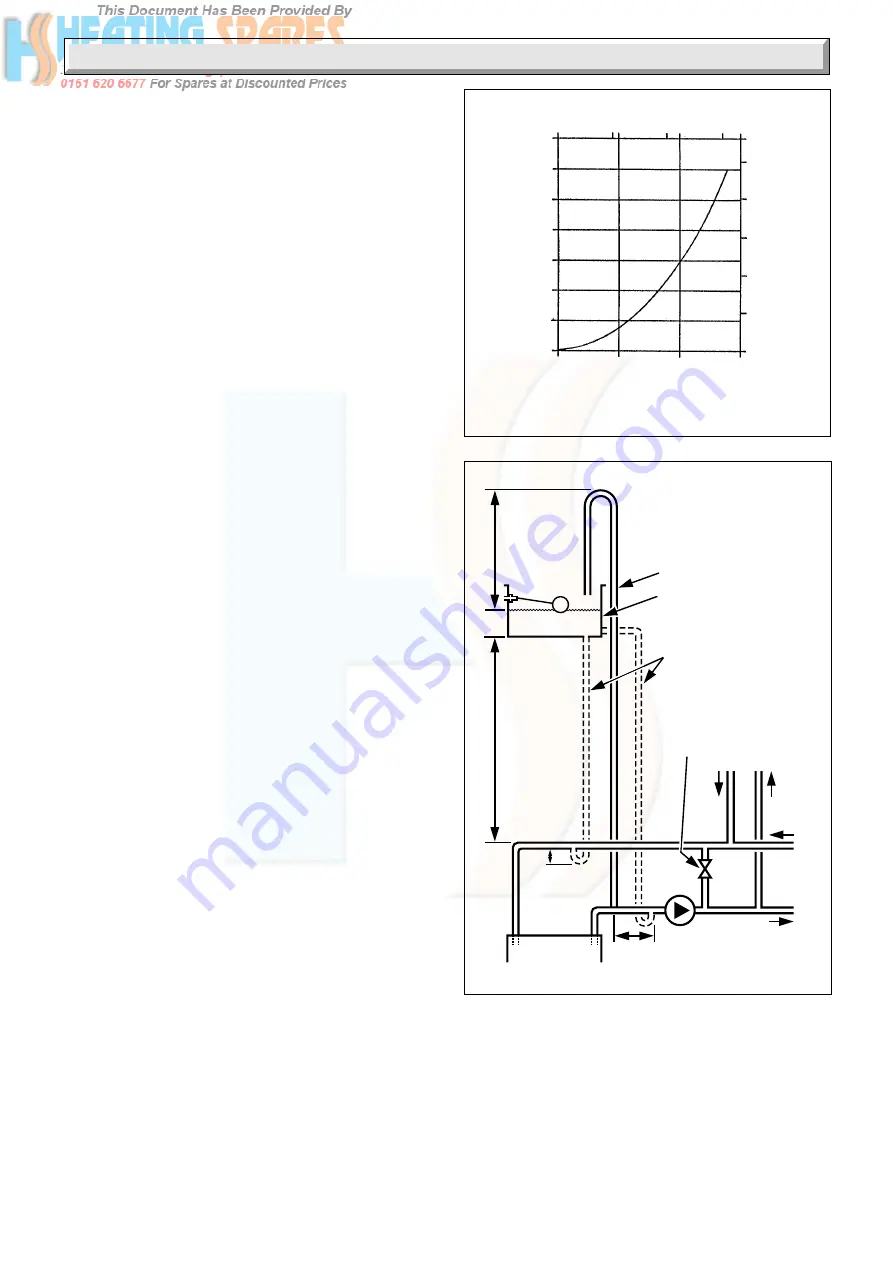
Supplied By www.heating spares.co Tel. 0161 620 6677
8
221481C
3 Water Systems
Notes:
PUMP
The pump should be fitted in the flow pipework from the boiler,
with valves each side, integral if possible, it should produce a
temperature difference across the boiler of 11
o
C (20
o
F).
Flow rates should be,
11.5 Litre/min (2.5gal/min)
See diagram 3.1 for pressure loss across the boiler.
High resistance microbore systems may require a higher duty
pump.
BYPASS
The flow through the boiler must not be allowed to fall below,
7.8 Litre/min (1.7gal/min) whilst the burner is alight.
A bypass must be fitted.
3.1 Open Vented Systems
Water system
For an open vented system the boiler must be supplied from an
unrestricted water supply taken from a feed and expansion
tank, situated at a maximum height of 27.5metres (90ft) above
the boiler.
The cold feed supply must be 15mm minimum size.
It is important that the relative positions of the pump, cold feed
and open vent are as shown in diagram 3.2.
3.2 Cylinder
SINGLE FEED SELF PRIMING CYLINDERS ARE NOT
RECOMMENDED.
The hot water cylinder must be a double feed fully indirect type.
3.3 Inhibitor
Attention is drawn to the current issue of BS5449 and BS7593
on the use of inhibitors in central heating systems.
If an inhibitor is to be used, contact a manufacturer for their
recommendations for the best product to use.
When fitting the boiler into an existing system take special care
to drain the entire system including the radiators, then thoroughly
cleaning out before fitting the boiler whether or not adding an
inhibitor.
Sealed Water Systems
The installation should comply with the appropriate requirements
of the current issue of BS4814, BS5449 BS6759 BS6798 and
BS7074 Part 1 and 2.
See diagram 3.3 for a suggested layout.
3.4 Safety Valve
A safety valve must be fitted to a sealed water system.
It shall be preset, nonadjustable with a lift pressure of 3bar,
incorporating seating of a resilient material, a test device and a
connection for drain.
The drain from the safety valve must be routed clear of any
electrical fittings and positioned so that any discharge can be
seen.
PRESSURE LOSS OF BOILER
ECONOMY
Diagram 3.1
2761
LITRES / MINUTE
GALLONS / MINUTE
(m head of water)
WATER PRESSURE LOSS
0
0.1
0.2
0.3
0.4
0.5
0.6
0.7
0
5
10
15
0
5
10
15
20
25
1
2
3
(m head of water)
WATER PRESSURE LOSS
Diagram 3.2
Open (vented) system.
Recommended
relationship between
pump, cold feed and
vent.
22 mm (MIN) VENT
FEED AND
EXPANSION
CISTERN
15mm (MINIMUM)
COLD FEED
15mm (MINIMUM)
BY-PASS WITH
LOCKSHIELD VALVE
450mm
MIN.
HEIGHT
1150mm
MIN.
150
mm
MIN.
BOILER
PUMP
150mm
MAX
FLOW
RET.
ALTERNATIVE
PREFERRED
RET.
CYLINDER
FLOW
HEATING
0392