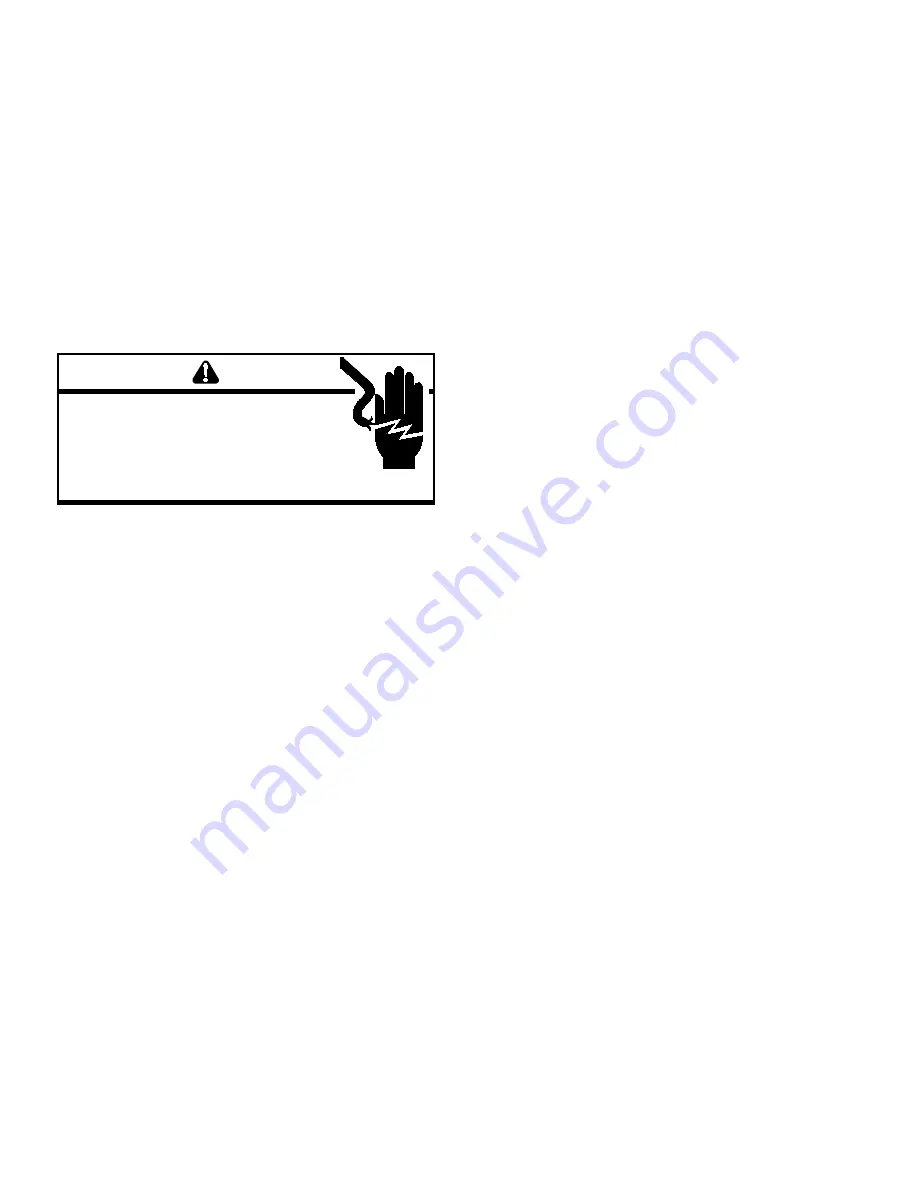
SCHEDULED MAINTENANCE
39
CONDENSATE DRAINAGE SYSTEM (QUALIFIED
SERVICER ONLY)
The drain tubes, trap, and field supplied drain line must be
checked annually and cleaned as often as necessary to
ensure proper condensate drainage.
FLAME SENSOR (QUALIFIED SERVICER ONLY)
Under some conditions, the fuel or air supply can create a
nearly invisible coating on the flame sensor. This coating acts
as an insulator, causing a drop in the flame sensing signal. If
this occurs, a qualified servicer must carefully clean the flame
sensor with steel wool. After cleaning, the flame sensor output
should be as listed on the specification sheet.
BURNERS
WARNING
HIGH
VOLTAG
E
E
L
EC
T
R
I
C
AL
C
OMPON
E
NTS
A
RE C
ONTAIN
E
D
IN
BOTH
C
OMPA
R
TM
E
NTS
.
T
O
AVOID
E
L
EC
T
R
I
C
AL
SHO
CK
,
IN
J
U
R
Y
O
R
D
E
ATH,
DO
NOT
RE
MOV
E
ANY
INT
ER
NAL
C
OMPA
R
TM
E
NT
C
OV
ER
S
O
R
ATT
E
MPT
ANY
AD
J
USTM
E
NT
.
C
ONTA
C
T
A
Q
UALIFI
E
D
S
ER
VI
CE
AG
E
NT
AT
ON
CE
IF
AN
ABNO
R
MAL
FLAM
E
APP
E
A
R
AN
CE
SHOULD
D
E
V
E
LOP
.
Periodically during the heating season make a visual check of
the burner flames. Turn the furnace on at the thermostat. Wait
a few minutes since any dislodged dust will alter the normal
flame appearance. Flames should be stable, quiet, soft and
blue with slightly orange tips. They should not be yellow. They
should extend directly outward from the burner ports without
curling downward, floating or lifting off the ports.
HEATING PERFORMANCE TEST
Before attempting to diagnose an operating fault code, run
a Heating Performance Test to determine if the heating
system is performing within 5% of the BTU input found on
the rating plate of the unit being tested. To conduct a heating
performance test, the BTU input to the unit must be calculated
(see Clocking a Gas Meter). Before clocking a gas meter,
contact your local utility to provide the caloric value (BTU
content) of the natural gas in the area.
It is also important to confirm the airflow (CFM) is within the
temperature rise range (see Airflow Data in spec sheet) and
external static pressure range (approximately 0.5” water
column). How-to instructions can be found in the service
manual under Checking External Static Pressure and
Checking Temperature Rise.