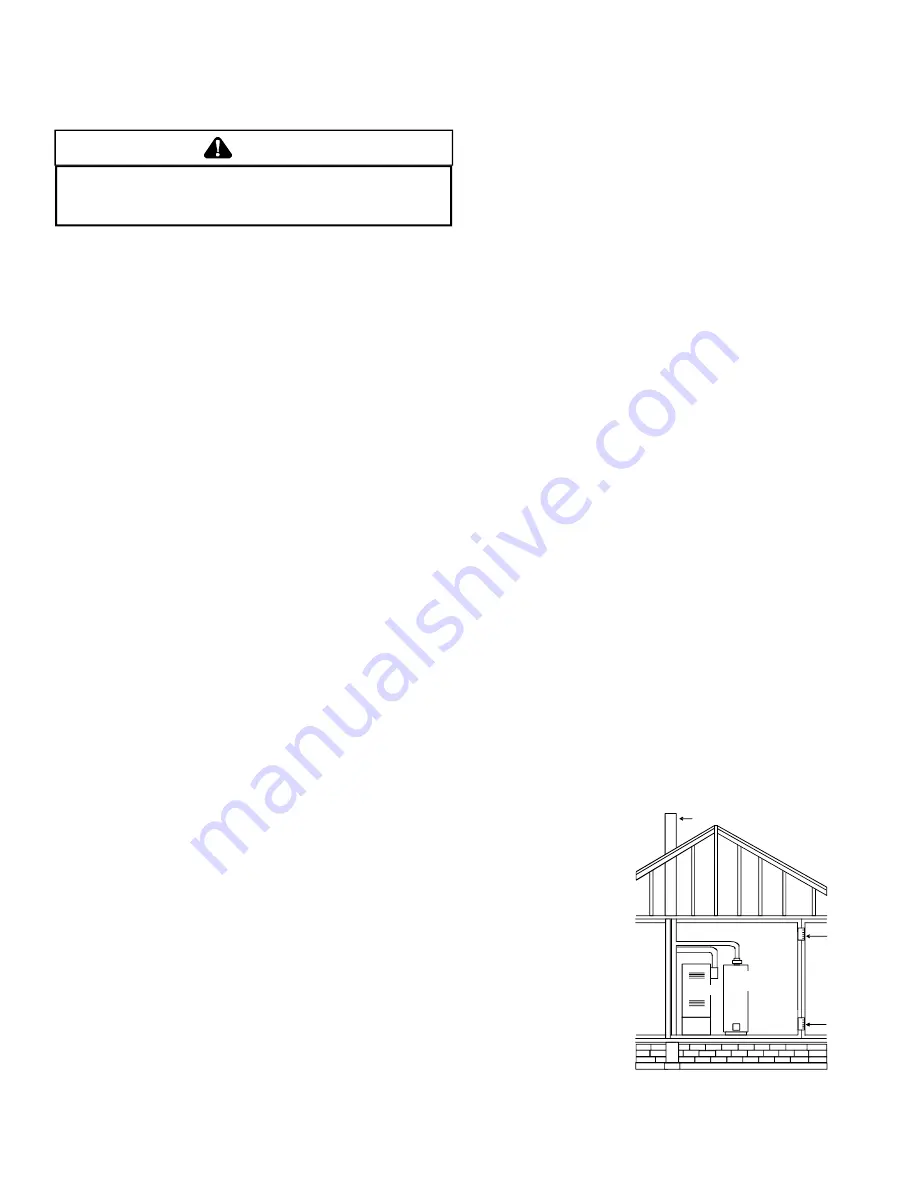
8
IO-247A
12/04
safety exhaust, odor control, and air for compressors.
(d) In addition to air needed for combustion, air shall be supplied
for ventilation, including all air required for comfort and
proper working conditions for personnel.
(e) While all forms of building construction cannot be covered
in detail, air for combustion, ventilation and dilution of flue
gases for gas utilization equipment vented by natural draft
normally may be obtained by application of one of the
methods covered in 5.3.3 and 5.3.4.
(f) Air requirements for the operation of exhaust fans, kitchen
ventilation systems, clothes dryers, and fireplaces shall be
considered in determining the adequacy of a space to
provide combustion air requirements.
5.3.2 Equipment Located in Unconfined Spaces:
In unconfined spaces (see definition below) in buildings,
infiltration may be adequate to provide air for combustion
ventilation and dilution of flue gases. However, in buildings
of tight construction (for example, weather stripping, heavily
insulated, caulked, vapor barrier, etc.), additional air may
need to be provided using the methods described in 5.3.3-
b or 5.3.4.
Space, Unconfined.
For purposes of this Code, a space whose volume is not
less than 50 cubic feet per 1,000 BTU per hour of the
aggregate input rating of all appliances installed in that
space. Rooms communicating directly with the space in
which the appliances are installed through openings not
furnished with doors, are considered a part of the unconfined
space.
5.3.3 Equipment Located in Confined Spaces:
(a)
All Air from Inside the Building:
The confined space shall be
provided with two permanent openings communicating
directly with an additional room(s) of sufficient volume so
that the combined volume of all spaces meets the criteria
for an unconfined space. The total input of all gas utilization
equipment installed in the combined space shall be
considered in making this determination. Each opening shall
have a minimum free area of 1 square inch per 1,000 BTU
per hour of the total input rating of all gas utilization
equipment in the confined space, but not less than 100
square inches. One opening shall be within 12 inches of the
top and one within 12 inches of the bottom of the enclosure.
Furnace
Water
Heater
Opening
Chimney or Gas Vent
Opening
NOTE: Each opening must have
a free area of not less than one
square inch per 1000 BTU of
the total input rating of all equip-
ment in the enclosure, but not
less than 100 square inches.
Equipment Located in Confined Spaces;
All Air from Inside Building. See 5.3.3-a.
Consult the instructions packaged with the thermostat for mounting
instructions and further precautions.
V. COMBUSTION AND VENTILATION AIR REQUIREMENTS
W A R N IN G
T
O A V O ID P R O P E R T Y D A M A G E , P E R S O N A L IN J U R Y O R D E A T H , S U F F IC IE N T
F R E S H A IR F O R P R O P E R C O M B U S T IO N A N D V E NT IL A T IO N O F F L U E G AS E S M U S T
B E S U P P L IE D .
M
O S T H O M E S R E Q U IR E O U T S ID E A IR B E S U P P L IE D IN T O T HE
F U R N A CE A RE A .
Improved construction and additional insulation in buildings have
reduced heat loss by reducing air infiltration and escape around
doors and windows. These changes have helped in reducing
heating/cooling costs but have created a problem supplying
combustion and ventilation air for gas fired and other fuel burning
appliances. Appliances that pull air out of the house (clothes dryers,
exhaust fans, fireplaces, etc.) increase the problem by starving
appliances for air.
House depressurization can cause back drafting or improper
combustion of gas-fired appliances, thereby exposing building
occupants to gas combustion products that could include carbon
monoxide.
If this furnace is to be installed in the same space with other gas
appliances, such as a water heater, ensure there is an adequate
supply of combustion and ventilation air for the other appliances.
Refer to the latest edition of the National Fuel Gas Code NFPA 54/
ANSI Z223.1 (Section 5.3), or CAN/CSA B149 Installation Codes
(Sections 7.2, 7.3, or 7.4), or applicable provisions of the local
building codes for determining the combustion air requirements for
the appliances.
This furnace must use indoor air for combustion. It cannot be
installed as a direct vent (i.e., sealed combustion) furnace.
Most homes will require outside air be supplied to the furnace area
by means of ventilation grilles or ducts connecting directly to the
outdoors or spaces open to the outdoors such as attics or crawl
spaces.
The following information on air for combustion and ventilation is
reproduced from the
National Fuel Gas Code NFPA 54/ANSI
Z223.1 Section 5.3.
5.3.1 General:
(a) The provisions of 5.3 apply to gas utilization equipment
installed in buildings and which require air for combustion,
ventilation and dilution of flue gases from within the building.
They do not apply to (1) direct vent equipment which is
constructed and installed so that all air for combustion is
obtained from the outside atmosphere and all flue gases are
discharged to the outside atmosphere, or (2) enclosed
furnaces which incorporate an integral total enclosure and
use only outside air for combustion and dilution of flue gases.
(b) Equipment shall be installed in a location in which the facilities
for ventilation permit satisfactory combustion of gas, proper
venting and the maintenance of ambient temperature at safe
limits under normal conditions of use. Equipment shall be
located so as not to interfere with proper circulation of air.
When normal infiltration does not provide the necessary air,
outside air shall be introduced.
(c) In addition to air needed for combustion, process air shall
be provided as required for: cooling of equipment or material,
controlling dew point, heating, drying, oxidation or dilution,