLING, FLEXIBLE, 5/8 X 1/2
1
38
802
HOSE CONNECTOR
1
39
SBA-102
NOZZLE BUSHING
1
40
HWN50P
ROMEX NUT 1/2 NPT
1
41
917
CLOSE NIPPLE, 1/4 NPT
2
42
933
BARBED FITTING, 1/4 BARB X 1/4 NPT
1
43
820X
SOLENOID VALVE, 110V 50-60 Hz
1
44
823N
NUT, MANIFOLD
1
45
HWOR-417
O-RING, VITON, 4” OD X 1/4” WIDTH
1
46
842
GFCI, 115V
1
842A
GFCI 230V
1
47
834R-XL
FOOT SWITCH, TWO DIRECTIONAL
1
48
834R-1
PRESSURE SWITCH
2
49
8947
CONTROL KNOB
1
50
9646
CIRCUIT BREAKER, 15A
1
51
X2-10
LIGHT, GREEN, 120V
1
X2-10A
LIGHT, GREEN, 230 V
1
52
HWS-2520-125P
SCREW, 1/4-20 X 1-1/4", PHILLIPS PHMS
6
53
HWW050
WASHER, 1/2 FLAT
2
54
HWS-3150H
SCREW, 5/16-18 X 1/2", HEX HEAD
2
55
918
TEE, 1/4 FNPT
1
56
R7-15
ADAPTER, BRASS 1/2 FNPT X 1/4 MNPT
1
57
L210
LABEL, CONTROL PANEL
1