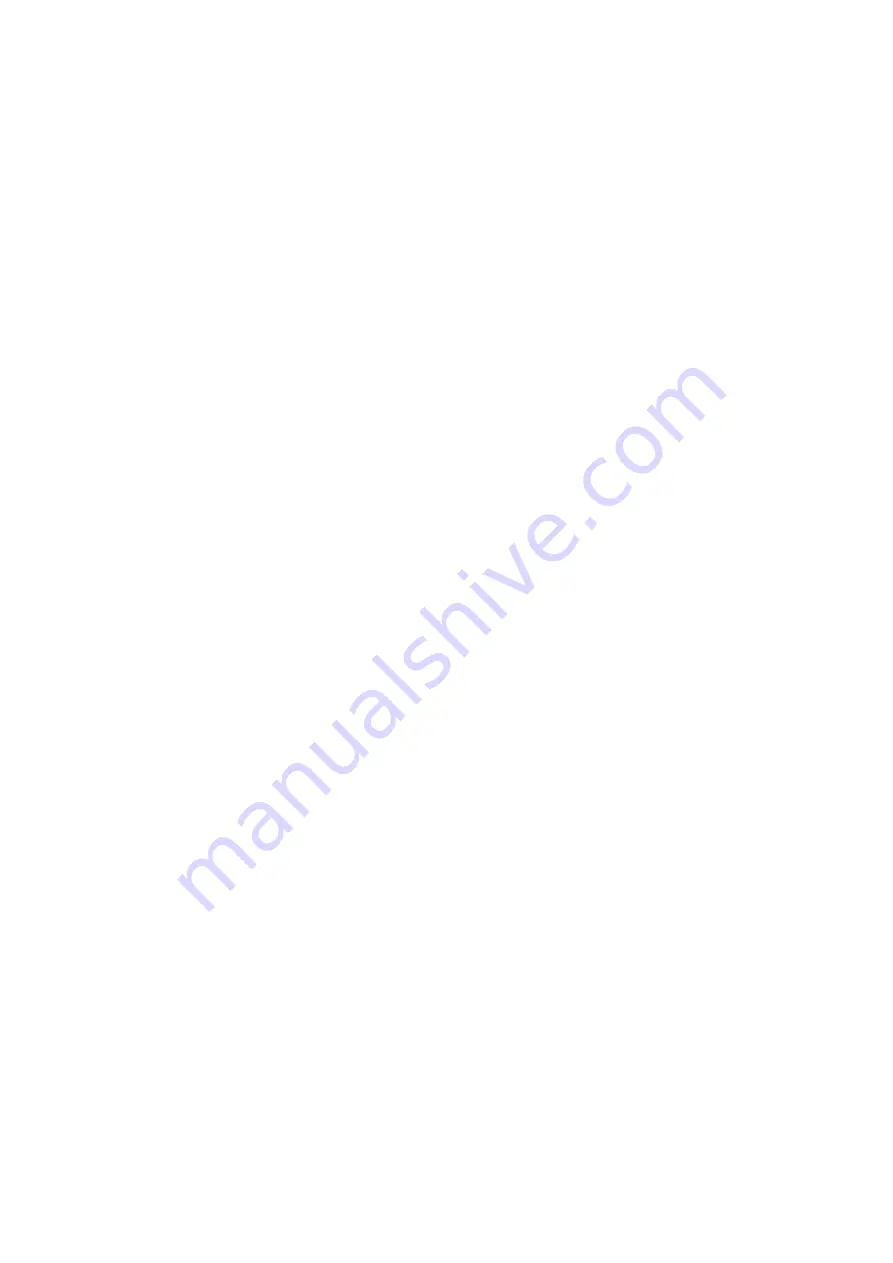
3
Operation
06
For correct function the printer must have a label design downloaded and set in "Applicator"
mode. Also make sure that the applicator arm 5 is in a correct position and roller no. 3 presses
firm enough on the product without slowing it down when passing by.
The next step is to adjust the applicator to the label length and bring the first printed label into
application position underneath the fan unit and pinch roller 3.
As soon as the product on the conveyer is detected by the product sensor, the first label will
be applied, the next label will be dispensed and a third label will be printed. In order to
prevent multiple triggering of the product sensor for the same product, the Block Delay
potentiometer can be adjusted to block sensor activations for a period after the initial trigger
therefore avoiding more than one label being applied to a product.
By changing the horizontal position of the product sensor you will be able to adjust the label
position on the product.
4
Adjusting the applicator and ventilator unit
Setting of label length
The label length is set by moving roller 1 along the applicator bracket 2. The roller should be
set to a position such that the gap between the labels stops 5-20mm from the dispensing
edge after print or after pressing the FEED button on the printer. The shorter the label, the
closer the gap needs to be to the dispensing edge.
Setting of ventilator unit
The fan unit 4 can be moved up and down applicator arm 5. It should be set to a position
such that the leading edge of the label is just underneath the foam rubber pinch roller 3.
The roller itself can also be tuned vertically and horizontally to obtain a perfect position and
pressure. By regulating the power with knob 6 it is possible to compensate for differences in
label weight, stiffness and memory effect.