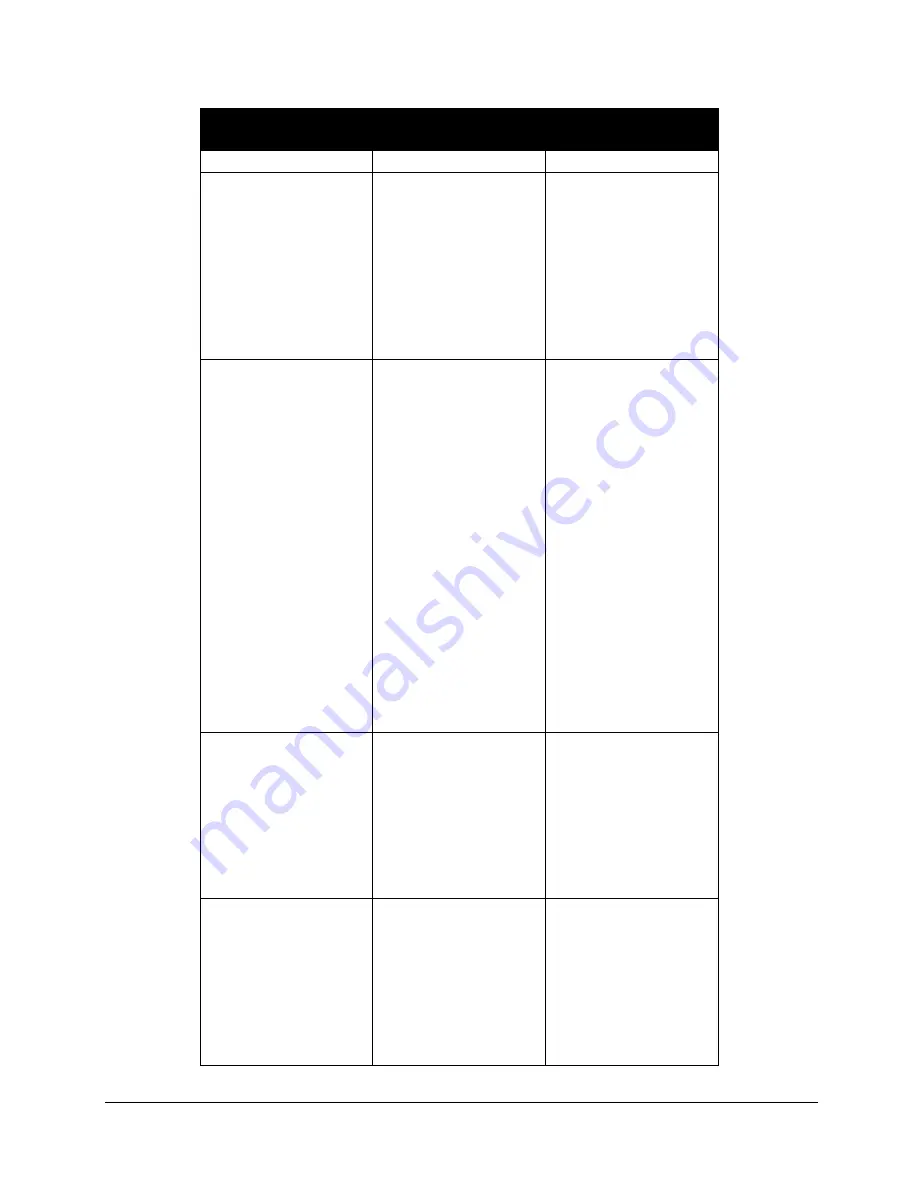
Airmac Owner’s Manual
August 2006
© Glenco Manufacturing Pty Ltd
Page 36 of 44
TABLE 5
TROUBLESHOOTING CHART
Symptom
Possible Cause
Corrective Action
6. Damaged or worn
compressor pump valves
and/or blown cylinder
head gaskets.
7. Damaged or worn piston
rings, pistons and/or
cylinders.
8. Faulty non-return valve.
6. Replace compressor
pump valves and/or
cylinder head gaskets.
7. Replace components or
entire compressor pump.
8. Repair or replace non-
return valve.
Compressor pump runs
excessively hot (and possibly
melts air filter enclosures).
1. Incorrect direction of
rotation.
2. Ambient temperature too
high or insufficient
ventilation.
3. Low oil level.
4. Excessive duty cycle.
5. Damaged or worn
compressor pump valves
and/or blown cylinder
head gaskets.
1. Check compressor pulley
turns anti-clockwise
(looking onto pulley).
Change electric motor
connections if incorrect.
2. Reduce ambient
temperature and/or
improve ventilation (e.g.
move further away from
walls or other equipment).
3. Add oil.
4. Reduce air demand or
use larger or additional
compressor(s).
5. Replace compressor
pump valves and/or
cylinder head gaskets.
Excessive cycling between
pumping mode and
unloading or off mode.
1. Excessive duty cycle.
2. Air leaks.
3. Excessive condensate in
air receiver tank.
1. Reduce air demand or
use larger or additional
compressor(s).
2. Tighten, refit or replace
leaking connections or
components.
3. Drain air receiver tank.
Excessive oil in discharge
air.
1. Blocked or dirty inlet air
filters.
2. Overfilled with oil.
3. Low oil viscosity.
4. Excessive duty cycle.
1. Clean or replace air filter
elements.
2. Drain oil down to high
level mark.
3. Replace with correct oil.
4. Reduce air demand or
use larger or additional
compressor(s).