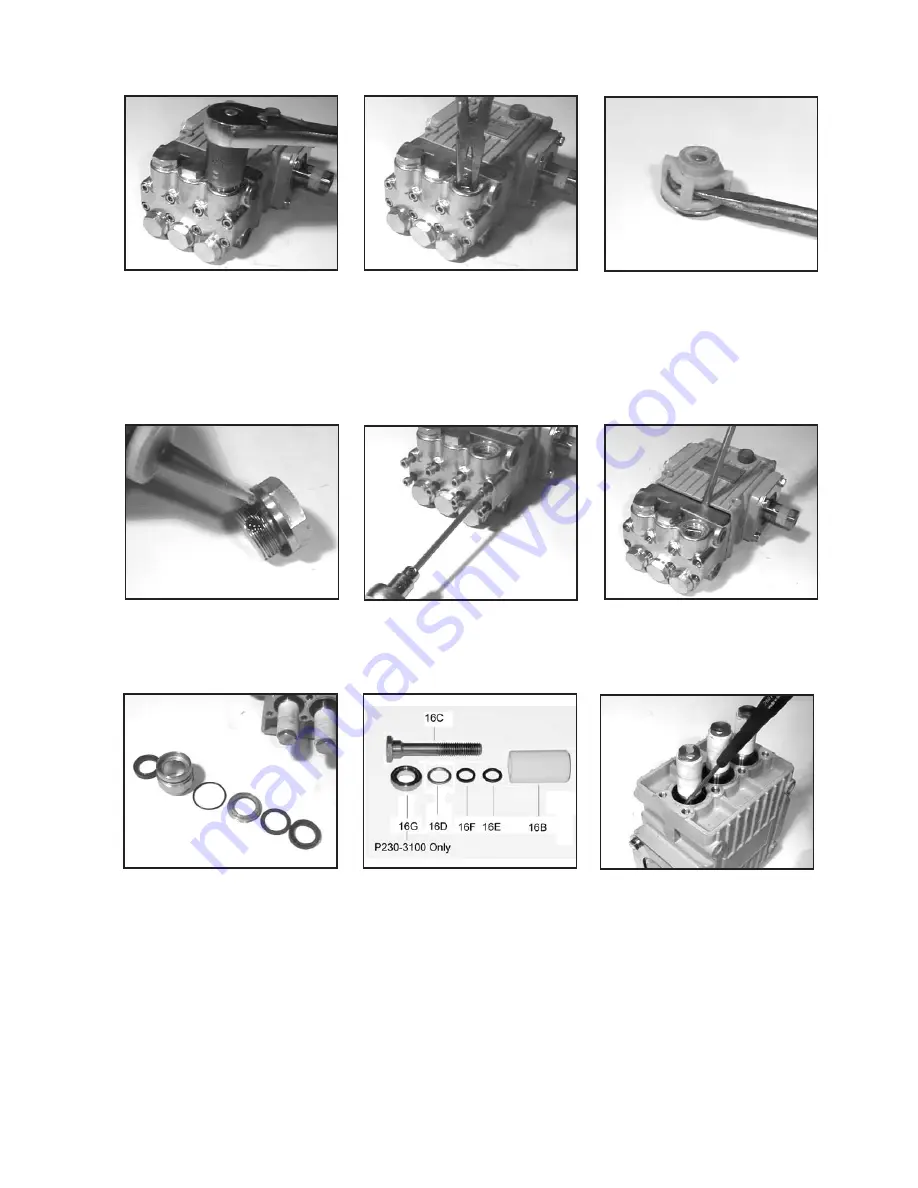
6
REPAIR INSTRUCTIONS - P200A-3100 SERIES
1. With a 22mm socket
wrench, remove the (3)
discharge valve plugs and
(3) inlet valve plugs (32)
Inspect the o-ring (33) for
wear and replace if dam-
aged.
2. Using a needle nose pliers,
remove the inlet and dis
-
charge valve assemblies
(27-30), for P230-3100 only,
remove spacer (30A), and
o-ring (31).
Inspect all parts
for wear and replace as nec-
essary.
3. By inserting a small screw
driver between the valve
seat (27) and the valve
spring retainer (30), the
valve assembly can be sepa-
rated.
7. Remove the weep return
ring (25), pressure ring
(24), and v-sleeve (23)
from the valve casing (26).
Remove the rear v-sleeve
(23A) from the seal case
(20). Inspect all parts, in
-
cluding o-ring (21) for wear
and replace as necessary.
8.Check surfaces of plunger pipe
(16B). A damaged surface will cause
accelerated wear on the seals. De
-
posits of any kind must be carefully
removed from the plunger surface. A
damaged plunger must be replaced!
When replacing the crush washer
(item 16D), make sure the rolled side
of the crush washer is placed on the
ceramic. Prior to installation, care-
fully crush the seal ring on a hand
press.
9. If the crankcase oil seals
(19) are to be replaced,
they can be removed by
prying loose with a flat
screwdriver. Take care not
to make contact with the
plunger.
4. Apply one drop of Loctite
243 to the valve plugs (32)
and tighten to 33 ft.-lbs.
5. Next, use a 5mm allen
wrench to remove the 8
socket head cap screws
(34).
6. Carefully slide the valve
casing (26) out over the
plungers.