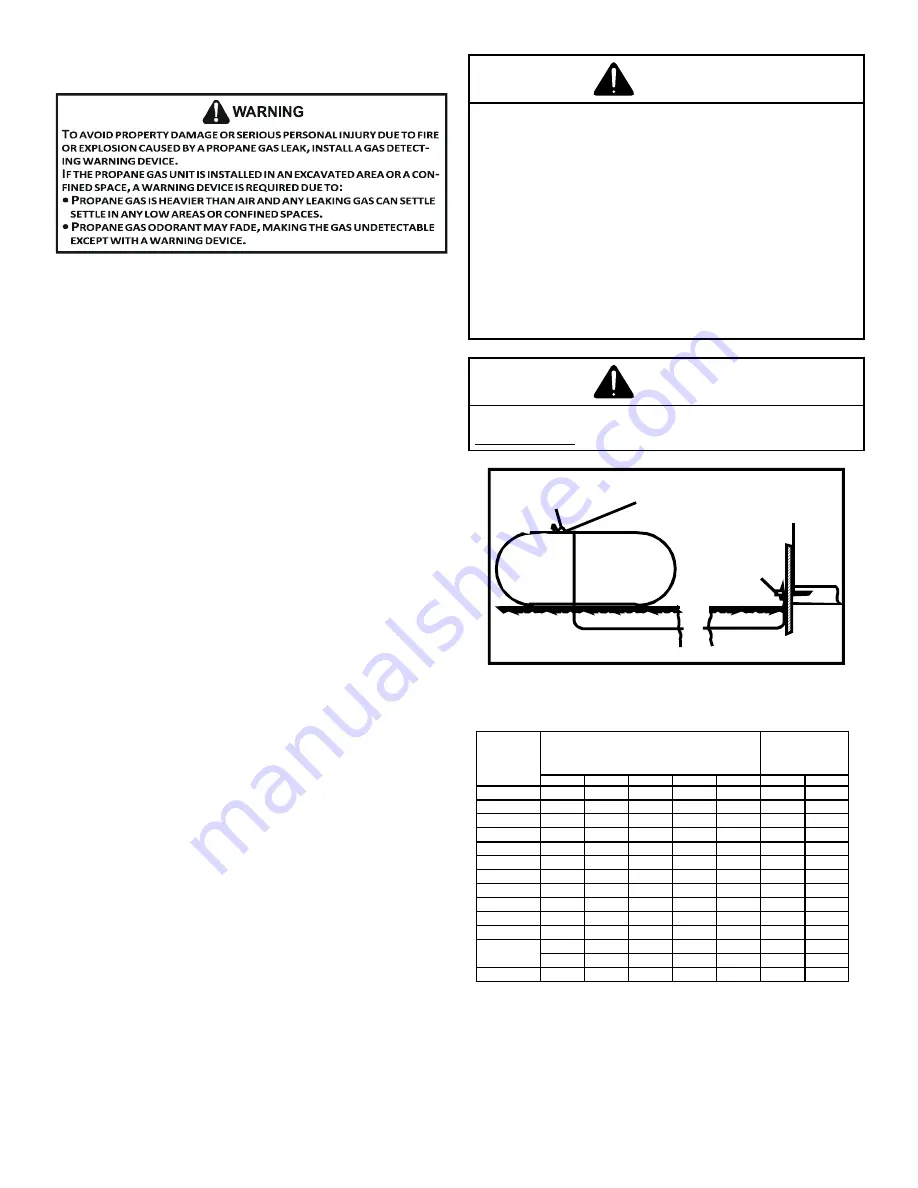
9
PROPANE GAS INSTALLATIONS
IMPORTANT NOTE:
For Natural gas to LP gas conversion,
Conversion Kit “LPM-08” must be used. Consult your dealer
for appropriate conversion kit(s).
All propane gas equipment must conform to the safety stan-
dards of the National Board of Fire Underwriters (See NBFU
Manual 58).
For satisfactory operation, propane gas supply pressure
must be within 9.7 - 10.3 inches W.C. at the manifold with all
gas appliances in operation. Maintaining proper gas pres-
sure depends on three main factors:
1.
Vaporization rate, which depends on (a) temperature of
the liquid, and (b) wetted surface area of the container
or containers.
2. Proper pressure regulation.
3. Pressure drop in lines between regulators, and be-
tween second stage regulator and the appliance. Pipe
size required will depend on length of pipe run and total
load of all appliances.
Tanks and Piping
Complete information regarding tank sizing for vaporization,
recommended regulator settings and pipe sizing is available
from most regulator manufacturers and propane gas suppliers.
Since propane gas will quickly dissolve white lead or most
standard commercial compounds, special pipe dope must
be used. Shellac base compounds resistant to the actions
of liquefied petroleum gases such as Gasolac®, Stalactic®,
Clyde’s® or John Crane® are satisfactory.
See Typical Propane Gas Piping figure for typical piping
arrangement.
CAUTION
To prevent property damage or personal injury due to fire,
the following instructions must be performed regarding gas
connections and pressure testing
•
The unit and its gas connections must be leak tested be-
fore placing in operation. Because of the danger of ex-
plosion or fire, never use a match or open flame to test
for leaks. Never exceed specified pressure for testing.
Higher pressure may damage gas valve and cause overfir-
ing which may result in premature heat exchanger failure.
•
This unit and its shut-off valve must be disconnected from
the gas supply during any pressure testing of that system
at pressures in excess of 1/2 PSIG (3.48 kPA).
•
This unit must be isolated from the gas supply system by
closing its manual shut-off valve during any pressure
testing of the gas supply piping system at test pressures
equal to or less than 1/2 PSIG (3.48 kPA).
WARNING
To avoid property damage or personal injury, be sure there is
NO OPEN FLAME in the vicinity during air bleeding.
200 PS
IG
Maximu
m
5 to 15 PS
IG
(20 PS
IG
Max.)
Continuous
11" W.C.
Second Stage
Regulator
First Stage
Regulator
Typical Propane Gas Piping
Sizing Between First and Second Stage Regulator
Maximum Propane Capacities listed are based on 1 PSIG Pressure Drop at 10
PSIG Setting. Capacities in 1,000 BTU/HR
3/8"
1/2"
5/8"
3/4"
7/8"
1/2"
3/4"
30
309
700
1,303
2,205
3,394
1,843
3,854
40
265
599
1,115
1,887
2,904
1,577
3,298
50
235
531
988
1,672
2,574
1,398
2,923
60
213
481
896
1,515
2,332
1,267
2,649
70
196
446
824
1,394
2,146
1,165
2,437
80
182
412
767
1,297
1,996
1,084
2,267
90
171
386
719
1,217
1,873
1,017
2,127
100
161
365
679
1,149
1,769
961
2,009
150
130
293
546
923
1,421
772
1,613
200
111
251
467
790
1,216
660
1,381
250
90
222
414
700
1,078
585
1,224
300
89
201
378
634
976
530
1,109
350
82
185
345
584
898
488
1,020
400
76
172
321
543
836
454
949
To convert to Capacities at 15 PSIG Settings -- Multiply by 1.130
To convert to Capacities at 5 PSIG Settings -- Multiply by 0.879
PIPE OR
TUBING
LENGTH,
FEET
NOMINAL PIPE SIZE,
SCHEDULE 40
TUBING SIZE, O.D., TYPE L