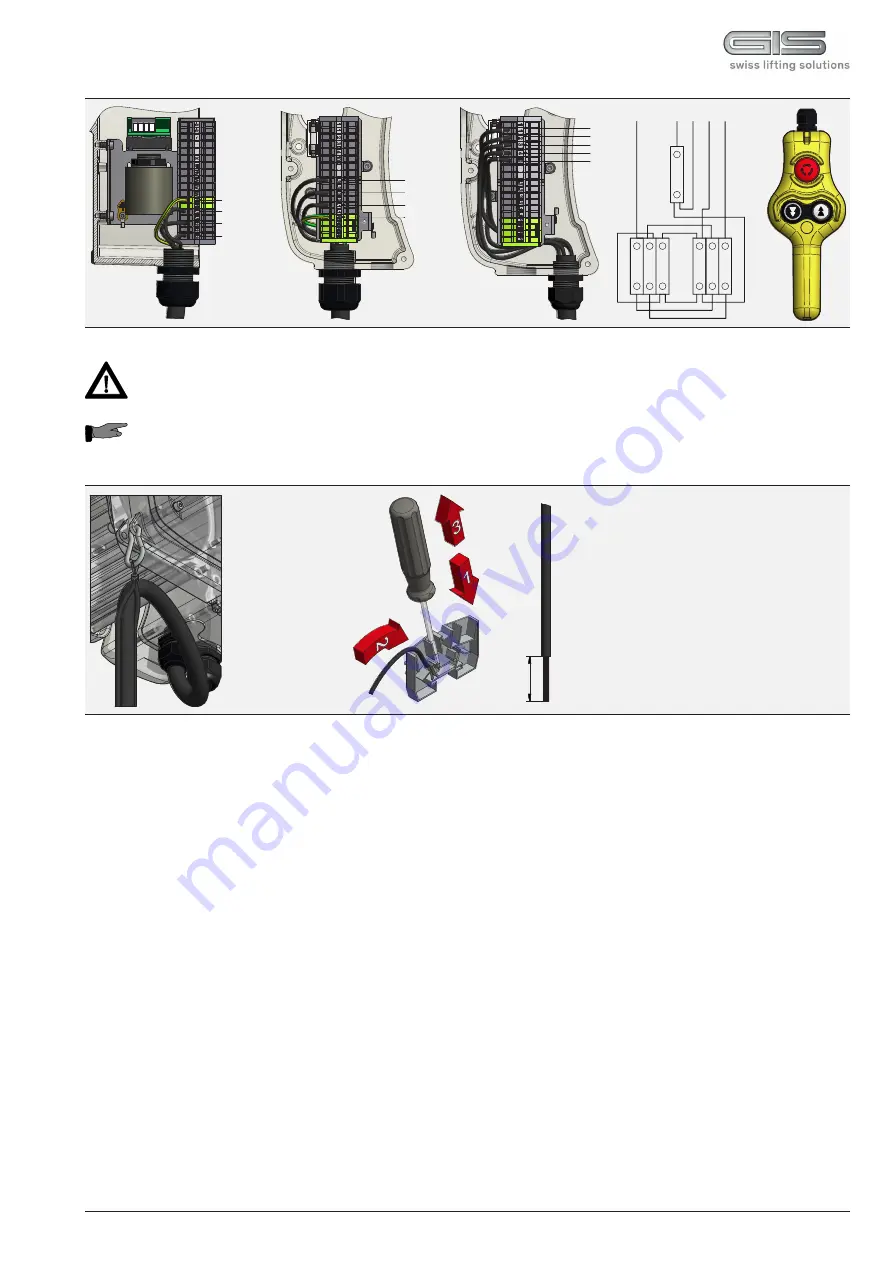
8-
9
m
m
NA
1
sp
ee
d
4
2
3
1
4
4
1
sp
ee
d
3
3
3
4
2
sp
ee
d
2
sp
ee
d
2
re
d
2
1
re
d
1
2
1 10 4 3
4
3
1
2
1
0
1
2
3
4
10
L3
L2
L1
PE
PE
L1 U
L2 V
L3 W
15
Swiss Lifting Solutions
2.2.2 Brake system
The brake must be able to hold the nominal load in power free mode without any problems. For chain hoists with two brakes, the functio-
nality of the two brakes must be checked during the system acceptance test. The first brake is on the DC side, the second brake on the AC
side and thereby switches with a slight delay.
The functional testing of the brake system is carried out under nominal load:
First brake:
Release the mounting screws of the second brake. The rotor of this brake now rotates freely. The function of the second brake is discon-
nected. Raise and lower: The first brake must be capable of braking and hold the nominal load. Tighten the mounting screws again after
the function test.
Second brake:
Electrical Method:
The first brake is released from + and - terminals and activated by a non-controlled current source (directly from L1 and L2). To activate a
rectifier must be switched between. Thus, the first brake is disconnected and the second brake can be tested by lifting and lowering the
load. Lifting and lowering with unloaded first brake: The second brake must be capable of braking and hold the nominal load. After the
function test reconnect the first brake to the ter and -.
Mechanical method:
With a tool, the pressure ring of the first brake is pressed to the solenoid, so that the rotor of the brake can rotate freely. The function of
the first brake is disconnected. Lifting and lowering with unloaded first brake: The second brake must be capable of braking and hold the
nominal load.
Figure 2-4
Figure 2-5
• Checking direction of rotation: If the directions of movement do not match the button symbols of the control switch,
the supply line wires L1 and L2 must be transposed.
• In the single-phase version, inching operations can cause malfunctions.
Open the terminal used in accordance with figure 2-5.
Figure 2-1
Figure 2-2
Figure 2-3