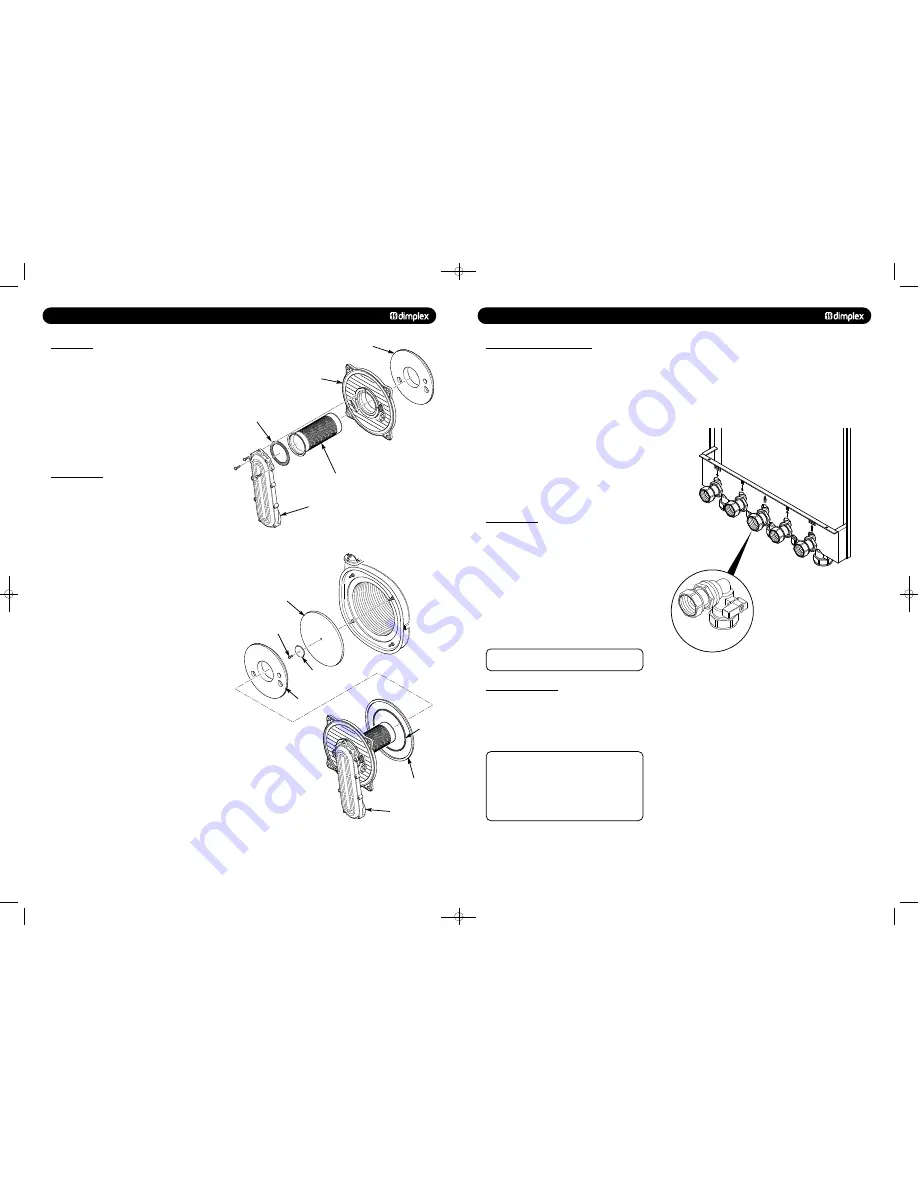
13.0
CHANGING COMPONENTS
13.4
BURNER
1. Remove the valve and fan assembly as described in Section
13.3.
2. Examine the gasket and replace if necessary.
3. Undo the four nuts securing the burner door and remove
from the heat exchanger.
4. Slowly withdraw the burner from the burner plate taking
care not to damage the insulation (Fig. 58).
5. Reassemble in reverse order.
34
© Dimplex Boilers 2008
13.5
INSULATION
1. Remove the electrode leads, noting their positions. Remove
the electrodes as described in section 13.2.
2. Remove the valve and fan assembly as described in Section
13.3.
3. Examine the gasket and replace if necessary.
4. Undo the four nuts securing the burner door and remove
from the heat exchanger.
5. Slowly withdraw the burner from the burner door.
6. Replace the insulation if necessary.
7. Check the burner door seals.
8. The rear insulation is retained by a screw and large washer,
remove these and draw the insulation out of the heat
exchanger (Fig. 59).
9. Reassemble in reverse order.
Burner
Insulation
Gasket
Air/Gas Channel
Rear Insulation
Washer
Insulation
Retaining Screw
Burner Assembly
Burner Door
Burner Door Seal
Fig. 58
Fig. 59
Inner Seal
7.0
SITE REQUIREMENTS
7.3
VENTILATION OF COMPARTMENTS
1. Where the appliance is installed in a cupboard or
compartment, no air vents are required.
Where an open flued system is used - Flue kit E (B23
classification) then an air vent communicating directly with
outside air must be provided in the same room or internal
space of the flue duct air inlet. Minimum free area:
Dimplex 24 = 88cm
2
Dimplex 30 = 121.5cm
2
Dimplex 38 = 159cm
2
In addition if an open flued system is used - Flue kit (B23
classification) and the boiler is fitted in a compartment, then
high and low level ventilation is required.
BS 5440-2:2000 gives guidance on compartmental ventilation.
2. When the boiler is installed in a cupboard or compartment
and either flue kit A, B, C, D or F (Classification C13, C33, C53)
is used, then no compartmental ventilation is required.
© Dimplex Boilers 2008
15
7.4
GAS SUPPLY
1. The gas installation should be in accordance with the
relevant standards. In GB this is BS 6891. In IE this is the
current edition of I.S. 813 “Domestic Gas Installations”.
2. The connection to the appliance is a 22mm copper tail
located at the rear of the gas service cock (Fig. 13).
3. Ensure that the pipework from the meter to the appliance is
of adequate size, and the demands of any other gas appliance
in the property are taken into consideration. Do not use pipes
of a smaller diameter than the boiler gas connection (22mm).
4. For boilers connected to use LPG (propane), the inlet
pressure must be 37mbar.
NOTE: The completed installation should always be tested
for gas tightness
7.5
ELECTRICAL SUPPLY
1. External wiring must be correctly earthed, polarised and in
accordance with relevant regulations/rules. In GB this is the
current I.E.E. Wiring Regulations. In IE reference should be
made to the current edition of the ETGI rules.
2. The mains supply is 230V - 50Hz fused at 3A
NOTE: The mains supply connection must allow complete
electrical isolation of the appliance and system controls
only.
Connection may be via a fused double-pole isolator with a
contact separation of at least 3mm in all poles and servicing
the boiler and system controls only.
Any additional mains cable should comply fully with the
current I.E.E. wiring regulations.
Fig. 13
Gas Service
Cock
48pp MANUAL SPREADS 19/10/10 08:36 Page 15