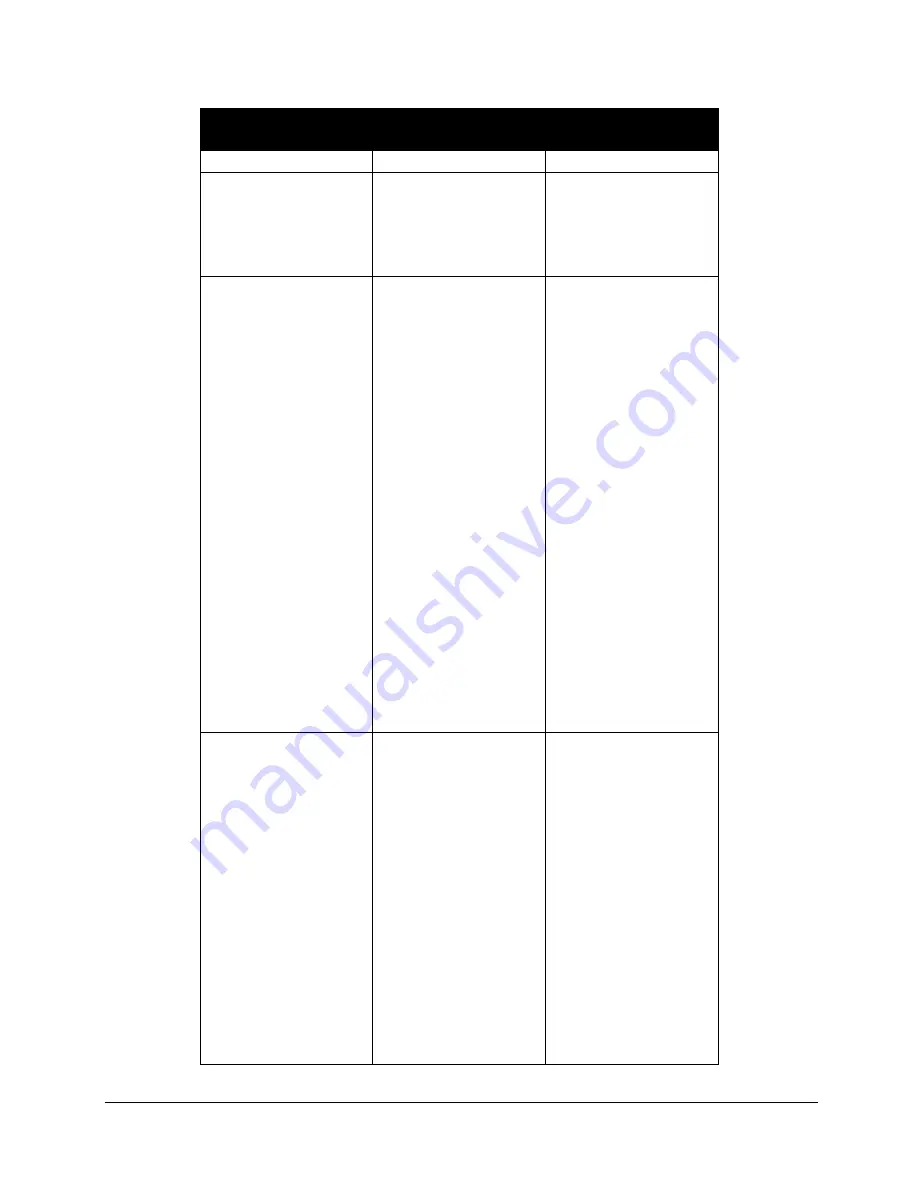
Airmac Owner’s Manual
August 2006
© Glenco Manufacturing Pty Ltd
Page 35 of 44
TABLE 5
TROUBLESHOOTING CHART
Symptom
Possible Cause
Corrective Action
compressor pump valves
and/or blown cylinder
head gaskets.
6. Compressor pump
partially seized.
pump valves and/or
cylinder head gaskets.
6. Repair or replace
compressor pump.
Excessive noise (including
knocking and rattling) or
vibration.
1. Loose engine/motor
and/or compressor
pulleys. V-belts too tight
or misaligned.
2. Low oil level.
3. Pistons hitting the cylinder
heads.
4. Damaged or worn
crankshaft bearings,
crankpin bearings,
crankshaft, connecting
rods, piston pin bearings,
piston pins, pistons,
cylinders and/or valves.
5. Faulty non-return valve.
6. Loose fasteners.
7. Engine fault.
1. Tighten or replace pulleys
as required, check
alignment and adjust V-
belt tension.
2. Add oil.
3. Remove cylinder heads
and check for carbon
deposits or other foreign
matter on top of pistons.
4. Replace components or
entire compressor pump.
5. Repair or replace non-
return valve.
6. Check and tighten
fasteners (including foot
mounts).
7. See engine manual.
Slow pressure rise or unable
to reach cut-out pressure.
1. Air demand exceeds
compressor pump
capacity.
2. Air leaks.
3. Blocked or dirty inlet air
filters.
4. Loose engine/motor
pulley, loose compressor
pump pulley, or
loose/worn V-belts.
5. Head unloaders not fully
retracting (usually
indicated by air blowing
out from air filter inlets).
1. Reduce air demand or
use larger or additional
compressor(s).
2. Tighten, refit or replace
leaking connections or
components.
3. Clean or replace air filter
elements.
4. Tighten or replace pulleys
as required, check
alignment and adjust V-
belt tension.
5. Repair or replace head
unloaders.