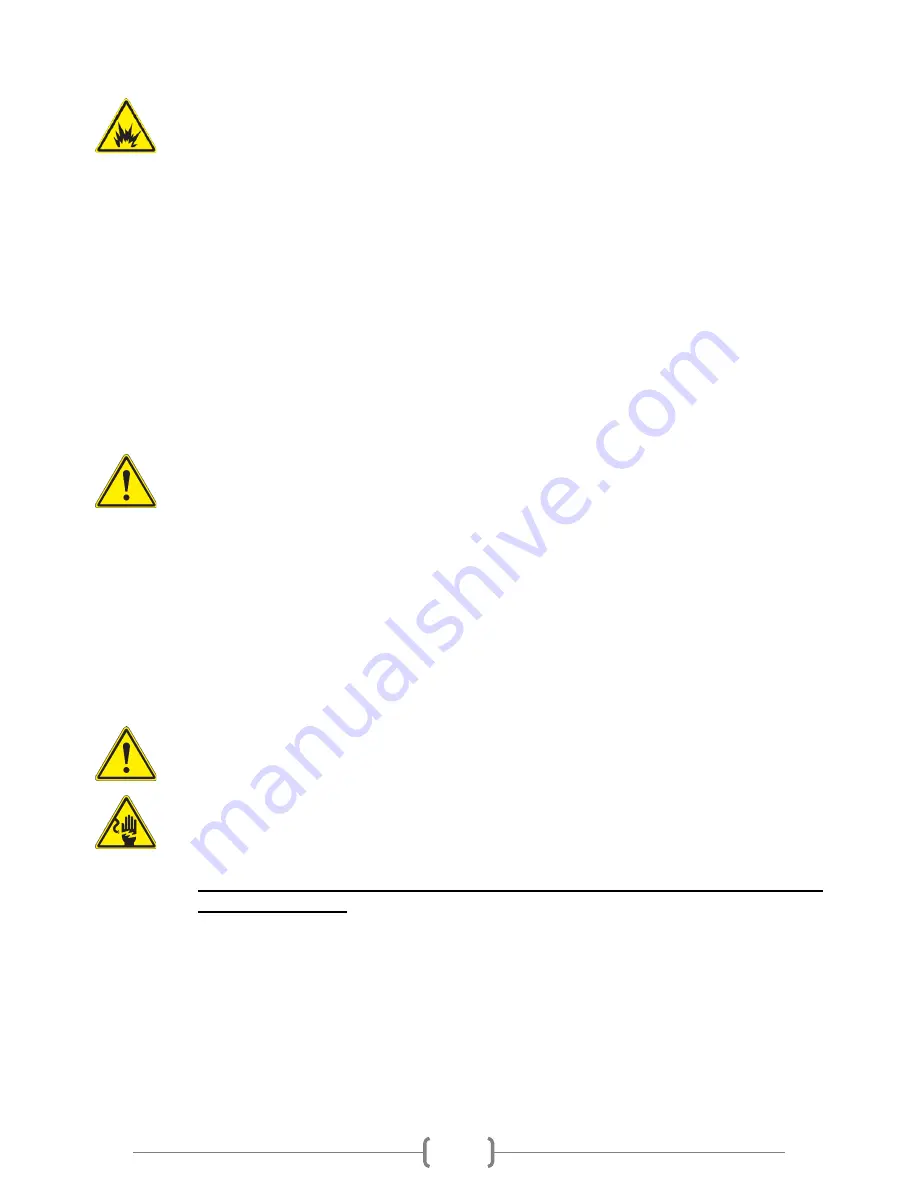
16
4.6
Magnet Power Connections
Never connect or remove cables from the magnet with the power supply energized.
The stored energy in the magnet can cause arcing resulting in severe injury or
equipment damage.
Follow the lockout/tagout procedure as described in Section 1, Lockout/Tagout prior
to connecting or removing the DC power cables.
The magnet is shipped with a power and interlock cable attached. The recommended current cable
for the 5203 is shown in Drawing 16907-0116-1-S1_A (section 12). Because the magnet stores a
significant amount of energy in its magnetic field, special care should be taken to ensure that the
current terminations are secure and cannot work loose in operation. Local heating at the
terminations can cause rapid oxidation leading to a high contact resistance and high power
dissipation at the terminals. If left unattended this can cause enough local heating to damage the
terminals and the coils.
4.7
5203 Interlocks
In the event of an interlock tripping it is strongly recommended that the root cause of
the trip be determined. In the event that the root cause cannot be determined please
contact Tom King ([email protected]) for technical support.
The Model 5203 has one Selco UP62-080C thermostat. It is located between the base yoke plate and
the lower cooling plate. The thermostat is normally closed, opening when the coil heatsink
temperature exceeds 80°C, ± 5°C.
The interlock circuit also includes a flow switch (GEMS FS-380) located at the junction box. This
flow switch is open for flow rates above 5.4 lpm (1.5 US gpm).
4.8
Interlock Testing
It is crucial that before general operation of the magnet system, that the interlock
circuits be tested. This test requires that the terminal cover be removed from the
magnet while energized and therefore must be completed by a qualified electrician.
This test should be done with the magnet operating with a LOW power setting,
preferably less than 5 amps.
DO NOT AT ANY POINT TOUCH OR DISCONNECT THE MAGNET
POWER CABLES.
Thermal Switches
: Carefully remove one of the temperature switch connections from the interlock
termination block. The power supply output MUST enter a disabled state. Reconnect the
connection and the power supply output should return to normal.
Flow Switch
: Shut off the water supply to the magnet. The power supply output MUST enter a
disabled state. Restore the water supply and the power supply output should return to normal.
This interlock testing procedure should be carried out no less than every six months.
Summary of Contents for 5203
Page 2: ...Blank Page ...
Page 11: ...9 2 3 11907 0224 0 5203 General Assembly ...
Page 12: ...10 2 4 11907 0233 0 5203 Terminal Block Assembly ...
Page 13: ...11 2 5 17907 0412 0 5203 Mounting Plate ...
Page 24: ...22 9 EXCITATION CURVES AND FIELD UNIFORMITY Excitation Curves for the various pole types ...
Page 25: ...23 Excitation and Field Remanence for the standard pole Type A ...
Page 26: ...24 Near and far vertical field profiles for the standard pole Type A ...
Page 27: ...25 ...
Page 28: ...26 ...
Page 39: ...37 10 TEST DATA ...
Page 41: ...39 13907 0025 1 System Wiring 5203 1x BOP20 50 and PDU ...
Page 42: ...40 13907 0026 1 System Wiring 5203 2x BOP20 50 and PDU ...
Page 43: ...41 1C907 5203 08 Electrical Assembly 5203 and IECO BPS ...
Page 44: ...42 1D907 5203 08 Electrical Wiring 5203 and IECO BPS ...
Page 45: ...43 1C907 5203 09 Electrical Assembly 5203 IECO BPS and 5972 ...
Page 46: ...44 1D907 5203 09 Electrical Wiring 5203 IECO BPS and 5972 ...
Page 48: ...46 16907 0116 1 S1 Cable Current Interlock 5203 BOP20 50 and PDU ...
Page 49: ...47 16907 0116 3 S1 Cable Current Interlock 5203 IECO BPS and 5972 ...
Page 50: ...48 16907 0281 0 Cable Assembly Interlock Pigtail 5972 or IECO BPS ...
Page 51: ...49 11907 0620 0 GMW RC 1920 Equipment Rack ...