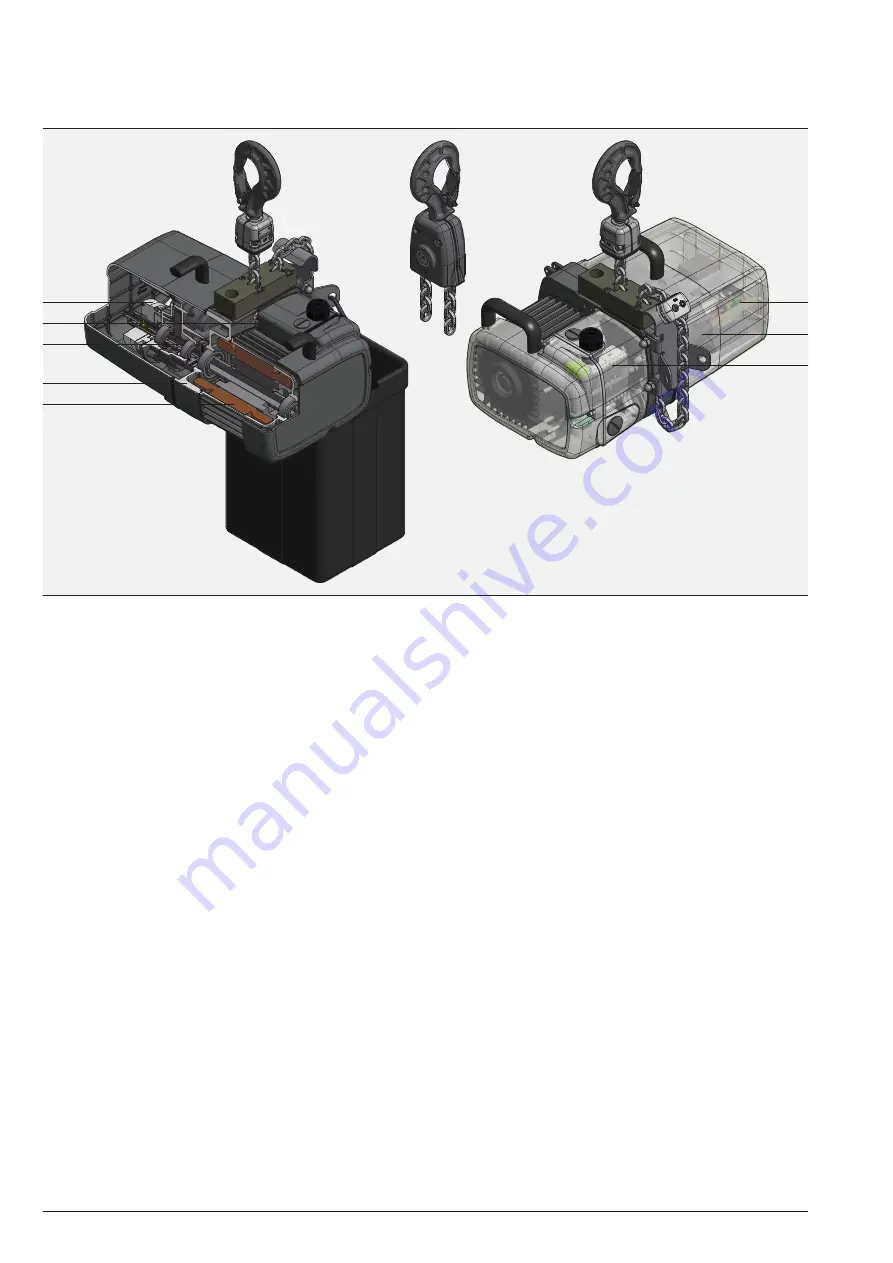
12
Swiss Lifting Solutions
The electric chain hoist meets the requirements of the EC Machinery Directive and the harmonized EN standards. Housing and cover of
the electric chain hoist are made of a sturdy die-cast aluminium. Cooling fins on the attached motor ensure optimum cooling. The chain
container can be attached to the compactly constructed housing. A drilled hole is provided for the power supply cable gland and for the
cable gland for the control cable. The eyebolt suspension or optional hook suspension are attached on the housing. The electric chain
hoists of the LP series are suitable for use as a climbing hoist. Two carrying handles (figure 1-2) facilitate the transport of the chain hoists.
GIS electric chain hoists are driven by asynchronous motors. The braking system consists of one (D8) or two (D8 PLUS, C1) DC-operated
magnetic brakes. When there is no current, pressure springs generate the braking torque.
The slipping clutch is installed in front of of the braking system due to its function. It protects the chain hoist from overload and takes on the
function of an emergency stop for the highest and lowest hook positions. The electric chain hoists of the LP series are suitable for direct
control.
The high tensile profile steel chain corresponds to grade DAT (8SS) per DIN EN 818-7. The chain wheel is hardened. The load hook, which
complies with DIN 15401 / DIN EN 13001, is fitted with a safety catch. The 3-stage enclosed spur gears are generally helical. The gears
are mounted on roller bearings and run with grease lubrication.
Additional equipment of D8 PLUS electric chain hoists (only available with the LPM/LP models):
• static safety factor of at least 8 with regard to fracture, in accordance with DIN 56950 (at least 8 per IGVW SQ P2)
• second parallel brake (figure 1-3)
Additional equipment of C1 electric chain hoists (only available with the LP model):
• static safety factor of at least 8 with regard to fracture per DIN 56950
• second parallel brake (figure 1-3)
• geared limit switch with downstream emergency limit switch (figure 1-4, Pos. 1)
• incremental encoders on the chain wheel (figure 1-4, Pos. 2)
• suspension with integrated load sensor (figure 1-5)
Options:
• integrated contactor control with or without emergency stop contactor (figure 1-6)
• safety load hooks (figure 1-7)
• absolute encoder
5) Motor
6) Limit switch (option)
7) Transmission
8) Electrical control (option)
1) Brake
2) Control unit box
3) Rotor shaft
4) Housing
6
7
8
1
2
3
4
5
Double fall
Single fall
Figure 1-1
1.2 General description