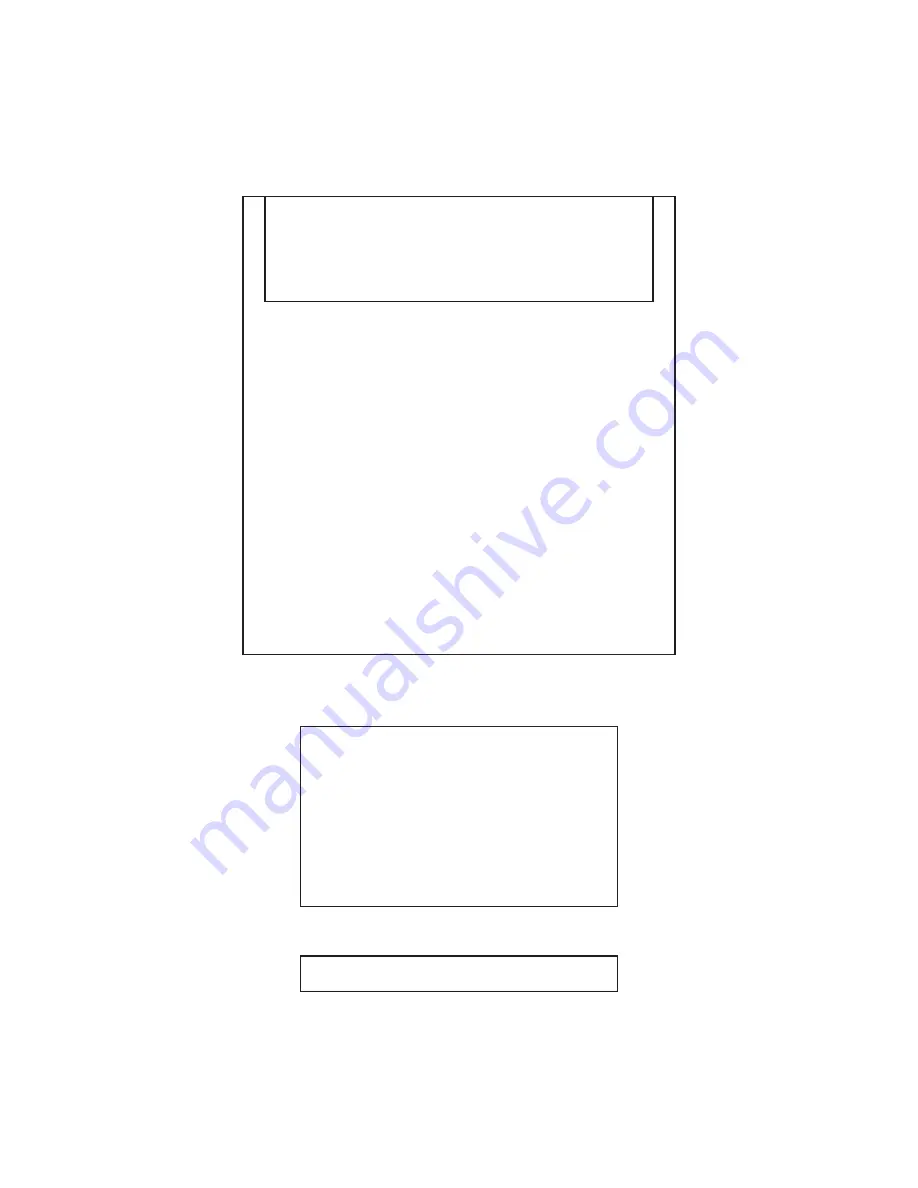
- Do not store or use gasoline or other flammable
vapors and liquids in the vicinity of this or any
other appliance.
- WHAT TO DO IF YOU SMELL GAS:
• Do not try to light any appliance.
• Do not touch any electrical switch; do not use
any phone in your building.
• Immediately call your gas supplier from a
neighbour’s phone. Follow the gas supplier’s
instructions.
• If you cannot reach your gas supplier, call the
fire department.
WARNING:
If the information in this manual
is not followed exactly, a fire or explosion
may result causing property damage, personal
injury or loss of life.
WARNING:
Improper installation,
adjustment, alteration, service or
maintenance can cause injury
or property damage. Read the
installation, operating and maintenance
instructions thoroughly before installing
or servicing this equipment.
WARNING:
For Outdoor Use Only
Summary of Contents for S-8500
Page 4: ......
Page 6: ......
Page 28: ...Global Power Technologies 22 S 8500 This page is purposely left blank ...
Page 63: ...Global Power Technologies 57 S 8500 Figure 29 CP Panel wiring schematic ...
Page 65: ...Global Power Technologies 59 S 8500 Figure 30 DC DC Converter Connections ...
Page 66: ...Global Power Technologies 60 S 8500 Figure 31 DC DC Converter with CP Panel wiring schematic ...
Page 72: ...Global Power Technologies 66 S 8500 Figure 32 Flowchart Battery Charging Application Setup ...