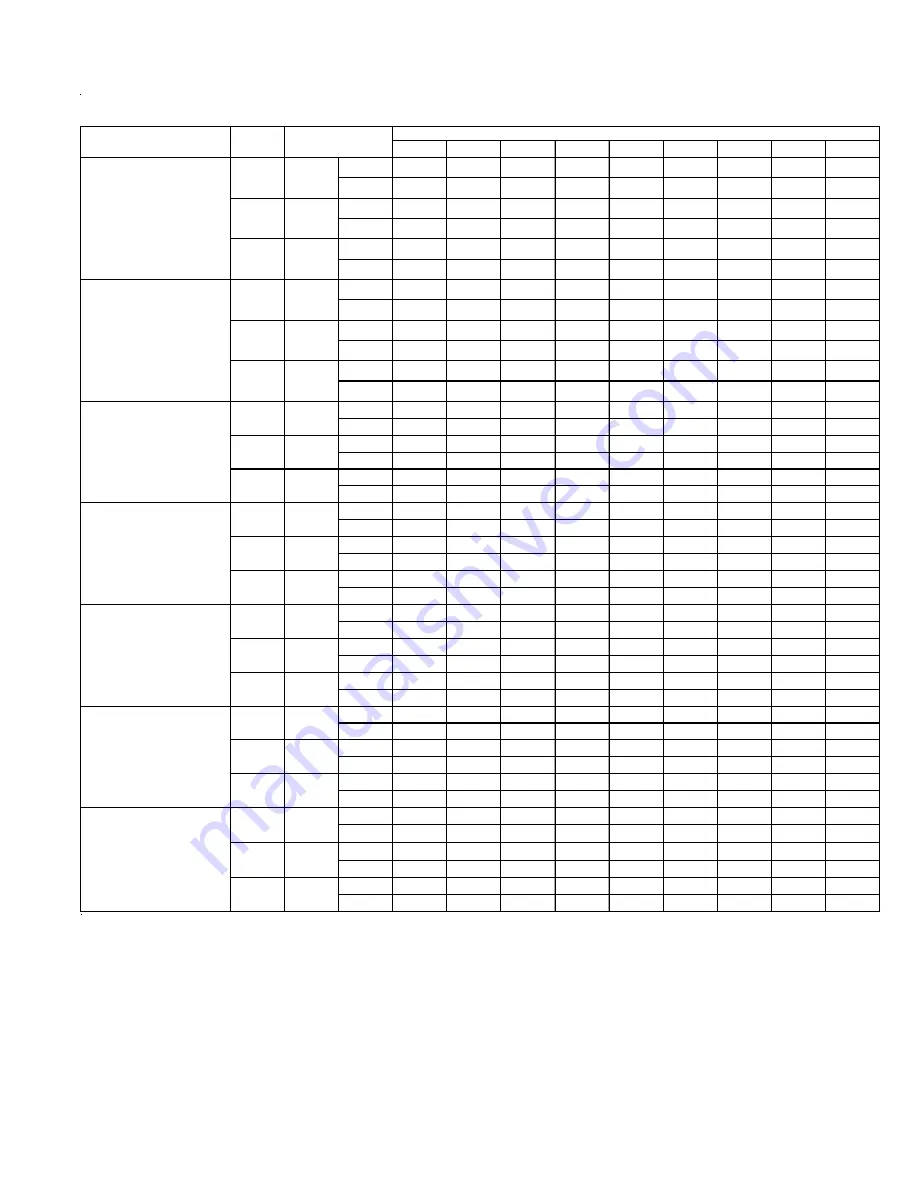
15
GPC15/GPH16[24-36]H41 BLOWER PERFORMANCE
0.1
0.2
0.3
0.4
0.5
0.6
0.7
0.8
0.9
CFM
1181
1146
1112
1062
1022
977
937
891
--
Watts
146
158
174
182
196
208
218
227
--
CFM
1410
1366
1328
1286
1248
1195
1155
1115
--
Watts
222
236
250
260
273
285
296
305
--
CFM
1637
1605
1561
1527
1484
1436
1390
1345
--
Watts
331
348
361
374
385
392
47
417
--
CFM
1165
1122
1080
1037
995
953
910
868
--
Watts
118
130
142
154
166
178
190
202
--
CFM
1365
1322
1280
1237
1195
1153
1110
1068
--
Watts
188
200
212
224
236
248
260
272
--
CFM
1645
1602
1560
1517
1475
1433
1390
1348
--
Watts
285
297
309
321
333
346
358
370
--
CFM
1057
939
839
745
657
570
497
--
--
Watts
128
134
148
162
168
180
192
--
--
CFM
1365
1322
1280
1237
1195
1153
1110
1068
--
Watts
188
200
212
224
236
248
260
272
--
CFM
1645
1602
1560
1517
1475
1433
1390
1348
--
Watts
285
297
309
321
333
346
358
370
--
CFM
1130
1080
1020
968
993
887
826
762
--
Watts
125
139
150
161
175
186
190
207
--
CFM
1712
1655
1587
1541
1486
1444
1393
1340
--
Watts
337
348
358
375
385
405
414
416
--
CFM
2002
1935
1885
1827
1767
1732
1669
1618
--
Watts
498
521
516
534
385
567
571
574
--
CFM
1130
1080
1020
968
993
887
826
762
--
Watts
125
139
150
161
175
186
190
207
--
CFM
1712
1655
1587
1541
1486
1444
1393
1340
--
Watts
337
348
358
375
385
405
414
416
--
CFM
2002
1935
1885
1827
1767
1732
1669
1618
--
Watts
498
521
516
534
551
567
571
574
--
CFM
1337
1297
1218
1155
1118
1088
1022
989
--
Watts
179
190
203
210
225
243
249
268
--
CFM
1694
1646
1598
1549
1501
1453
1405
1357
--
Watts
296
303
311
319
327
334
342
350
--
CFM
1919
1870
1822
1774
1726
1678
1629
1581
--
Watts
449
457
465
472
480
488
496
503
--
CFM
1451
1375
1321
1286
1233
1191
1108
1083
1034
Watts
216
224
230
240
248
262
266
288
294
CFM
1913
1834
1762
1698
1670
1619
1567
1531
1469
Watts
408
418
432
438
446
454
456
476
484
CFM
2049
1948
1914
1851
1811
1770
1738
1685
1641
Watts
506
522
528
548
544
548
556
568
578
G
P
H
1
6
42H
41
B
*
T1
230
T2 / T3
230
T4 / T5
230
E.S.P. (In. of H
2
O)
GP
H
166
0H
41
**
T1
230
T2 / T3
230
T4 / T5
230
T2 / T3
230
G
P
C
1
54
2H41
**
T4 / T5
230
Model
Speed
Volts
GP
H
1
64
2H41
A
*
T1
230
G
P
C
1
54
8H41
**
T1
230
T2 / T3
230
T4 / T5
230
G
P
H
164
8H
41
**
T1
230
T2 / T3
230
T4 / T5
230
G
P
C
156
0H
41
**
T1
230
T2 / T3
230
T4 / T5
230
T1
230
T2 / T3
230
T4 / T5
230
NOTES:
1. Data show n is dry coil. Wet coil pressure drop is approx.
2. Data show n does not include filter pressure drop, approx. 0.08” H2O.
3. Reduce airflow by 2% for 208V operation.
4. For high static applications, see blow er performance table above for selecting appropriate speed tap.